Hydraulic hose specifications are crucial for ensuring the safe and effective operation of hydraulic systems. These specifications outline the hose’s construction, performance characteristics, and suitability for specific applications. Two prominent standards that govern hydraulic hose specifications are SAE (Society of Automotive Engineers) and ISO (International Organization for Standardization).
This guide will delve into the key aspects of SAE and ISO hydraulic hose specifications, providing a comprehensive understanding of these critical standards.
What Are Hydraulic Hose Specifications
Hydraulic hose specifications are crucial for selecting the right hose for a specific application. These specifications define the hose’s characteristics and performance capabilities, ensuring safe and reliable operation.
Key hydraulic hose specifications include:
- Inner Diameter (ID): This determines the flow capacity of the hose. A larger ID allows for greater fluid flow.
- Outer Diameter (OD): This influences the hose’s overall size and its ability to fit within confined spaces.
- Working Pressure: This indicates the maximum pressure the hose can withstand during normal operating conditions.
- Burst Pressure: This represents the maximum pressure the hose can withstand before rupturing.
- Temperature Range: This specifies the temperature limits within which the hose can operate safely and effectively.
- Fluid Compatibility: This indicates the types of hydraulic fluids the hose is compatible with, such as mineral oil, synthetic fluids, or water-based fluids.
- Bend Radius: This specifies the minimum radius to which the hose can be bent without damage or excessive stress.
- Construction Materials: This includes the materials used for the hose’s inner tube, reinforcement layers (such as wire braid or textile), and outer cover.
By carefully considering these specifications and selecting hoses that meet the demands of the specific application, you can ensure optimal system performance, minimize the risk of failures, and enhance the overall safety and reliability of your hydraulic equipment.
Hydraulic Hose SAE Standards
SAE standards play a crucial role in ensuring the safety, reliability, and interchangeability of hydraulic hoses. These standards, developed by the Society of Automotive Engineers, outline specific performance requirements for various types of hydraulic hoses.

SAE standards cover a wide range of aspects, including:
Construction: They specify the materials used in hose construction, such as the inner tube, reinforcement layers (wire braid, textile), and outer cover.
Performance Characteristics: SAE standards define key performance parameters, including:
- Working Pressure: The maximum pressure the hose can withstand during normal operating conditions.
- Burst Pressure: The maximum pressure the hose can withstand before rupturing.
- Temperature Range: The operating temperature limits within which the hose can safely function.
- Bend Radius: The minimum radius to which the hose can be bent without damage or excessive stress.
- Fluid Compatibility: The types of hydraulic fluids the hose is designed to handle.
Testing Procedures: SAE standards outline specific testing procedures to ensure that hoses meet the required performance criteria.
By adhering to SAE standards, manufacturers can produce consistent and reliable hydraulic hoses, while end-users can make informed decisions when selecting and installing hoses for their specific applications.
SAE standards contribute to:
- Improved Safety: By ensuring that hoses can withstand the pressures and temperatures encountered in real-world applications, SAE standards help to minimize the risk of hose failures, which can lead to fluid leaks, equipment damage, and potential injuries.
- Enhanced Interchangeability: SAE standards facilitate the use of interchangeable components from different manufacturers, simplifying maintenance and repair procedures.
- Increased Reliability: Adherence to SAE standards helps to ensure the consistent quality and reliability of hydraulic hoses, leading to improved system performance and reduced downtime.
SAE standards are essential for the safe and reliable operation of hydraulic systems. By selecting hoses that meet or exceed these standards, you can enhance the overall performance and longevity of your equipment.
Hydraulic Hose ISO Standards
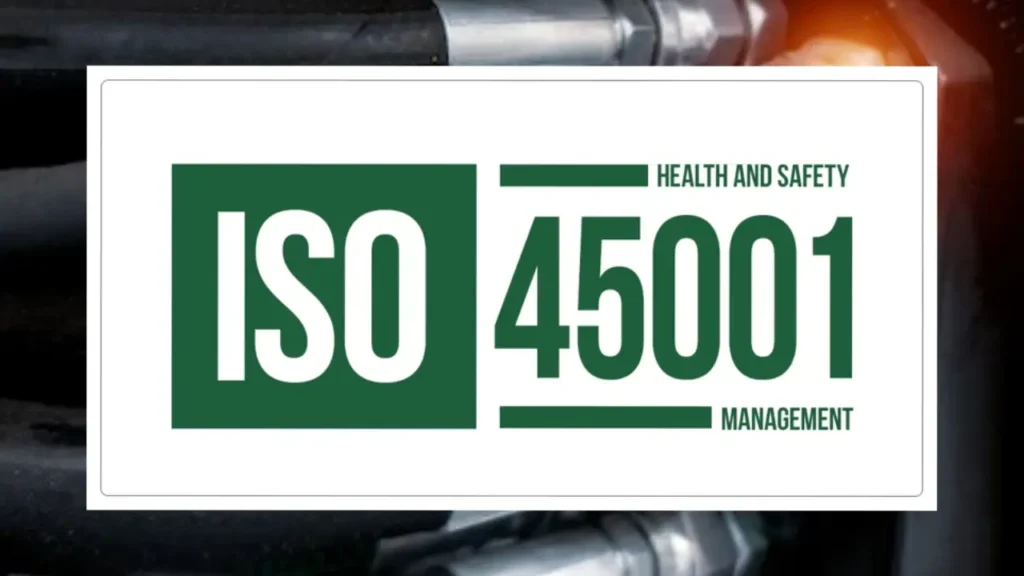
ISO standards provide a crucial framework for the design, manufacture, and performance of hydraulic hoses. These standards ensure consistency, quality, and safety across different manufacturers and applications.
Key ISO standards for hydraulic hoses include:
ISO 18752:
This standard classifies hydraulic hoses based on their resistance to impulse pressure, dividing them into four grades: A, B, C, and D. Each grade is further categorized by outside diameter into standard types (AS, BS, CS) and compact types (AC, BC, CC, DC). This classification system provides a clear understanding of a hose’s performance capabilities in various applications.
ISO 1436:
This standard specifies the construction and performance requirements for various types of hydraulic hoses, including single and double wire braided hoses. It outlines details such as pressure ratings, temperature capabilities, and suitable applications.
By adhering to these ISO standards, manufacturers can produce high-quality, reliable, and interchangeable hydraulic hoses, while end-users can make informed decisions when selecting hoses for their specific applications.
These standards contribute to enhanced safety, improved system performance, and reduced maintenance costs throughout the lifecycle of hydraulic systems.
Hydraulic Hose Testing Standards
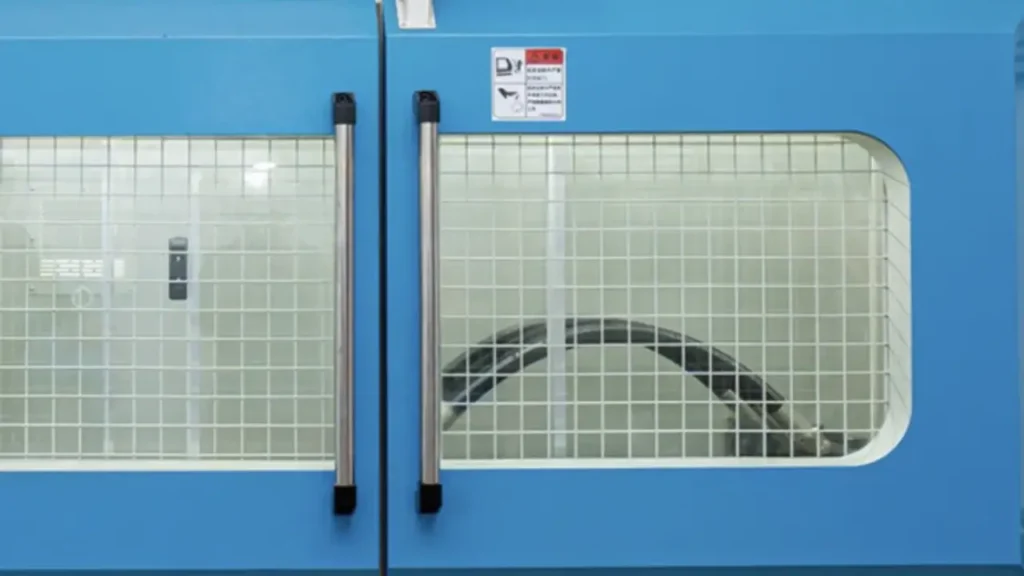
Hydraulic hose testing standards are crucial for ensuring the safety, reliability, and performance of these critical components. These standards outline rigorous testing procedures to evaluate hose performance under various conditions, ensuring they can withstand the demands of real-world applications.
Key aspects of hydraulic hose testing standards include:
Pressure Testing:
- Proof Test: This involves subjecting the hose to a pressure significantly higher than its working pressure for a specified duration. This test assesses the hose’s ability to withstand internal pressure without leaks or deformation.
- Burst Test: This test determines the maximum pressure the hose can withstand before rupturing. It provides crucial information about the hose’s pressure limits.
Temperature Testing:
- Temperature Cycling: Hoses are subjected to repeated cycles of extreme temperatures (both high and low) to evaluate their ability to withstand temperature fluctuations and maintain flexibility and performance.
- Cold Temperature Flexibility: Testing assesses the hose’s flexibility and resistance to cracking at low temperatures.
Fluid Compatibility Testing:
Hoses are tested with different hydraulic fluids to evaluate their compatibility and resistance to fluid degradation or swelling. This ensures that the hose material is not adversely affected by the fluid it will be carrying.
Abrasion Resistance Testing:
Hoses are subjected to controlled abrasion to evaluate their resistance to wear and tear. This is crucial for hoses operating in environments where they may come into contact with rough surfaces or abrasive materials.
Flex Fatigue Testing:
Hoses are subjected to repeated bending cycles to evaluate their resistance to fatigue and cracking. This is particularly important for hoses that are subjected to frequent bending or flexing during operation.
Test Type | Description |
---|---|
Proof Test | Subjecting the hose to a pressure significantly higher than its working pressure for a specified duration to assess its ability to withstand internal pressure without leaks or deformation. |
Burst Test | Determining the maximum pressure the hose can withstand before rupturing, providing crucial information about its pressure limits. |
Temperature Cycling | Repeatedly subjecting the hose to extreme temperatures (both high and low) to evaluate its ability to withstand temperature fluctuations and maintain flexibility and performance. |
Cold Temperature Flexibility | Assessing the hose’s flexibility and resistance to cracking at low temperatures. |
Fluid Compatibility | Testing the hose with different hydraulic fluids to evaluate its compatibility and resistance to fluid degradation or swelling. |
Abrasion Resistance | Subjecting the hose to controlled abrasion to evaluate its resistance to wear and tear. |
Flex Fatigue | Subjecting the hose to repeated bending cycles to evaluate its resistance to fatigue and cracking. |
By adhering to these rigorous testing standards, manufacturers can ensure that their hydraulic hoses meet the highest quality and performance standards, providing users with confidence in their reliability and safety.
Conclusion
Understanding and adhering to SAE and ISO standards is crucial for ensuring the safety, compatibility, and performance of hydraulic hoses. These standards provide a framework for consistent quality, interchangeability, and reliable operation across various applications. By selecting hoses that meet or exceed these standards, you can enhance the overall efficiency and longevity of your hydraulic systems.
For high-quality, durable, and SAE/ISO compliant hydraulic hoses, choose Kingdaflex. We offer a wide range of hoses designed to meet the most stringent industry standards. Contact us today to request a quote and discover how Kingdaflex can enhance your hydraulic system performance.