Hydraulic hoses are essential in various industries, powering everything from construction equipment to aerospace systems. Understanding the hydraulic hose manufacturing process behind these robust and flexible tubes can provide valuable insights into their construction and performance.
In this guide, we’ll delve into the step-by-step process of hydraulic hose manufacturing process, from raw material selection to the final product.
How to Make Hydraulic Hoses
While the large-scale manufacturing process of hydraulic hoses is a complex process that requires specialized machinery and expertise, here’s a simplified overview of the key steps involved:
Step 1. Material Selection:
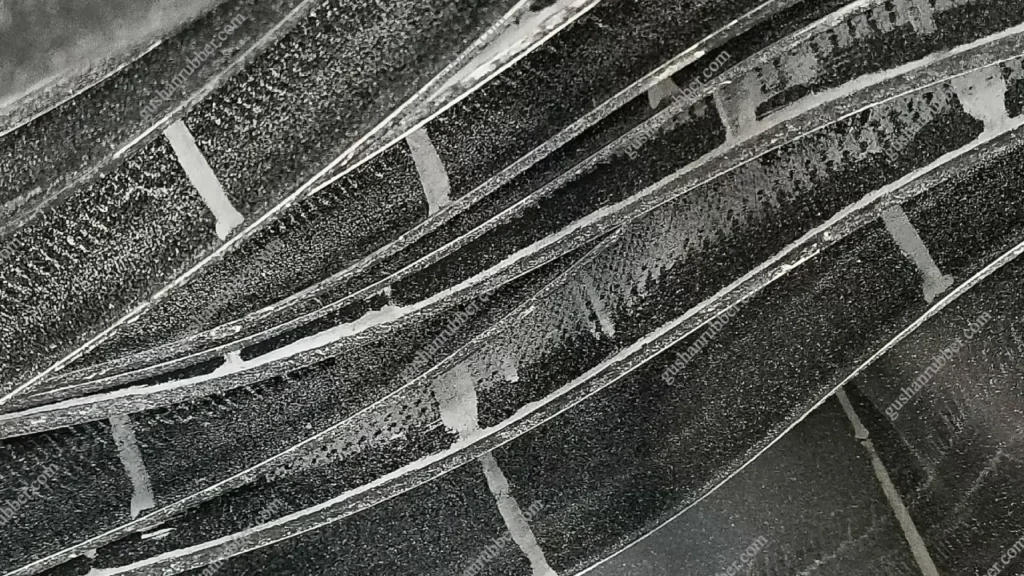
The selection of rubber materials for hydraulic hose manufacturing is crucial, as it directly impacts the hose’s performance, durability, and suitability for specific applications.
Rubber Material Selection for Hydraulic Hose Manufacturing
The selection of rubber materials for hydraulic hose manufacturing is crucial, as it directly impacts the hose’s performance, durability, and suitability for specific applications. Key factors to consider include:
1. Inner Tube Material:
Nitrile Rubber (NBR):
- Most commonly used due to its excellent resistance to petroleum-based hydraulic fluids.
- Offers good mechanical properties and temperature resistance.
- Suitable for a wide range of hydraulic applications.
2. Outer Cover Material:
Neoprene Rubber (CR):
- Provides excellent resistance to ozone, weathering, and flame.
- Good mechanical properties and flexibility.
- Often used in harsh environmental conditions.
Rubber (CR):
- Similar to Neoprene but with improved resistance to heat and oil.
- Offers good abrasion resistance and flexibility.
Ethylene-Propylene-Diene Monomer (EPDM):
- Excellent resistance to heat, ozone, and weathering.
- Good chemical resistance, especially to polar solvents and alkalis.
- Suitable for applications with exposure to high temperatures and harsh environments.
3. Reinforcement Layers:
- Steel Wire: Provides high-pressure resistance and strength.
- Textile Braids: Offer flexibility and kink resistance.
Key Considerations for Rubber Material Selection:
- Hydraulic Fluid Compatibility: Ensure the rubber material is compatible with the specific hydraulic fluid being used.
- Temperature Range: Consider the operating temperature range to select a material with appropriate thermal properties.
- Pressure Rating: Choose a material that can withstand the required operating pressure.
- Chemical Resistance: Select a material that is resistant to the chemicals and contaminants in the environment.
- Abrasion Resistance: If the hose is exposed to abrasive conditions, choose a material with good abrasion resistance.
- Flexibility: A flexible material is essential for easy installation and operation.
- Ozone Resistance: In outdoor applications, ozone resistance is crucial to prevent cracking and deterioration.
- UV Resistance: For outdoor use, UV resistance is necessary to protect the hose from sunlight degradation.
By carefully considering these factors, manufacturers can select the optimal rubber materials to produce high-quality, durable, and reliable hydraulic hoses for a wide range of applications.
Would you like to delve deeper into a specific aspect of hydraulic hose manufacturing, such as material testing, quality control, or design considerations?
Step 2. Hydraulic Hose Tube Extrusion:
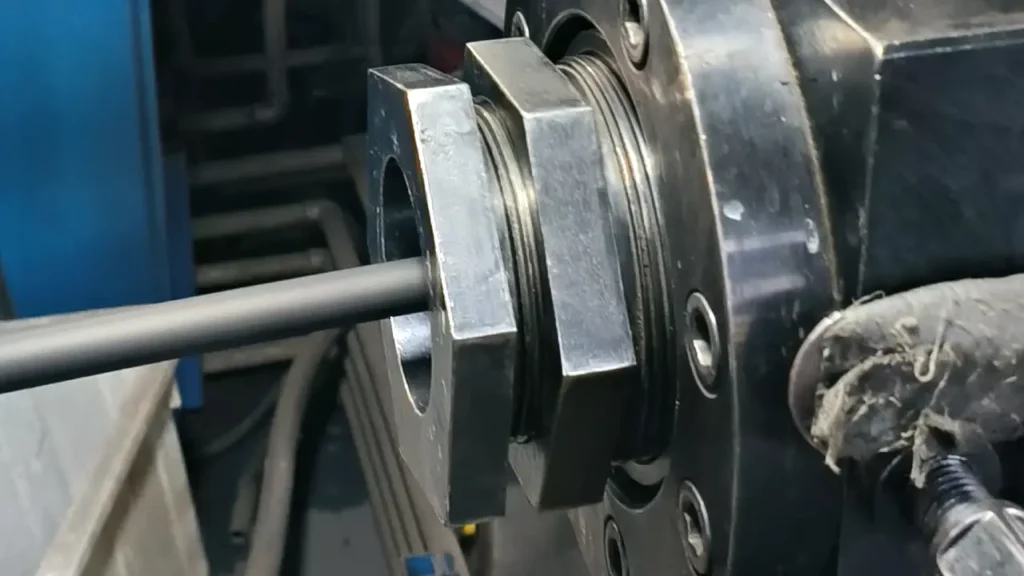
Hydraulic hose tube extrusion is a critical step in the manufacturing process of hydraulic hoses.
It involves shaping a rubber compound into a continuous tube that will form the inner layer of the hose. Here’s a breakdown of the process:
1. Material Preparation:
- Rubber Compound: A carefully formulated rubber compound, typically based on nitrile rubber (NBR), is prepared. This compound is selected for its excellent resistance to hydraulic fluids, heat, and abrasion.
- Compound Mixing: The rubber compound is mixed in a sophisticated mixing machine to ensure homogeneity and proper dispersion of additives.
2. Extrusion Process:
- Extruder Machine: The prepared rubber compound is fed into an extruder machine, which consists of a screw that rotates within a heated barrel.
- Heating and Melting: As the compound moves through the extruder, it is heated and melted into a viscous state.
- Die: The molten rubber is forced through a precisely engineered die, which shapes it into the desired tube profile. The die can be designed to create various tube sizes and wall thicknesses.
- Cooling: The extruded tube is immediately cooled to solidify the rubber and maintain its shape.
3. Mandrel:
- A mandrel, a solid core, is often used during the extrusion process to maintain the tube’s inner diameter and ensure a smooth inner surface.
- The mandrel can be removed after the tube is cured, or it can be left in place for certain types of hoses.
4. Quality Control:
- Throughout the extrusion process, strict quality control measures are implemented to ensure that the tube meets the required specifications.
- Dimensions, wall thickness, and surface quality are inspected to guarantee product consistency and reliability.
Key Considerations in Hydraulic Hose Tube Extrusion:
- Material Selection: The choice of rubber compound is crucial for the hose’s performance in specific applications.
- Extrusion Parameters: Factors like temperature, pressure, and screw speed influence the tube’s quality and properties.
- Die Design: The die’s geometry determines the tube’s shape, size, and wall thickness.
- Cooling Process: Proper cooling is essential to prevent defects and maintain dimensional accuracy.
- Mandrel Selection: The mandrel’s material and surface finish can affect the tube’s inner surface quality.
By carefully controlling these factors, manufacturers can produce high-quality hydraulic hose tubes that meet the demanding requirements of various industries, including construction, agriculture, and manufacturing.
Step 3. Reinforcement Layer Manufacturing
Reinforcement layers are crucial components of hydraulic hoses, providing the necessary strength and durability to withstand high pressures and harsh operating conditions. The manufacturing process involves several key steps:
1. Material Selection:
- Steel Wire: The most common material for reinforcement, offering high tensile strength and pressure resistance.
- Synthetic Fibers: Materials like polyester, nylon, and aramid fibers are used for flexibility and resistance to fatigue.
2. Wire Drawing and Treatment:
- Wire Drawing: Steel wire is drawn through dies to achieve the desired diameter and tensile strength.
- Heat Treatment: The wire may undergo heat treatment processes like annealing or tempering to improve its mechanical properties.
3. Braiding or Winding:
- Braiding: Multiple strands of wire or fiber are interlaced to form a braided reinforcement layer. This technique provides excellent flexibility and resistance to bending.
- Winding: Wire or fiber is wound spirally around the hose tube to create a reinforcement layer. This method is suitable for high-pressure applications.
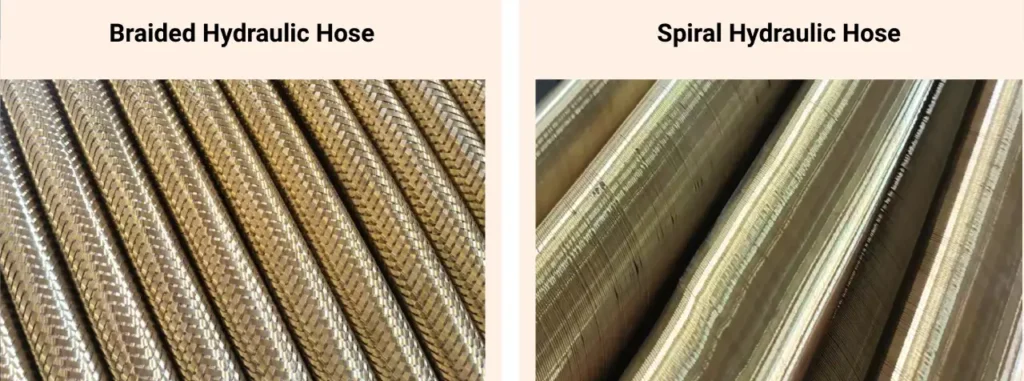
Hydraulic Hose Reinforcement: Braiding vs. Spiraling
The reinforcement layer is a critical component of a hydraulic hose, providing the necessary strength and durability to withstand high pressures and harsh operating conditions. Two common methods for reinforcing hydraulic hoses are braiding and spiraling.
Process: Multiple strands of wire or fiber are interlaced in a crisscross pattern around the hose tube.
Advantages:
High flexibility
- Good resistance to bending fatigue
- Suitable for applications requiring frequent movement and bending
Hydraulic Hose Spiraling
Process: Wire or fiber is wound spirally around the hose tube, layer by layer.
Advantages:
- High-pressure capability
- Excellent resistance to pressure surges and impulses
- Suitable for high-pressure, high-impulse applications
Choosing the Right Reinforcement:
The choice between braided and spiral reinforcement depends on the specific application and the required performance characteristics:
- High Flexibility: Braided hoses are generally more flexible and suitable for applications requiring frequent bending and movement.
- High Pressure and Impulse Resistance: Spiral hoses are better suited for high-pressure, high-impulse applications, such as those found in heavy-duty equipment.
By understanding the strengths and weaknesses of each reinforcement method, engineers can select the appropriate hose for specific applications, ensuring optimal performance and reliability.
4. Application to the Hose Tube:
- Adhesive Bonding: The reinforcement layer is applied to the hose tube using a high-strength adhesive.
- Heat Bonding: In some cases, heat is applied to bond the reinforcement layer to the tube.
5. Curing:
- The hose, with the applied reinforcement layer, is cured in a high-temperature oven to ensure a strong bond between the layers.
Key Considerations:
- Reinforcement Layer Thickness: The thickness of the reinforcement layer is determined by the required pressure rating and flexibility of the hose.
- Layer Orientation: The orientation of the reinforcement layers can influence the hose’s bending radius and pressure resistance.
- Adhesive Selection: The adhesive used must be compatible with both the rubber tube and the reinforcement material, providing a strong and durable bond.
- Curing Process: The curing process must be carefully controlled to ensure optimal bonding and mechanical properties.
By carefully selecting materials and controlling the manufacturing process, manufacturers can produce high-quality hydraulic hoses that meet the demanding requirements of various industries.
Step 4. Outer Cover Extrusion (Same as the Inner Tube Extrusion)
The outer cover is the final layer of a hydraulic hose, protecting environmental factors such as abrasion, ozone, UV radiation, and extreme temperatures.
Here’s a breakdown of the outer cover extrusion process:
1. Material Selection:
Rubber Compounds: A variety of rubber compounds are used for outer covers, with the most common being:
- Neoprene (CR): Offers excellent resistance to ozone, weather, and flame.
- Chloroprene Rubber (CR): Similar to Neoprene but with improved heat and oil resistance.
- Ethylene-Propylene-Diene Monomer (EPDM): Provides excellent resistance to heat, ozone, and weathering.
2. Extrusion Process:
- Extruder Machine: The rubber compound is fed into an extruder machine, similar to the process used for the inner tube.
- Heating and Melting: The compound is heated and melted to a viscous state.
- Die: The molten rubber is forced through a die, which shapes it into a tube with the desired thickness and profile.
- Cooling: The extruded outer cover is cooled to solidify the rubber and maintain its shape.
3. Application to the Hose:
- Adhesive Bonding: The outer cover is applied to the reinforced hose tube using a high-strength adhesive.
- Heat Bonding: In some cases, heat is applied to bond the outer cover to the tube.
4. Curing:
- The entire hose assembly is cured in a high-temperature oven to ensure a strong bond between the outer cover and the underlying layers.
Key Considerations:
- Material Selection: The choice of rubber compound depends on the specific application and the environmental conditions the hose will be exposed to.
- Extrusion Parameters: Factors such as temperature, pressure, and die design influence the outer cover’s quality and properties.
- Adhesive Selection: The adhesive must be compatible with both the rubber compound and the reinforcement layer, providing a strong and durable bond.
- Curing Process: The curing process is critical for achieving optimal mechanical properties and ensuring the long-term performance of the hose.
By carefully controlling these factors, manufacturers can produce high-quality hydraulic hoses with durable and protective outer covers.
Step 5. Vulcanization Process (Curing Process)
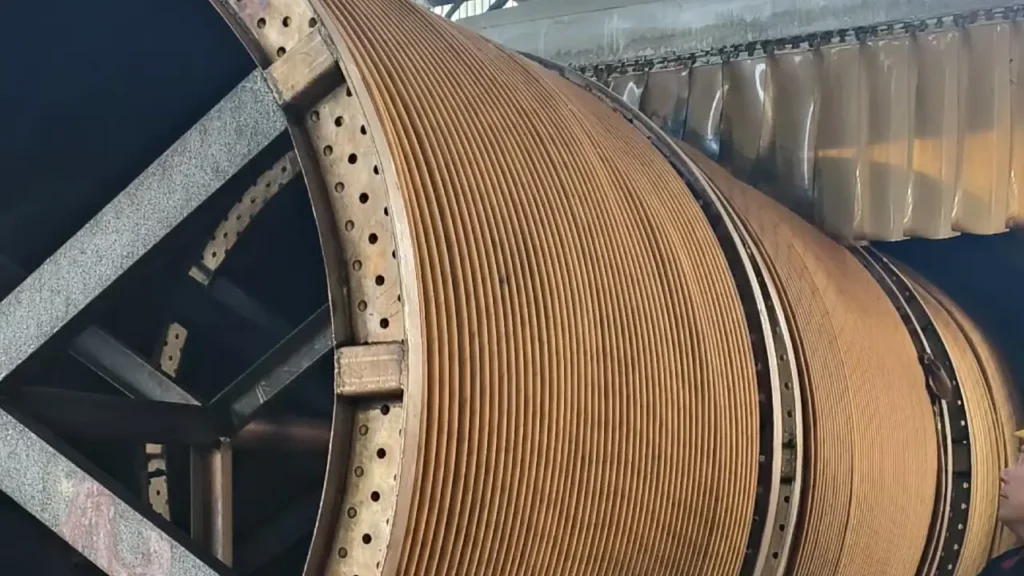
Vulcanization is a crucial step in the manufacturing process of hydraulic hoses. It involves heating the rubber components of the hose in the presence of a vulcanizing agent, typically sulfur, to create cross-links between the polymer chains.
This process transforms the raw rubber into a durable and resilient material.
Key Steps in the Vulcanization Process:
Preparation:
- The assembled hydraulic hose, consisting of the inner tube, reinforcement layers, and outer cover, is prepared for vulcanization.
- The hose is often wrapped in a protective cloth to prevent damage during the curing process.
Vulcanization Chamber:
- The prepared hose is placed in a vulcanization chamber, which can be a steam-heated autoclave or a hot air oven.
Curing Process:
- Heat and Pressure: The chamber is heated to a specific temperature and pressure.
- Sulfur Cross-Linking: The heat and pressure activate the vulcanizing agent, causing sulfur atoms to bond with the rubber molecules. This creates cross-links that strengthen the rubber’s molecular structure.
Cooling and Post-Curing:
- Once the curing cycle is complete, the hose is cooled gradually to prevent thermal stress and cracking.
- In some cases, post-curing may be necessary to complete the vulcanization process and improve the hose’s properties.
Benefits of Vulcanization:
- Increased Strength and Durability: Vulcanization significantly improves the hose’s tensile strength, tear resistance, and abrasion resistance.
- Improved Elasticity: The cross-linking process enhances the hose’s elasticity, allowing it to flex without cracking.
- Enhanced Heat Resistance: Vulcanized rubber can withstand higher temperatures without degrading.
- Resistance to Chemical Attack: Vulcanization can improve the hose’s resistance to various chemicals and oils.
By carefully controlling the vulcanization process, manufacturers can produce high-quality hydraulic hoses that meet the demanding requirements of various industries.
Step 6. Testing and Inspection:
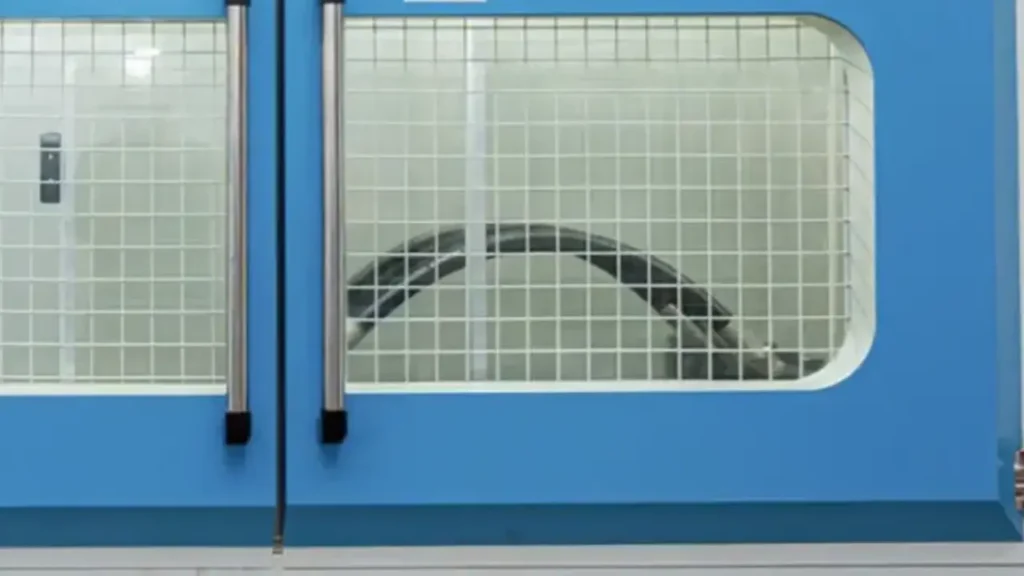
Hydraulic hoses are subjected to rigorous testing to ensure their reliability, durability, and safety. Here are some of the common tests performed on hydraulic hoses:
1. Pressure Testing:
- Working Pressure: This is the maximum pressure at which the hose is designed to operate continuously. It’s the standard operating pressure for the hose. (You can see the working pressure value printed on the hydraulic hose layline)
- Testing Pressure: This is the pressure applied to the hose during quality control testing to verify its integrity. It’s typically 2 times the working pressure, which ensures the hose can withstand pressure fluctuations and spikes that may occur in real-world applications.
- Burst Pressure: This is the maximum pressure the hose can withstand before rupturing. It’s usually 4 times the working pressure, providing a significant safety margin.
Hydraulic Hose Pressure Ratings
Parameter | Description | Typical Ratio to Working Pressure |
---|---|---|
Working Pressure | Maximum continuous operating pressure | 1x |
Testing Pressure | Pressure applied during quality control testing | 2x |
Burst Pressure | Maximum pressure before rupture | 4x |
Note: These are common industry standards, but specific ratios may vary depending on the hose type, manufacturer, and application. Always refer to the manufacturer‘s specifications for accurate pressure ratings.
2. Flex Testing:
- Flex Fatigue Test: This test evaluates the hose’s ability to withstand repeated bending. The hose is subjected to a specified number of flex cycles at a particular bend radius and frequency.
- Twist Test: This test assesses the hose’s resistance to twisting. The hose is twisted to a specific angle and held for a certain period.
3. Temperature Testing:
- Low Temperature Test: This test evaluates the hose’s flexibility and performance at low temperatures. The hose is subjected to cold temperatures and then tested for its ability to bend and withstand pressure.
- High Temperature Test: This test assesses the hose’s resistance to high temperatures. The hose is exposed to high temperatures and then tested for its mechanical properties and chemical resistance.
4. Chemical Resistance Testing:
- Fluid Compatibility Test: This test determines the hose’s compatibility with various hydraulic fluids. The hose is immersed in different fluids for a specified period, and its physical properties and chemical resistance are evaluated.
5. Abrasion Resistance Test:
- Abrasion Test: This test evaluates the hose’s resistance to wear and tear. The hose is subjected to abrasive materials, such as sand or metal particles, to assess its durability.
6. Ozone Resistance Test:
- Ozone Chamber Test: This test evaluates the hose’s resistance to ozone, a common cause of rubber degradation. The hose is exposed to ozone in a controlled environment to assess its cracking resistance.
7. UV Resistance Test:
- UV Exposure Test: This test evaluates the hose’s resistance to ultraviolet radiation. The hose is exposed to UV light to assess its color fading, cracking, and loss of mechanical properties.
8. Impulse Testing for Hydraulic Hoses
Impulse testing is a critical test for hydraulic hoses, especially those used in high-pressure applications. It simulates the sudden pressure surges that can occur in hydraulic systems, such as those caused by pump cavitation or valve slamming.
By conducting these tests, manufacturers can ensure that hydraulic hoses meet the required performance standards and are suitable for their intended applications.
Note: The specific hydraulic hose manufacturing process may vary depending on the types of hydraulic hose and the manufacturer’s techniques. However, the general steps outlined above provide a solid understanding of the basic process.
Step 7: Hydraulic Hose Packing Process
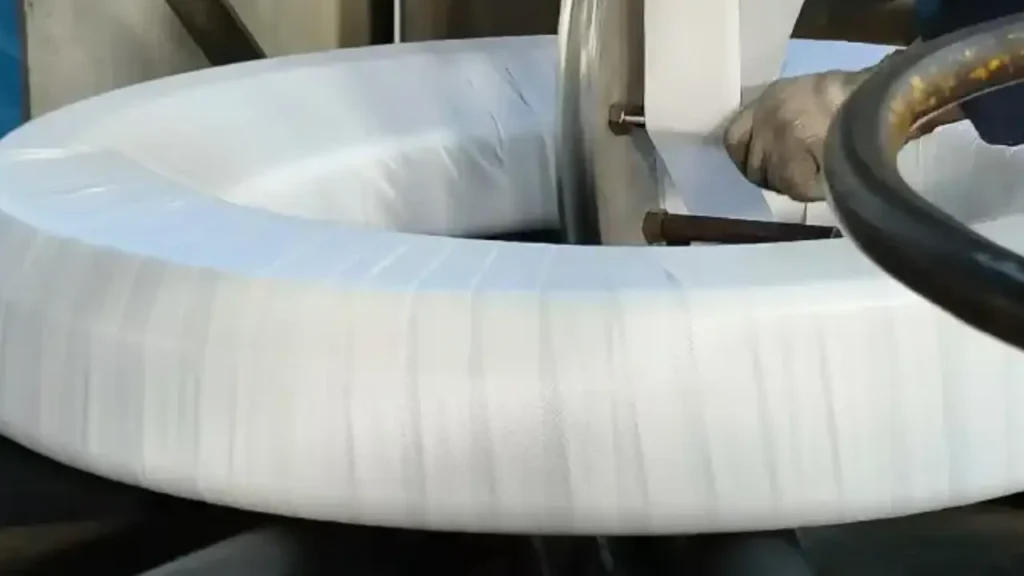
The packaging process for hydraulic hoses is crucial to ensure they arrive at their destination undamaged and ready for use.
Here are common methods used to pack hydraulic hoses:
1. Coiling and Wrapping:
- Coiling: Hoses are coiled neatly to avoid kinking or damage.
- Wrapping: The coiled hose is wrapped in protective materials like plastic film or woven bags to prevent abrasion and moisture damage.
2. Reel Packaging:
- Reeling: Hoses are wound onto reels, which provides a compact and organized way to store and transport them.
- Reel Protection: Reels are often wrapped or boxed to protect them during shipping.
3. Box Packaging:
- Boxing: Hoses are placed in sturdy cardboard boxes, often with additional protective padding to prevent damage.
- Labeling: Clear labeling is essential to identify the hose type, size, and other relevant information.
Key Considerations for Hydraulic Hose Packaging:
- Protection: The packaging should protect the hose from physical damage, moisture, and UV radiation.
- Storage: The packaging should allow for proper storage, preventing the hose from kinking or deforming.
- Transportation: The packaging should be durable enough to withstand the rigors of shipping and handling.
- Labeling: Clear and accurate labeling is crucial for identification and inventory management.
- Environmental Factors: The packaging materials should be environmentally friendly and comply with relevant regulations.
By following these guidelines, hydraulic hoses can be effectively packaged and transported, ensuring they reach their destination in optimal condition.
It’s important to note that the manufacturing of hydraulic hoses requires specialized equipment, expertise, and adherence to industry standards to ensure product quality and safety.
What Are Hydraulic Hoses Made Of
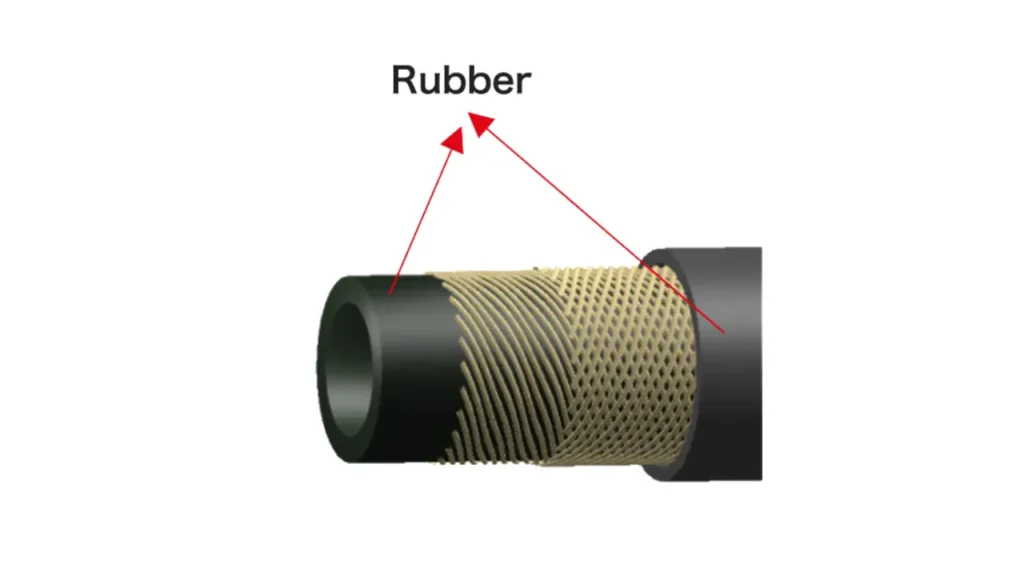
Hydraulic hoses are typically made of multiple layers:
- Inner Tube: This core layer is usually made of synthetic rubber such as nitrile or polyurethane. It’s designed to be resistant to the chemical properties, abrasion, and high temperatures of the hydraulic fluid.
- Reinforcement Layer: This layer is crucial for strength and pressure resistance. It’s often made of materials like steel wire, braided fibers, or a combination of both.
- Outer Cover: The outermost layer protects the hose from external damage like abrasion, weather, and other environmental factors. It’s commonly made of rubber or synthetic materials.
The specific materials and construction will vary depending on the intended application of the hose. Factors like the type of hydraulic fluid, operating pressure, temperature range, and environmental conditions all influence the hose’s design.
Places to Get Hydraulic Hoses Made
Where to Get a Hydraulic Hose Made
When you need a hydraulic hose, you have several options for where to get it made:
- Hydraulic Hose Shops: These specialized shops are your primary resource. They often have a wide selection of hoses, fittings, and the expertise to assemble hoses to your exact specifications. They can handle repairs, custom orders, and even emergency situations.
- Industrial Supply Stores: Many industrial supply stores carry a variety of hydraulic hoses and fittings. They may have limited custom assembly capabilities, but can provide readily available options and basic repair services.
- Equipment Dealers: If your equipment requires specific hoses, the dealer may be able to source or even manufacture them for you. They have a good understanding of your equipment’s needs and can ensure compatibility.
- Original Equipment Manufacturers (OEMs): In some cases, you may be able to obtain replacement hoses directly from the original manufacturer of your equipment.
Factors to Consider When Choosing Hydraulic Hoses:
- Urgency: If you need a hose immediately, a local hydraulic hose shop is often the fastest option.
- Complexity: For complex or custom hoses, a specialized shop with experienced technicians is crucial.
- Availability: Check the inventory and availability of hoses and fittings at your chosen location.
- Cost: Compare prices and services from different providers to find the most cost-effective solution.
By considering these factors and exploring your options, you can find the best place to get your hydraulic hoses made, ensuring reliable performance and minimal downtime for your equipment.
Conclusion
The manufacturing process of hydraulic hoses is a complex and precise operation that requires careful attention to detail. By understanding the key steps involved, we can appreciate the engineering and craftsmanship that goes into producing these essential components.
Need custom hydraulic hoses tailored to your specific requirements?
Gushan Rubber offers a wide range of customized hydraulic hose solutions. Our experienced team can work with you to design and manufacture hoses that meet your exact needs.
Contact us today to discuss your project and explore our custom hydraulic hose options.