Hydraulic hoses are critical components in many industries, from construction and manufacturing to agriculture and transportation.
Ensuring their integrity is paramount to the safety and efficiency of hydraulic systems. Regular and thorough testing of hydraulic hoses is essential to identify potential issues before they lead to catastrophic failures.
This guide provides a comprehensive overview of hydraulic hose testing procedures, covering various methods and techniques.
Hydraulic Hose Testing
Hydraulic hose testing is a critical process to ensure the safety and reliability of hydraulic systems. By regularly testing hydraulic hoses, you can identify potential issues early on and prevent costly breakdowns and accidents.
Types of Hydraulic Hose Testing
- Visual Inspection: This involves a thorough visual examination of the hose for signs of wear, cuts, cracks, or other damage.
- Pressure Testing: This test involves applying a specific pressure to the hose and monitoring for leaks or other signs of failure.
- Bend Test: This test evaluates the hose’s flexibility and resistance to bending stress.
- Twist Test: This test measures the hose’s ability to withstand twisting forces without damage.
- Abrasion Resistance Test: This test assesses the hose’s resistance to wear and tear from friction.
- Temperature Cycling Test: This test evaluates the hose’s performance at extreme temperatures.
- Fluid Compatibility Test: This test ensures that the hose is compatible with the specific fluid being used.
Importance of Hydraulic Hose Testing
- Safety: Regular testing helps identify potential failures before they occur, reducing the risk of accidents and injuries.
- Reliability: By identifying and addressing issues early, you can improve the reliability of your hydraulic system.
- Efficiency: Regular testing can help prevent unexpected downtime and reduce maintenance costs.
- Compliance: Adhering to industry standards and regulations requires regular testing and inspection of hydraulic hoses.
By implementing a comprehensive hydraulic hose testing program, you can significantly improve the safety, reliability, and efficiency of your hydraulic systems.
Hydraulic Hose Pressure Testing
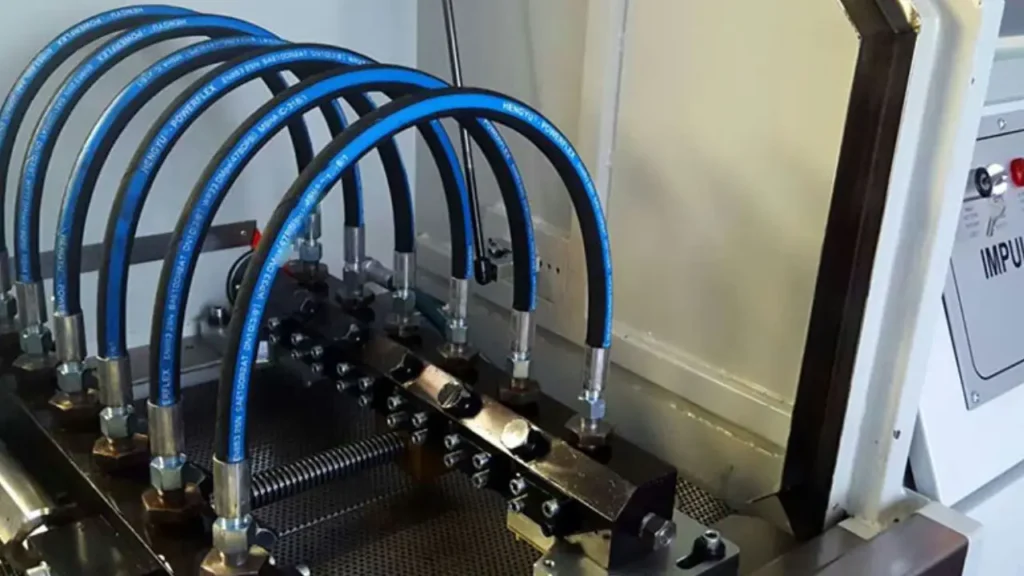
Hydraulic hose pressure testing is a critical procedure to ensure the integrity and safety of hydraulic systems. By subjecting hoses to controlled pressure, potential weaknesses and defects can be identified before they lead to catastrophic hydraulic hose failures.
Why is Pressure Testing Important?
- Early Detection of Faults: Pressure testing can reveal hidden flaws, such as cracks, leaks, or weakened areas, that may not be visible during a visual inspection.
- Verification of Pressure Rating: It ensures that the hose can withstand the maximum operating pressure of the hydraulic system.
- Preventive Maintenance: Regular pressure testing can help identify potential issues before they escalate into major problems.
Types of Pressure Testing:
- Hydrostatic Test: Involves filling the hose with a liquid, typically water, and applying pressure. This method can detect leaks and other defects.
- Pneumatic Test: Uses compressed air to pressurize the hose. This method is often used for hoses that will be filled with air or gas.
Factors to Consider During Pressure Testing:
- Pressure Rating: The test pressure should exceed the hose’s working pressure to identify potential weaknesses.
- Test Duration: The duration of the test should be sufficient to allow for thorough inspection.
- Environmental Factors: Temperature and humidity can affect the hose’s performance, so consider these factors when conducting the test.
Safety Precautions:
- Personal Protective Equipment (PPE): Wear appropriate PPE, including safety glasses, gloves, and protective clothing.
- Controlled Environment: Conduct the test in a controlled environment, away from potential hazards.
- Emergency Procedures: Have a plan in place to handle unexpected situations, such as a sudden hose failure.
By conducting regular pressure testing and following safety guidelines, you can significantly reduce the risk of hydraulic hose failures and ensure the safety and reliability of your hydraulic systems.
Hydraulic Hose Impulse Testing
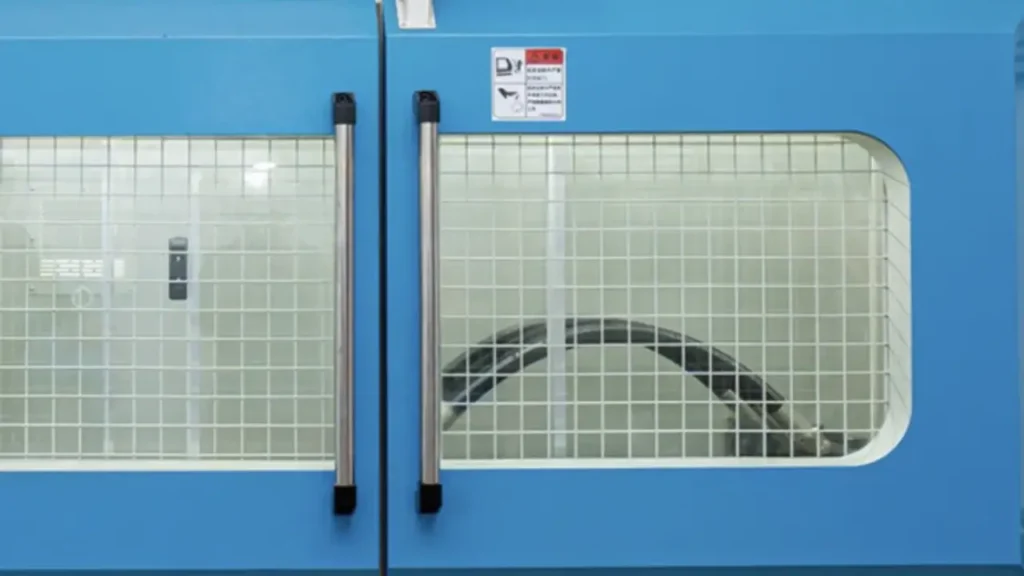
Hydraulic hose impulse testing is a rigorous process that evaluates the durability and reliability of hydraulic hoses under dynamic pressure conditions. It involves subjecting the hose to repeated cycles of pressure, simulating the real-world operating conditions of a hydraulic system.
Why is Impulse Testing Important?
- Predicts Service Life: Impulse testing helps determine the lifespan of a hydraulic hose by assessing its ability to withstand repeated pressure cycles.
- Identifies Weaknesses: It can reveal potential weaknesses in the hose’s construction, such as material fatigue or manufacturing defects.
- Ensures Safety: By identifying potential failure points, impulse testing helps prevent catastrophic failures that could lead to injuries or property damage.
- Optimizes Design: Manufacturers can use the results of impulse testing to improve hose design and material selection.
The Impulse Testing Process
- Test Setup: The hose is mounted on a testing machine and subjected to a specific pressure profile.
- Pressure Cycling: The hose is repeatedly pressurized and depressurized to simulate real-world operating conditions.
- Monitoring and Inspection: The hose is closely monitored for signs of damage, such as cracks, leaks, or bulges.
- Failure Analysis: If the hose fails during the test, a detailed analysis is conducted to determine the root cause of the failure.
By understanding the importance of hydraulic hose impulse testing and implementing rigorous testing procedures, manufacturers can ensure the reliability and safety of their products.
Hydraulic Hose Aging Testing
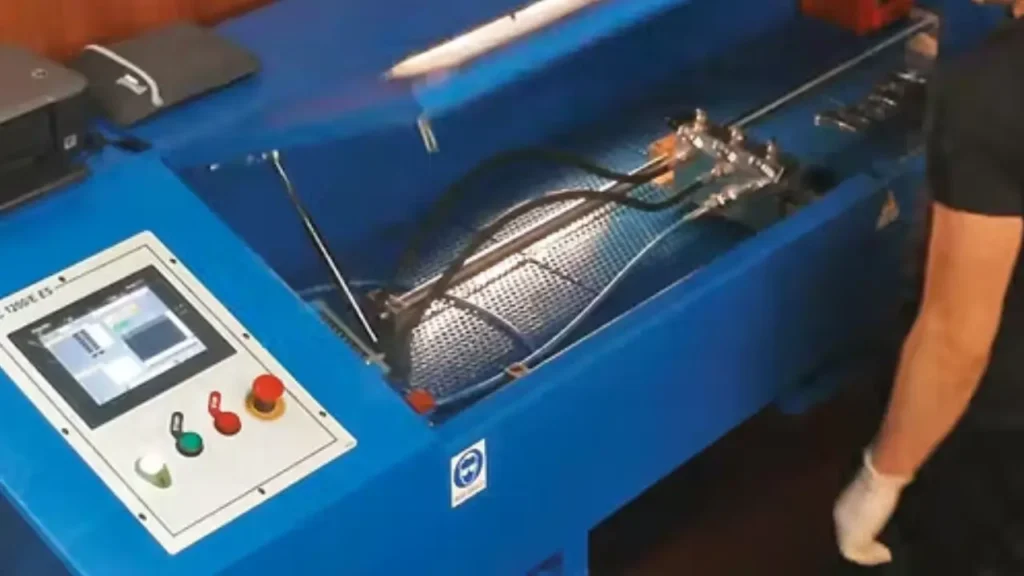
Hydraulic hose aging testing is a critical process to assess the long-term durability and performance of hydraulic hoses. By simulating accelerated aging conditions, manufacturers and users can evaluate the potential degradation of hose materials and identify potential failure points.
Common Aging Testing Methods
Heat Aging Test:
- Process: Exposing the hose to elevated temperatures for a specified period.
- Purpose: To simulate the effects of long-term exposure to high temperatures, which can lead to material degradation, cracking, and loss of flexibility.
Ozone Aging Test:
- Process: Exposing the hose to ozone gas, which can cause oxidative degradation of the rubber compounds.
- Purpose: To assess the hose’s resistance to ozone cracking, a common form of degradation in rubber products.
UV Aging Test:
- Process: Exposing the hose to ultraviolet radiation, simulating the effects of sunlight.
- Purpose: To evaluate the hose’s resistance to UV degradation, which can lead to color fading, cracking, and loss of mechanical properties.
Flex Fatigue Test:
- Process: Repeatedly flexing the hose to simulate real-world bending and flexing cycles.
- Purpose: To assess the hose’s resistance to fatigue failure, which can occur due to repeated flexing and bending.
Fluid Compatibility Test:
- Process: Immersing the hose in the specific fluid to be used in the application.
- Purpose: To evaluate the hose’s resistance to chemical attack and swelling.
By conducting these tests, manufacturers can ensure that their hydraulic hoses meet the required performance standards and are suitable for their intended applications. Additionally, users can assess the condition of their hoses and replace them before they reach the end of their service life, reducing the risk of catastrophic failures.
Hydraulic Hose Test Certificate
A hydraulic hose test certificate is a crucial document that verifies the integrity and performance of hydraulic hoses. It typically includes the following information:
Hose Specifications:
- Size (ID, OD)
- Material
- Pressure rating
- Temperature range
- Fluid compatibility
Test Parameters:
- Test pressure
- Test duration
- Test temperature
- Test method (hydrostatic or pneumatic)
Test Results:
- Whether the hydraulic hose passed or failed the test
- Any defects or anomalies observed during the test
Certification Authority: The name and accreditation of the organization that conducted the test
Test Date and Location: The date and location of the test
Signature and Stamp: The signature and stamp of the authorized personnel who conducted the test
Importance of Hydraulic Hose Test Certificates:
- Safety Assurance: Ensures that the hose is safe for use and can withstand the intended operating conditions.
- Compliance: Demonstrates compliance with industry standards and regulations.
- Quality Control: Verifies the quality and performance of the hose.
- Warranty Claims: Provides evidence for warranty claims in case of premature failure.
When to Request a Hydraulic Hose Test Certificate:
- New Hose Purchases: To verify the quality and performance of newly purchased hoses.
- Periodic Inspections: To assess the condition of hoses in service and identify potential issues.
- After Repairs: To confirm the integrity of repaired hoses.
- Insurance Requirements: Some insurance policies may require proof of hose testing.
By requesting and reviewing hydraulic hose test certificates, you can ensure the safety and reliability of your hydraulic systems.
Conclusion
Regular hydraulic hose testing is essential for maintaining the safety and reliability of your hydraulic systems. By following the guidelines outlined in this guide, you can identify potential issues early on and prevent costly breakdowns.
Ready to upgrade your hydraulic systems with high-quality hoses?
Contact us today to explore our wide range of hydraulic hoses and fittings. Our expert team can help you select the right products for your specific application and provide expert advice on installation and maintenance.