Hydraulic hose impulse testing is a critical procedure that simulates the real-world stresses a hose endures during operation. Certification and compliance with industry standards are paramount to ensure reliability and safety. This testing verifies the hose’s ability to withstand repeated pressure surges and flexes, preventing premature failure.
Adherence to standards like SAE J343 and ISO 6803 guarantees consistent quality and performance. Certified hoses undergo rigorous testing, proving their durability under extreme conditions. This blog explores the significance of certification and compliance in hydraulic hose impulse testing, highlighting their impact on system longevity and safety.
What Is Hydraulic Hose Impulse Testing
Hydraulic hose impulse testing is a critical process designed to evaluate the durability and reliability of hydraulic hoses under repeated pressure fluctuations. This type of hydraulic hose testing simulates the real-world conditions a hose experiences during operation, where it’s subjected to rapid and frequent pressure cycles. By replicating these dynamic stress conditions, manufacturers and engineers can assess the hose’s ability to withstand fatigue and potential failure over its intended lifespan.
The process involves subjecting the hose to a controlled number of pressure pulses, typically exceeding the hose’s rated working pressure. These pulses are applied at a specific frequency and temperature, mimicking the severe conditions found in heavy-duty hydraulic systems. The test aims to identify any weaknesses or defects in the hose’s construction, ensuring it meets industry standards and safety requirements.
Why is Impulse Testing Important for Hydraulic Hose
Impulse testing is crucial for hydraulic hoses because it directly assesses their ability to withstand the dynamic stresses encountered in real-world applications. Hydraulic systems often experience rapid pressure fluctuations, which can lead to fatigue and premature failure in hoses that aren’t adequately designed or manufactured. This testing ensures that hoses can reliably handle these stresses, preventing costly downtime, equipment damage, and, most importantly, potential safety hazards.
Here’s why impulse testing is so important:
- Ensures Safety: It verifies that hoses can handle pressure spikes, minimizing the risk of catastrophic failures and fluid leaks that could harm personnel.
- Predicts Lifespan: It provides valuable data on a hose’s expected service life, enabling informed maintenance schedules and preventing unexpected breakdowns.
- Validates Quality: It confirms that the hose meets industry standards and manufacturer specifications, guaranteeing consistent performance and reliability.
- Reduces Downtime: By identifying potential weaknesses early, it helps prevent costly equipment downtime and repairs.
- Optimizes System Performance: It ensures that hoses can maintain consistent fluid flow and pressure, contributing to overall system efficiency.
How to Do Hydraulic Hose Impulse Testing
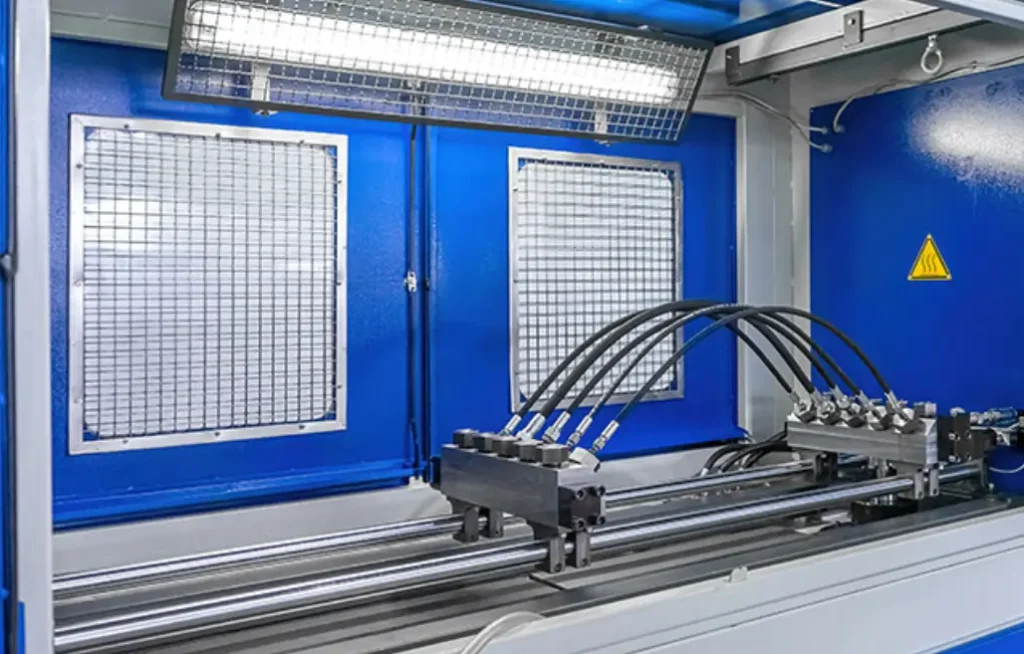
Hydraulic hose impulse testing is a rigorous procedure designed to simulate real-world operating conditions, ensuring hoses can withstand repeated pressure fluctuations. This process is essential for validating hose durability and reliability.
Here’s a detailed guide on how to conduct hydraulic hose impulse testing.
Tools Needed for Hydraulic Hose Impulse Testing:
- Hydraulic impulse test bench with pressure and flow control
- Pressure transducers and sensors
- Temperature sensors and control systems
- Data acquisition system and software
- High-pressure hydraulic fluid
- Assorted fittings and adapters
- Visual inspection tools (magnifying glass, etc.)
- Calibration equipment for sensors
- Safety equipment (eye protection, gloves, etc.)
Step 1: Preparing the Test Setup
The initial phase involves setting up the test environment. This includes selecting a suitable test bench, configuring the hydraulic system to generate the required pressure pulses, and ensuring all connections are secure. The test bench should be capable of handling the maximum pressure and flow rates specified for the hoses being tested. Precise calibration of pressure sensors and control systems is crucial for accurate data collection.
Additionally, the test setup must accommodate the temperature requirements specified by industry standards or application-specific needs. This often involves incorporating heating or cooling systems to maintain a consistent temperature throughout the test. Proper ventilation and safety measures are also critical to mitigate risks associated with high-pressure hydraulic systems.
Ensuring the test setup is properly calibrated and secure is paramount to obtaining reliable results. Any error in the test setup could lead to inaccurate measurements, which in turn could lead to selecting the incorrect hose for an application.
Step 2: Conducting the Impulse Test
Once the setup is prepared, the impulse test can commence. This involves subjecting the hydraulic hose to a series of pressure pulses, typically exceeding the hose’s rated working pressure. The frequency, amplitude, and waveform of these pulses are carefully controlled to replicate the dynamic stresses experienced in actual hydraulic systems. Data loggers record pressure and temperature throughout the test, allowing for detailed analysis of the hose’s performance.
The test continues for a predetermined number of cycles or until the hose fails. Visual inspection is conducted periodically to check for signs of damage, such as leaks, cracks, or deformation. Any failures are documented, including the location and mode of failure. Post-test analysis involves evaluating the hose’s performance against industry standards and manufacturer specifications.
Proper control of the system and recording of data is required for a complete test. Any variation in the test parameters can cause inaccurate data.
Step 3: Analyzing and Reporting Test Results
The final step involves analyzing the collected data and generating a comprehensive test report. This report includes details about the test setup, parameters, and results. It documents any failures observed, along with their causes and implications. The analysis focuses on evaluating the hose’s ability to withstand the specified impulse conditions and comparing its performance to industry standards like SAE J343.
The report also provides recommendations for hose selection, maintenance, and replacement based on the test results. This information is crucial for ensuring the reliability and safety of hydraulic systems. It helps manufacturers improve hose design and quality, and it assists users in selecting the right hoses for their applications.
A complete and accurate test report is essential to understanding the quality of the hose, and to making informed decisions about the use of the hose.
How Long Do Hydraulic Hose Impulse Testing Last
The duration of hydraulic hose impulse testing varies significantly depending on the specific industry standards, application requirements, and the hydraulic hose’s intended lifespan. Tests can range from a few hours to several weeks. Factors influencing the test duration include the number of impulse cycles required, the frequency of those cycles, and the operating temperature. Some tests might demand millions of cycles, simulating years of real-world use, while others may focus on a shorter, more intense stress period.
Typically, standards like SAE J343 specify the number of impulse cycles a hose must withstand to pass certification. These standards are designed to replicate the stresses a hose would experience throughout its operational life. Modern testing equipment allows for automated cycling and data collection, which can run continuously. The actual length of time is not the most important aspect, but the number of cycles that are conducted on the hose, and if the hose passes those cycles.
Hydraulic Hose Impulse Testing Certificate
A Hydraulic Hose Impulse Testing Certificate is a document that verifies a hydraulic hose has undergone and passed rigorous impulse testing according to industry standards. This hydraulic hose impulse testing certificate provides evidence that the hose meets specific performance criteria and is suitable for its intended application.
Purpose:
- To demonstrate that a hydraulic hose can withstand repeated pressure fluctuations and maintain its integrity over a specified number of impulse cycles.
- To ensure compliance with industry standards, such as SAE J343 or ISO 6803.
- To provide assurance of the hose’s quality and reliability.
Content:
- Manufacturer’s information (name, address, etc.)
- Hose specifications (size, material, pressure rating, etc.)
- Testing parameters (pressure amplitude, frequency, temperature, number of cycles)
- Test results (pass/fail, any observed failures, etc.)
- Date of testing and certificate issuance
- Reference to the applicable industry standard
- Test lab information.
- Certification of the lab.
Importance:
- Safety: Certifies that the hose can handle the demanding conditions of hydraulic systems, minimizing the risk of failures and leaks.
- Quality assurance: Provides evidence of the hose’s quality and performance.
- Compliance: Ensures that the hose meets industry standards and regulatory requirements.
- Reliability: Gives users confidence in the hose’s ability to perform reliably over its intended lifespan.
In essence, a Hydraulic Hose Impulse Testing Certificate serves as a testament to the hose’s ability to perform under dynamic pressure conditions, ensuring safety and reliability in hydraulic applications.
Conclusion
In conclusion, hydraulic hose impulse testing, particularly for certification and compliance, is paramount for ensuring system safety and longevity. Rigorous testing validates hose performance under demanding conditions, preventing catastrophic failures and minimizing downtime. Adherence to industry standards like SAE J343 guarantees consistent quality and reliability, safeguarding both equipment and personnel.
Compliance with certification requirements not only mitigates risks but also enhances operational efficiency. By selecting certified hoses, businesses can optimize system performance and reduce maintenance costs associated with premature hose failures. This proactive approach underscores the importance of prioritizing quality and compliance in hydraulic system design and maintenance.
For reliable, hydraulic hoses that meet stringent industry standards, consider Gushan Rubber. We offer a comprehensive range of certified hydraulic hoses, including those designed for demanding impulse applications. Contact us today to explore our wholesale options and ensure your hydraulic systems operate with maximum safety and efficiency.