Industrial hoses are one of the unsung heroes of countless industries. Far from being simple tubes, these rugged, versatile conduits are designed to move a wide range of materials under demanding conditions—from liquids and gases to slurries and powders.
Understanding the various types of industrial hoses is essential to making informed decisions, ensuring seamless operations, and avoiding costly failures. In this guide, we’ll walk you through the various types of industrial hoses, their unique characteristics, and their important applications across different industries.
The Importance of Understanding Industrial Hose Types
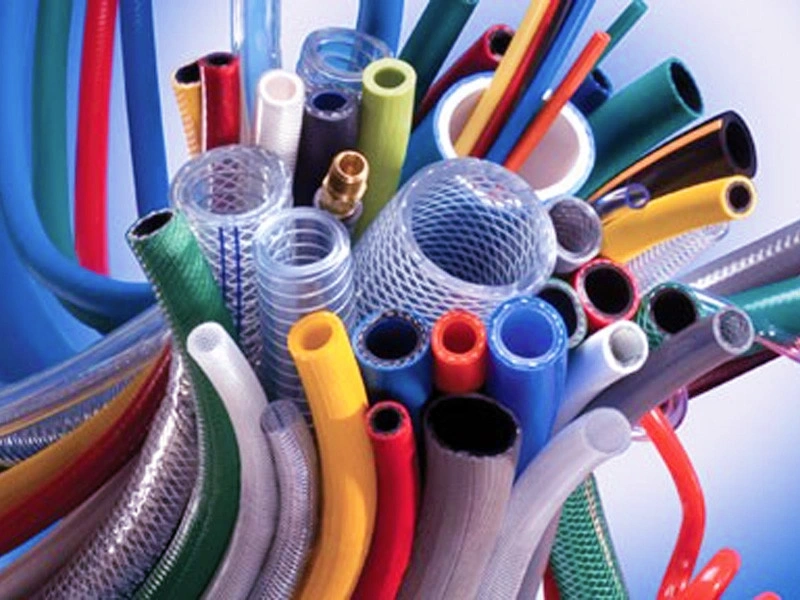
Before we dive into the specifics of each category, let’s consider why a thorough grasp of types of industrial hoses is so critical. It’s not merely about knowing what carries what; it’s about optimizing performance, ensuring regulatory compliance, and most importantly, guaranteeing safety. Using the wrong hose can lead to catastrophic failures, environmental damage, and severe injuries. Conversely, choosing the perfectly matched hose enhances efficiency, extends equipment life, and minimizes downtime. It’s a foundational knowledge point for anyone responsible for procurement, maintenance, or operations in an industrial setting.
Common Types of Industrial Hoses
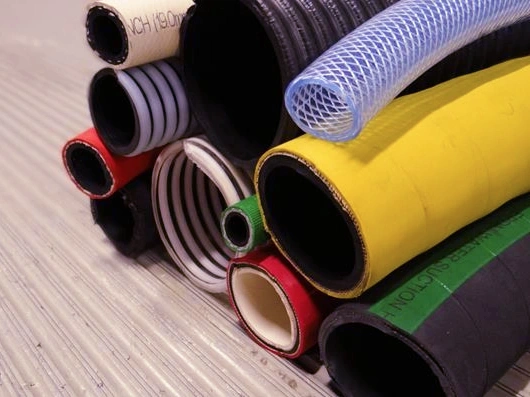
In my experience, industrial hoses can be broadly categorized based on the material they convey and the conditions they operate under. While there’s a vast spectrum of specialized hoses, understanding the main types will cover most industrial needs. Let’s explore some of the most common and essential types of industrial hoses you’ll encounter.
Air Hoses: Powering Pneumatic Systems
When it comes to powering pneumatic tools or delivering compressed air for various processes, air hoses are indispensable. These hoses are specifically designed to withstand the internal pressure of compressed air while remaining flexible enough for practical use in workshops, construction sites, and manufacturing plants. Their robust construction ensures durability against abrasion and impacts, common in demanding work environments.
Air hoses are vital in workshops for operating impact wrenches, nail guns, and paint sprayers. In construction, they power jackhammers and concrete vibrators, while in manufacturing, they’re essential for automation and assembly lines. Proper selection is crucial to match the hose’s pressure rating with the pneumatic system’s requirements, preventing bursts and ensuring consistent airflow for optimal tool performance and worker safety.
Water Hoses: The Lifeline of Many Operations
Water is fundamental to almost every industry, whether for cooling, cleaning, irrigation, or fire suppression. Water hoses are designed to handle various water pressures and temperatures, from potable water supply to high-pressure washdowns. Their construction prioritizes flexibility, durability, and resistance to kinking, making them versatile for numerous applications.
From agricultural irrigation systems to industrial cleaning processes and emergency fire fighting, water hoses are omnipresent. They are crucial in construction for dust suppression and concrete mixing, and in food processing for sanitation. The specific type of water hose selected depends on factors like pressure, temperature, and whether it needs to be potable water compliant, ensuring efficient and safe water transport across diverse industrial needs.
Steam Hoses: Handling High Temperatures with Care
Working with steam requires specialized equipment due to its high temperature and pressure. Steam hoses are engineered with multiple layers of heat-resistant materials, typically synthetic rubber or steel wire reinforcement, to safely convey saturated or superheated steam without degradation. Their design prioritizes extreme temperature resistance and pressure containment.
Steam hoses are critical in processes like sterilization in food and pharmaceutical industries, heating systems, and even some cleaning applications. Due to the inherent dangers of high-temperature steam, the integrity of these hoses is paramount. Regular inspection and adherence to manufacturer guidelines for pressure and temperature limits are essential to prevent catastrophic failures and ensure worker safety in steam-intensive environments.
Oil and Fuel Hoses: Transporting Hydrocarbons Safely
The safe transfer of petroleum products, including gasoline, diesel, lubricants, and hydraulic fluids, relies heavily on oil and fuel hoses. These hoses are specifically constructed with linings resistant to hydrocarbon degradation, preventing permeation and ensuring chemical compatibility. Their robust outer covers also provide excellent abrasion and weather resistance.
These hoses are vital in fuel transfer stations, automotive workshops, and hydraulic systems in heavy machinery. They are engineered to handle various grades of oil and gas, ensuring leak-free and efficient transfer. Compliance with industry standards and regulations is crucial for these hoses, as failure can lead to environmental contamination, fire hazards, and significant operational downtime, emphasizing the need for their specialized design.
Chemical Hoses: Precision for Corrosive Substances
Transporting acids, alkalis, solvents, and other corrosive chemicals demands highly specialized chemical hoses. These hoses are designed with inner linings made from inert materials, such as Teflon (PTFE) or specific synthetic rubbers, to resist chemical attack and prevent contamination of the transported media. The outer cover also often provides resistance to external chemical spills.
Chemical hoses are indispensable in the chemical manufacturing, pharmaceutical, and food processing industries, where the safe transfer of various reagents is critical. The selection process for these hoses is highly meticulous, requiring precise matching of the hose material to the specific chemicals being handled to prevent degradation, ensure product purity, and, most importantly, protect personnel from hazardous exposures.
Material Handling Hoses: Moving Solids and Abrasives
When it comes to conveying solid materials like grains, powders, pellets, or even abrasive slurries, material handling hoses are the workhorses. These hoses are constructed with thick, abrasion-resistant inner tubes, often reinforced with wire helices, to withstand the constant wear and tear from friction and impact.
They are extensively used in agriculture for grain transfer, in construction for concrete and abrasive aggregate conveyance, and in manufacturing for moving plastic pellets or powders. The robust construction ensures longevity despite constant abrasive contact.
Selecting the right material handling hose depends on the size, density, and abrasiveness of the material being transported, ensuring efficient and damage-free transfer.
What is the Difference Between Hydraulic Hose and Industrial Hose?
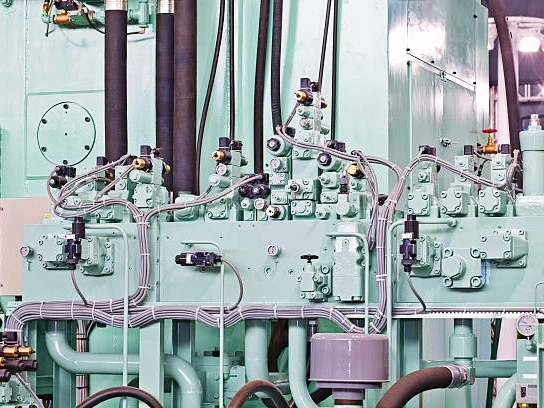
The main difference between a hydraulic hose and a general industrial hose lies in their intended application and, consequently, their construction and pressure capabilities.
Hydraulic hoses are specifically engineered to handle extremely high pressures and rapid pressure impulses, typically for conveying hydraulic fluids in heavy machinery like excavators, forklifts, and industrial presses. They feature multiple layers of reinforcement, often braided or spiral-wound steel wire, to withstand these intense forces, ensuring power transmission in hydraulic systems.
Industrial hoses, while also designed for various demanding tasks, generally handle a broader range of media at more moderate pressures. They transport substances like air, water, chemicals, steam, or abrasive materials in applications such as manufacturing plants, agriculture, and general utility. Their construction varies widely depending on the specific media and environment, focusing on properties like chemical resistance, abrasion resistance, and flexibility rather than solely extreme pressure.
Key Considerations When Choosing Industrial Hoses
Beyond the specific types of industrial hoses, several critical factors influence the selection process. I always consider these elements to ensure the hose performs optimally and safely in its intended application.
1. Material Compatibility
This is arguably the most crucial factor. The hose’s inner tube material must be compatible with the substance it will carry to prevent degradation, contamination, or failure. For example, a standard rubber hose won’t suffice for strong acids.
2. Pressure Rating
Every hose has a maximum working pressure (MWP) and a burst pressure. It’s essential to select a hose with a MWP that exceeds the maximum system pressure to ensure a safety margin. Never exceed the rated pressure.
3. Temperature Range
Hoses must be able to withstand both the internal temperature of the conveyed media and the external ambient temperature. Extreme temperatures can degrade hose materials, leading to failure.
4. Application Environment
Consider the external conditions: Is it exposed to abrasion, ozone, UV light, chemicals, or extreme weather? The hose’s cover material needs to resist these environmental factors.
5. Size and Length
The inner diameter (ID) must be appropriate for the flow rate required, and the outer diameter (OD) for fitting compatibility. The length should be sufficient to prevent kinking or excessive tension.
6. Reinforcement
Hoses are reinforced with various materials like textile braids, spiral steel wire, or synthetic yarns to handle pressure and maintain shape. The type of reinforcement depends on the pressure rating and flexibility requirements.
7. End Fittings
The type of coupling or fitting (e.g., camlock, threaded, flanged) must match the equipment and ensure a secure, leak-proof connection. Material compatibility of fittings is also crucial.
A Quick Reference Table for Industrial Hoses
To make it easier to compare some of the types of industrial hoses, I’ve put together this quick reference table summarizing their common uses and key features.
Hose Type | Common Applications | Key Characteristics |
Air Hoses | Pneumatic tools, air lines, manufacturing automation | Withstands compressed air pressure, flexible, abrasion-resistant outer cover |
Water Hoses | Water supply, irrigation, washdown, fire suppression | Handles various water pressures/temps, kink-resistant, flexible |
Steam Hoses | Sterilization, heating systems, process heating | High-temperature and pressure resistance, multi-layered, heat-resistant lining |
Oil & Fuel Hoses | Fuel transfer, hydraulic systems, lubricants | Hydrocarbon-resistant lining, robust outer cover, anti-static properties |
Chemical Hoses | Pneumatic tools, air lines, and manufacturing automation | Inert lining (e.g., PTFE), chemical-resistant cover, highly specific compatibility |
Material Handling | Abrasive slurries, grains, powders, pellets, aggregates | Thick, abrasion-resistant inner tube, often reinforced for vacuum/pressure |
Conclusion
With a clear understanding of your specific application and key factors, you can make your selection with confidence. Always prioritize safety, material compatibility, and compliance with industry standards. Whether you are conveying air, water, chemicals, or abrasive solids, there is always a well-designed hose to meet your needs.
Contact us for more information!