When it comes to cutting-edge fluid transfer, thermoplastic hydraulic hoses are the undisputed leaders. They represent a modern, high-performance solution that steadily outperforms traditional solutions due to their unique properties and wide range of applications.
This comprehensive guide from our factory provides an in-depth look at why these hoses are indispensable, highlighting their unique benefits and outlining the areas where they truly deliver exceptional value.
What Is Thermoplastic Hydraulic Hose?
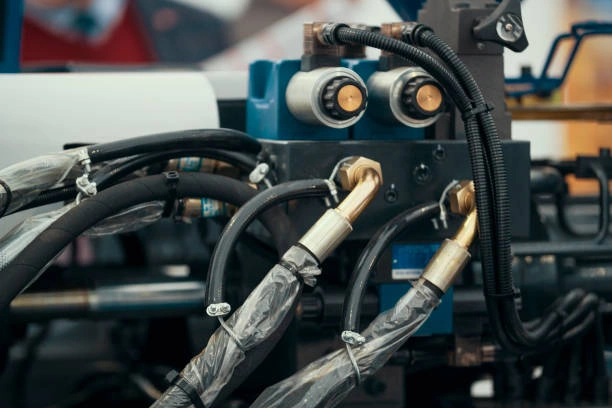
Understanding the construction of a thermoplastic hydraulic hose helps us appreciate its performance capabilities. Each layer plays a crucial role in the hose’s overall integrity and function. It’s this clever layering that allows them to withstand high pressures, extreme temperatures, and corrosive fluids, making them a reliable choice for critical applications. Let’s break down the typical components.
- Inner Tube/Liner: This is the innermost layer that comes into direct contact with the hydraulic fluid. It’s typically made from a smooth, low-friction thermoplastic material like nylon or polyester, chosen for its chemical compatibility with various hydraulic fluids and its ability to minimize pressure drop. The liner ensures fluid integrity and prevents contamination.
- Reinforcement Layer(s): This layer is critical for the hose’s pressure-handling capabilities. It consists of high-tensile synthetic fibers, such as polyester or aramid, braided or spiraled around the inner tube. Unlike steel wire in some traditional hoses, these synthetic reinforcements offer excellent flexibility and fatigue resistance, contributing to the hose’s lighter weight. Multiple layers can be used for higher pressure ratings.
- Outer Cover: The outermost layer protects against abrasion, ozone, UV radiation, and environmental damage. Materials like polyurethane or polyester are commonly used for their durability and resistance to harsh outdoor conditions. This cover also often dictates the hose’s color and texture.
What Is Thermoplastic Hydraulic Hose Made of?
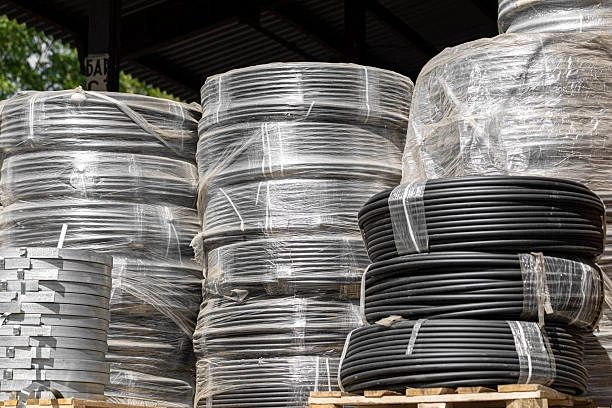
When we talk about what thermoplastic hydraulic hoses are made of, we’re discussing a sophisticated, multi-layered construction designed for high performance. At its core, these hoses utilize thermoplastic polymers like nylon (polyamide), polyester, or even fluoropolymers for the inner tube.
This choice of material is crucial because it offers excellent chemical compatibility with various hydraulic fluids, minimizes friction for efficient flow, and prevents material degradation from the fluid itself.
Beyond the inner tube, thermoplastic hydraulic hoses incorporate a reinforcement layer, typically made from high-tensile synthetic fibers such as polyester or aramid. These fibers are precisely braided or spiraled to provide the necessary burst strength and pressure rating while keeping the hose lightweight and highly flexible.
An outer cover, usually made from durable polyurethane or specialized polyester, protects the internal components from external threats like abrasion, UV radiation, ozone, and environmental damage, ensuring the hose’s longevity in challenging industrial settings.
Key Advantages of Choosing Thermoplastic Hydraulic Hoses
Having worked with various hydraulic systems, I’ve come to appreciate the significant advantages that thermoplastic hydraulic hoses offer over their traditional counterparts. Their unique material properties translate directly into tangible benefits for performance, longevity, and operational efficiency. These advantages often lead to lower maintenance costs and increased uptime, making them a smart investment for many industries.
Feature | Thermoplastic Hydraulic Hoses | Traditional Rubber Hoses |
Weight | Significantly lighter, reducing equipment weight and improving handling. | Heavier due to steel wire reinforcement, impacting maneuverability. |
Flexibility | Excellent flexibility, even at low temperatures, allowing tighter bend radii. | Can be stiffer, especially in cold conditions, requiring larger bend radii. |
Abrasion Resistance | Superior abrasion and cut resistance, extending service life in harsh environments. | Generally less resistant to abrasion and cuts, prone to external damage. |
Chemical Resistance | Broad chemical compatibility, including many aggressive fluids and solvents. | More limited chemical resistance, susceptible to degradation by certain fluids. |
Ozone/UV Resistance | Inherently resistant to ozone and UV degradation, ideal for outdoor applications. | Can be susceptible to ozone cracking and UV damage over time, requiring protective covers. |
Moisture Absorption | Very low moisture absorption, preventing swelling and maintaining performance. | Can absorb moisture, potentially leading to material degradation over time. |
Electrical Non-Conductivity | Many designs offer non-conductive properties, enhancing safety in certain applications. | Typically conductive unless specifically designed otherwise. |
Cleanliness | Smooth inner bore reduces fluid contamination and promotes efficient flow. | Can have rougher inner surfaces, potentially leading to particle shedding. |
Thermoplastic Hydraulic Hose Applications
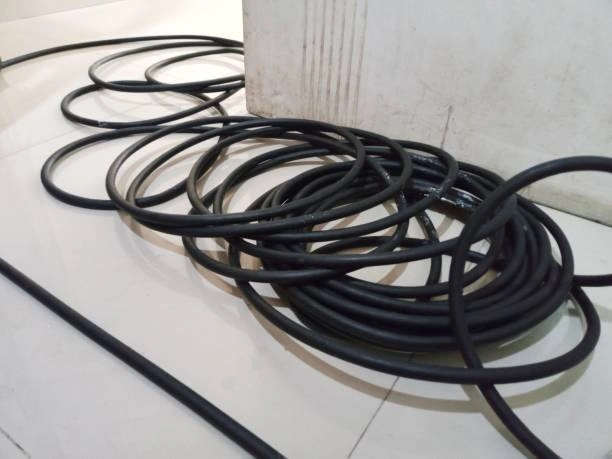
The versatility and robust performance of thermoplastic hydraulic hoses make them ideal for a wide array of applications where traditional hoses might fall short. From heavy machinery to sensitive electronic equipment, their unique properties provide reliable and efficient fluid transfer. We often see them deployed in situations demanding precision, cleanliness, or resistance to challenging environmental factors.
Offshore and Marine: Resistance to saltwater corrosion, UV exposure, and wide temperature swings makes them suitable for marine and offshore drilling applications.
Construction and Mobile Equipment: Their lightweight nature and excellent flexibility make them perfect for dynamic applications like forklifts, excavators, and agricultural machinery where hoses are constantly flexing and exposed to harsh conditions. The abrasion resistance is particularly beneficial here.
Aerial Work Platforms (AWPs): For boom lifts and scissor lifts, thermoplastic hydraulic hoses offer significant weight savings, contributing to better stability and extended reach. Their non-conductive properties are also a major safety advantage when working near power lines.
Automotive and Transportation: In vehicle braking systems, power steering, and fuel lines, these hoses provide reliable performance, especially in compact spaces where tight bends are required. Their resistance to various automotive fluids is also a key factor.
Industrial Robotics: Precision and minimal footprint are critical in robotics. The flexibility and smaller outer diameter of thermoplastic hydraulic hoses allow for cleaner routing and greater movement within robotic arms and automated systems.
Material Handling Equipment: From conveyers to lifting mechanisms, these hoses offer durability and resistance to wear and tear, ensuring smooth and uninterrupted operation in demanding material handling environments.
High-Pressure Washing and Cleaning: Their ability to withstand high pressures and resistance to water absorption makes them an excellent choice for pressure washing equipment and industrial cleaning systems.
Specialty Applications: This includes applications requiring specific properties like non-conductivity (e.g., utility vehicles, power tools), resistance to specific chemicals (e.g., paint spray, chemical transfer), or very tight bend radii (e.g., medical devices, test equipment).
The Benefits of Thermoplastic Hydraulic Hose
While thermoplastic hydraulic hoses offer numerous benefits, selecting the right one requires careful consideration. Just like any engineered product, their performance depends on a proper match between the hose’s specifications and the application’s requirements. Over the years, I’ve learned that overlooking these details can lead to premature failure and costly downtime.
- Pressure Rating: This is paramount. Ensure the hose’s maximum working pressure exceeds the system’s maximum operating pressure, including surge pressures. Always consider a safety factor.
- Temperature Range: Hydraulic systems can operate in a wide range of temperatures. Verify that the hose’s specified operating temperature range covers both the ambient temperature and the fluid temperature. Extreme temperatures can degrade hose material and fittings.
- Fluid Compatibility: The inner tube material must be compatible with the hydraulic fluid being used. Incompatible fluids can cause the liner to swell, crack, or dissolve, leading to leaks and system failure. Always consult compatibility charts.
- Bend Radius: While thermoplastic hoses are flexible, they still have a minimum bend radius. Exceeding this can kink the hose, restrict flow, and cause premature failure. Always allow for sufficient space for proper routing.
- Abrasion and Environmental Resistance: Consider the external environment. If the hose will be exposed to significant abrasion, harsh chemicals, UV light, or extreme weather, choose a cover material specifically designed to withstand these conditions.
- Electrical Conductivity Requirements: For applications where electrical non-conductivity is critical (e.g., near power lines), ensure the hose is specifically rated as non-conductive.
- Fittings and Assembly: The proper selection and installation of fittings are just as important as the hose itself. Ensure that the fittings are compatible with the hose type and designed for the application’s pressure and temperature. Improper assembly is a leading cause of hose failure.
- Length and Routing: Accurate length measurement and proper routing prevent kinking, abrasion, and unnecessary stress on the hose. Avoid twisting the hose during installation.
Maintenance and Best Practices for Longevity
Even the most robust thermoplastic hydraulic hose requires proper maintenance and adherence to best practices to ensure its longevity and reliable performance.
- Regular Visual Inspection: Periodically inspect hoses for signs of wear, cuts, abrasions, kinks, bulges, leaks, or cracked outer covers. Pay close attention to areas near fittings.
- Cleanliness: Keep hoses free from dirt, debris, and chemical spills. Contaminants on the exterior can degrade the cover, while internal contamination can damage the hydraulic system.
- Proper Routing: Ensure hoses are routed correctly, avoiding sharp bends, twists, and contact with moving parts or sharp edges. Use clamps or protective sleeves where necessary.
- Pressure Checks: Monitor system pressure to ensure it remains within the hose’s specified working pressure. Over-pressurization is a common cause of hose failure.
- Temperature Monitoring: Ensure that operating temperatures, both ambient and fluid, remain within the hose’s rated temperature range.
- Fluid Quality: Maintain clean hydraulic fluid and adhere to recommended fluid change intervals. Contaminated fluid can degrade the hose’s inner tube and lead to system issues.
- Replacement Schedules: Even without visible damage, hoses have a finite service life. Follow manufacturer recommendations for replacement intervals, especially in critical applications.
- Proper Storage: Store spare hoses in a cool, dry, dark place, away from ozone-generating equipment, direct sunlight, and extreme temperatures to prevent premature aging.
Conclusion
Thermoplastic hydraulic hoses are more than just a replacement; they are a superior choice for many modern hydraulic applications. Their inherent advantages in weight, flexibility, abrasion resistance and chemical compatibility translate into significant operational benefits, resulting in increased efficiency, enhanced safety, and reduced downtime.
Which applications in your industry do you think could benefit most from these advanced hoses? Gushan provides the most extensive selection of crimp and swage couplings to complete your hydraulic hose system. If you have questions about the thermoplastic hydraulic hose, please feel free to contact us at any time.