Hydraulic hoses are critical components in many industrial and commercial applications, powering everything from heavy machinery to automotive systems.
Over time, these hoses are subjected to various stresses, including pressure, temperature extremes, and physical damage. As a result, they can deteriorate, leading to potential leaks, failures, and safety hazards. To mitigate these risks, regular hydraulic hose inspection is essential.
This blog post will delve into identifying wear and tear in hydraulic hoses. We will explore common signs of deterioration, discuss effective inspection techniques, and provide guidance on timely replacement. By understanding these factors, you can ensure the safety and reliability of your hydraulic systems.
Why Hydraulic Hose Inspection is Important
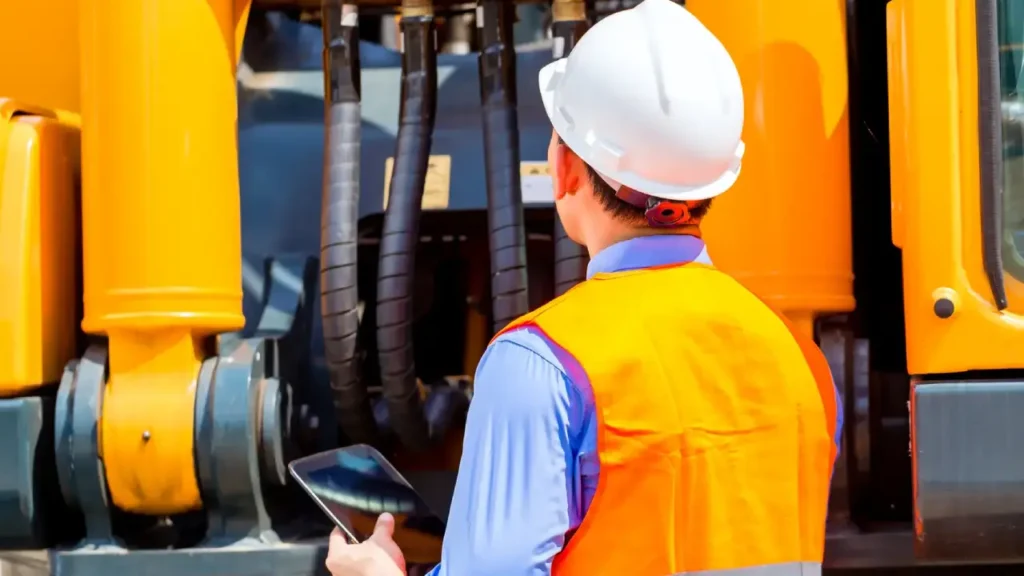
Hydraulic hoses are the lifeblood of many industrial and commercial operations. They are subjected to constant pressure, temperature fluctuations, and exposure to harsh environments. As a result, they are prone to wear and tear, which can lead to serious consequences, including:
- Equipment Failure: A ruptured hose can cause sudden and catastrophic equipment failure, leading to production downtime and financial loss.
- Safety Hazards: Leaking hydraulic fluid can create slippery surfaces, posing a significant safety risk to workers. Additionally, hydraulic fluid can damage equipment and the environment.
- Increased Operational Costs: Frequent hose replacements and unplanned downtime can significantly increase operational costs.
Regular hydraulic hose inspection is essential to prevent these issues. By identifying potential problems early on, you can take proactive measures to avoid costly repairs and downtime.
Key areas to inspect during a hydraulic hose inspection include:
- Visual Inspection: Check for cuts, cracks, abrasions, and signs of excessive wear.
- Pressure Testing: Verify that the hose can withstand the required operating pressure.
- Flex Testing: Assess the hose’s flexibility and resistance to fatigue.
- Coupling Inspection: Examine the couplings for damage, corrosion, and proper tightening.
By incorporating regular hydraulic hose inspections into your maintenance routine, you can significantly improve the reliability and safety of your hydraulic systems.
Hydraulic Hose Inspection Checklist
Visual Inspection:
- Hose Surface:
- Check for cuts, cracks, abrasions, or other signs of damage.
- Look for evidence of heat damage, such as discoloration or blistering.
- Inspect for any signs of chemical exposure, such as swelling or softening.
- Hose Fittings:
- Verify that all fittings are securely tightened.
- Check for leaks at the connections.
- Inspect for corrosion or damage to the fittings.
- Hose Clamps:
- Ensure that clamps are secure and not damaged.
- Verify that clamps are properly positioned.
- Hose Routing:
- Check for any sharp bends or kinks in the hose.
- Ensure that the hose is routed away from heat sources and sharp edges.
- Verify that the hose is not excessively stretched or compressed.
Functional Inspection:
- Pressure Testing:
- Use a pressure gauge to verify that the hose can withstand the required operating pressure.
- Check for any leaks during pressure testing.
- Flex Testing:
- Bend the hose to assess its flexibility and resistance to fatigue.
- Look for any signs of cracking or weakening in the hose.
Additional Considerations:
- Hose Age:
- Consider the age of the hose and its expected lifespan.
- Replace hoses that have exceeded their recommended service life.
- Operating Environment:
- Take into account the harshness of the operating environment, such as exposure to extreme temperatures, chemicals, or vibration.
- Maintenance Records:
- Keep detailed records of all inspections and maintenance performed on hydraulic hoses.
Remember:
- Regular Inspections: Conduct regular inspections, ideally on a monthly or quarterly basis.
- Trained Personnel: Ensure that inspections are performed by trained and qualified personnel.
- Corrective Action: Take immediate corrective action for any identified issues.
- Replacement: Replace damaged or worn hoses promptly to prevent further damage and downtime.
By following this checklist and conducting regular inspections, you can help ensure the safety and reliability of your hydraulic systems.
Hydraulic Hose Inspection Procedure
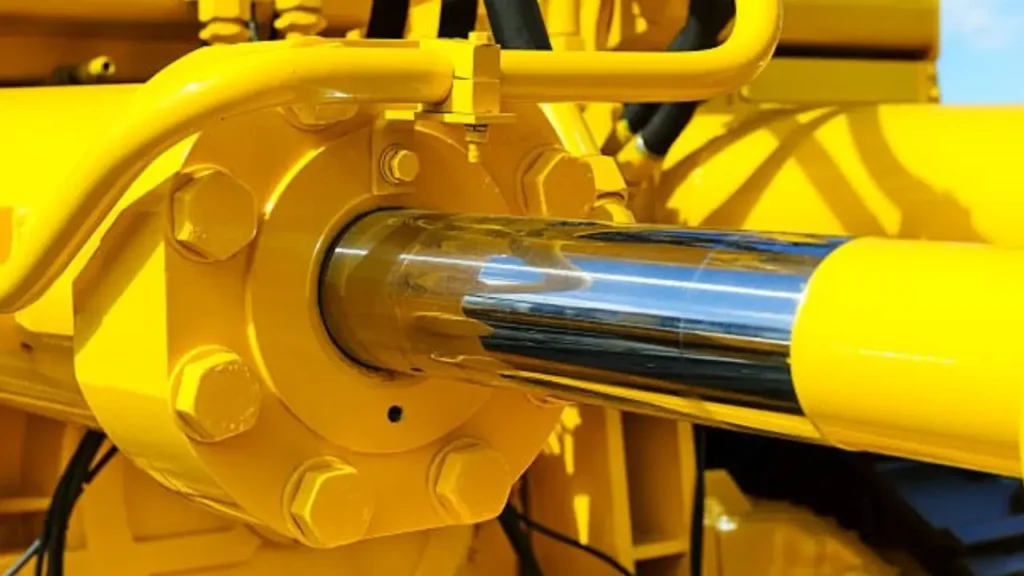
1. Visual Inspection:
Hose Surface:
- Check for cuts, cracks, abrasions, or other signs of physical damage.
- Look for evidence of heat damage, such as discoloration or blistering.
- Inspect for any signs of chemical exposure, such as swelling or softening.
Hose Fittings:
- Verify that all fittings are securely tightened.
- Check for leaks at the connections.
- Inspect for corrosion or damage to the fittings.
Hose Clamps:
- Ensure that clamps are secure and not damaged.
- Verify that clamps are properly positioned.
- Check for any sharp bends or kinks in the hose.
- Ensure that the hose is routed away from heat sources and sharp edges.
- Verify that the hose is not excessively stretched or compressed.
2. Functional Inspection:
Pressure Testing:
- Use a pressure gauge to verify that the hose can withstand the required operating pressure.
- Check for any leaks during pressure testing.
Flex Testing:
- Bend the hose to assess its flexibility and resistance to fatigue.
- Look for any signs of cracking or weakening in the hose.
Additional Considerations:
Hose Age:
Consider the age of the hose and its expected lifespan.
Replace hoses that have exceeded their recommended service life.
Operating Environment:
Take into account the harshness of the operating environment, such as exposure to extreme temperatures, chemicals, or vibration.
Maintenance Records:
Keep detailed records of all inspections and maintenance performed on hydraulic hoses.
Frequency of Inspection:
The frequency of inspection depends on several factors, including:
- Operating Environment: Harsh environments may require more frequent inspections.
- Hose Age: Older hoses may need more frequent checks.
- Usage: Heavy-duty applications may necessitate more frequent inspections.
General guidelines:
- Monthly Inspections: For most applications, monthly visual inspections are recommended.
- Annual Inspections: Annual pressure testing and flex testing are typically sufficient.
Remember:
- Trained Personnel: Ensure that inspections are performed by trained and qualified personnel.
- Corrective Action: Take immediate corrective action for any identified issues.
- Replacement: Replace damaged or worn hoses promptly to prevent further damage and downtime.
By following this procedure and conducting regular inspections, you can help ensure the safety and reliability of your hydraulic systems.
Hydraulic Hose Inspection Criteria
Hydraulic hose inspections are essential to ensure the safety and reliability of hydraulic systems. Here are the key criteria to consider during an inspection:
Visual Inspection
- Hose Surface:
- Check for cuts, cracks, abrasions, or other signs of physical damage.
- Look for evidence of heat damage, such as discoloration or blistering.
- Inspect for any signs of chemical exposure, such as swelling or softening.
- Hose Fittings:
- Verify that all fittings are securely tightened.
- Check for leaks at the connections.
- Inspect for corrosion or damage to the fittings.
- Hose Clamps:
- Ensure that clamps are secure and not damaged.
- Verify that clamps are properly positioned.
- Hose Routing:
- Check for any sharp bends or kinks in the hose.
- Ensure that the hose is routed away from heat sources and sharp edges.
- Verify that the hose is not excessively stretched or compressed.
Functional Inspection
- Pressure Testing:
- Use a pressure gauge to verify that the hose can withstand the required operating pressure.
- Check for any leaks during pressure testing.
- Flex Testing:
- Bend the hose to assess its flexibility and resistance to fatigue.
- Look for any signs of cracking or weakening in the hose.
Additional Considerations
- Hose Age:
- Consider the age of the hose and its expected lifespan.
- Replace hoses that have exceeded their recommended service life.
- Operating Environment:
- Take into account the harshness of the operating environment, such as exposure to extreme temperatures, chemicals, or vibration.
- Maintenance Records:
- Keep detailed records of all inspections and maintenance performed on hydraulic hoses.
Remember:
- Regular Inspections: Conduct regular inspections, ideally on a monthly or quarterly basis.
- Trained Personnel: Ensure that inspections are performed by trained and qualified personnel.
- Corrective Action: Take immediate corrective action for any identified issues.
- Replacement: Replace damaged or worn hoses promptly to prevent further damage and downtime.
By following these criteria and conducting regular inspections, you can help ensure the safety and reliability of your hydraulic systems.
How Often Should Hydraulic Hoses Be Tested
The frequency of hydraulic hose testing depends on several factors, including:
- Operating Environment: Harsh environments may require more frequent inspections.
- Hose Age: Older hoses may need more frequent checks.
- Usage: Heavy-duty applications may necessitate more frequent inspections.
General guidelines:
- Monthly Inspections: For most applications, monthly visual inspections are recommended.
- Annual Inspections: Annual pressure testing and flex testing are typically sufficient.
However, it’s important to note that these are general guidelines, and the specific inspection frequency should be determined based on a risk assessment and the manufacturer‘s recommendations.
Additional Tips:
- Keep detailed records of all inspections and maintenance performed on hydraulic hoses.
- Replace damaged or worn hoses promptly to prevent further damage and downtime.
- Consult with a hydraulic hose specialist to determine the optimal inspection frequency for your specific application.
By following these guidelines and conducting regular inspections, you can help ensure the safety and reliability of your hydraulic systems.
How to Inspect a Hydraulic System
How do you inspect a hydraulic system?
A thorough inspection of your hydraulic system is crucial to ensure its optimal performance and longevity. Here’s a step-by-step guide:
Safety First:
- Depressurize the System: Always ensure the system is depressurized before starting any inspection or maintenance.
- Wear Protective Gear: Use safety glasses, gloves, and appropriate clothing to protect yourself from potential hazards like high-pressure fluid.
Visual Inspection:
- Hose Inspection:
- Check for cuts, cracks, abrasions, or other signs of damage.
- Look for evidence of heat damage, such as discoloration or blistering.
- Inspect for any signs of chemical exposure, such as swelling or softening.
- Verify that all fittings are securely tightened and free of leaks.
- Hydraulic Fluid:
- Check the fluid level in the reservoir.
- Inspect the fluid for color, clarity, and contaminants.
- Check for any signs of foaming or excessive aeration.
- Hydraulic Components:
- Inspect pumps, valves, cylinders, and other components for leaks, damage, or excessive wear.
- Check for any unusual noises or vibrations.
- Verify that all electrical connections are secure and free of corrosion.
Functional Inspection:
- Pressure Testing:
- Use a pressure gauge to verify that the system can withstand the required operating pressure.
- Check for any leaks during pressure testing.
- Performance Testing:
- Operate the system to check for proper functionality and responsiveness.
- Listen for any unusual noises or vibrations.
- Monitor system temperature and pressure gauges for any abnormalities.
Additional Considerations:
- Maintenance Records: Keep detailed records of all inspections, maintenance, and repairs.
- Operating Environment: Consider the harshness of the operating environment and adjust your inspection frequency accordingly.
- Manufacturer‘s Recommendations: Follow the manufacturer‘s guidelines for specific inspection and maintenance procedures.
Regular inspection and maintenance are essential to ensure the long-term performance and reliability of your hydraulic system. By following these steps, you can prevent costly breakdowns and downtime. If you encounter any issues during your inspection, consult with a qualified technician for further diagnosis and repair.
Conclusion
You can significantly reduce the risk of unexpected failures, costly downtime, and potential safety hazards by diligently inspecting your hydraulic hoses for signs of wear and tear. Remember, a small investment in preventative maintenance can save you substantial costs in the long run.
Ready to upgrade your hydraulic system with top-quality hoses? Contact us today to explore our extensive range of wholesale hydraulic hoses. Our expert team is dedicated to providing you with reliable and durable solutions tailored to your specific needs.
Don’t compromise on the health of your hydraulic system. Choose [Your Company Name] for premium hydraulic hoses and expert advice.