Understanding hydraulic hose flow and velocity is critical not only to system efficiency but also to its health and longevity. It’s not enough to simply connect a pump to an actuator; how fast the hydraulic fluid flows through the hose can directly impact pressure drop, heat generation, and even component life. Getting the flow and velocity wrong can lead to cavitation, premature wear, and wasted energy, which can seriously impact system performance.
This guide will dive into the principles of hydraulic hose flow and velocity, explain how they relate to each other, and provide practical tips for calculating and managing them effectively. My goal is to equip you with the knowledge to design and maintain hydraulic systems that operate at peak efficiency, minimize common problems, and maximize productivity.
The Importance of Optimizing Flow and Velocity in Hydraulic Hose
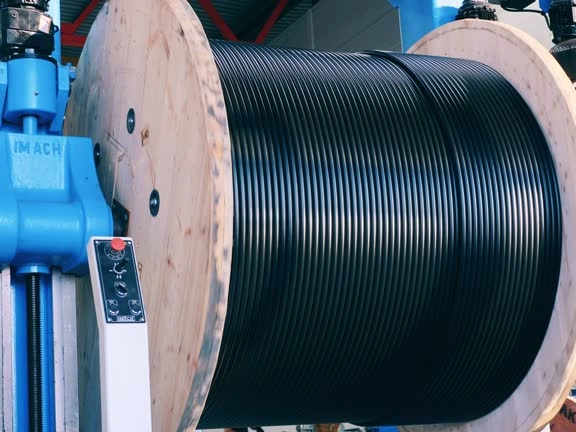
When fluid flows too fast, it can create excessive friction, causing a significant pressure drop in the hose. This means less power reaches the actuator, forcing the pump to work harder, consume more energy, and generate more heat. Conversely, if fluid flows too slowly, the system becomes sluggish and inefficient, failing to meet performance demands.
In addition to efficiency, improper velocity can lead to damaging phenomena such as cavitation, where tiny bubbles form and collapse, corroding hose liners and other components. It can also cause turbulence and increase noise and vibration. Ultimately, optimizing flow and velocity can extend the life of hydraulic hoses, fittings, pumps, and valves, saving significant maintenance and replacement costs in the long run.
Understanding the Fundamentals: Flow Rate vs. Velocity
When we talk about hydraulic hose flow and velocity, it’s crucial to differentiate between these two closely related, yet distinct, concepts. I often see them used interchangeably, which can lead to miscalculations and system inefficiencies.
What is Hydraulic Flow Rate?
Hydraulic flow rate refers to the volume of fluid that passes through a given point in the hydraulic system per unit of time. It’s typically measured in units like gallons per minute (GPM) in the imperial system or liters per minute (LPM) in the metric system. The flow rate is primarily determined by the output of your hydraulic pump. For example, a 10 GPM pump will generate a 10 GPM flow rate, assuming no major leaks or diversions. It’s about how much fluid is moving.
What is Hydraulic Fluid Velocity?
Hydraulic fluid velocity, on the other hand, refers to the speed at which the fluid moves through the hose or pipe. It’s typically measured in feet per second (ft/s) or meters per second (m/s). Unlike flow rate, velocity is not solely determined by the pump’s output. It’s also heavily influenced by the internal diameter (ID) of the hose. Imagine a fixed volume of water flowing through a wide pipe versus a narrow pipe; the water will move much faster through the narrower pipe. It’s about how fast the fluid is moving.
While your pump dictates the flow rate, the diameter of your hose dictates the velocity for that given flow rate. This distinction is the cornerstone of optimizing your hydraulic system.
How Hose Size Impacts Velocity
The interplay between flow rate and hose internal diameter is where the magic (or misery) of hydraulic hose flow and velocity happens. For a constant flow rate, a smaller hose ID means higher fluid velocity, and a larger hose ID means lower fluid velocity.
Let’s illustrate this with a simple analogy: think of a river. If the same amount of water (flow rate) is moving through a wide, shallow section (large hose ID), it moves slowly. If that same amount of water enters a narrow canyon (small hose ID), it speeds up dramatically.
This relationship is vital because velocity has recommended ranges for different parts of a hydraulic circuit to ensure optimal performance and avoid issues.
Recommended Velocity Ranges (General Guidelines)
Based on industry best practices and my own experience, here are some general guidelines for optimal fluid velocity in various parts of a hydraulic system:
Circuit Section | Recommended Velocity (ft/s) | Recommended Velocity (m/s) | Considerations |
Suction Lines | 2 to 4 | 0.6 to 1.2 | Avoid cavitation; minimize pressure drop at pump inlet. |
Pressure Lines | 10 to 20 | 3 to 6 | Balance pressure drop, heat generation, and response time. |
Return Lines | 4 to 15 | 1.2 to 4.5 | Minimize pressure drop back to reservoir; avoid excessive back pressure. |
Actuator Lines | 10 to 20 (can vary) | 3 to 6 (can vary) | Minimize pressure drop back to the reservoir; avoid excessive back pressure. |
How to Calculate Hydraulic Hose Velocity?
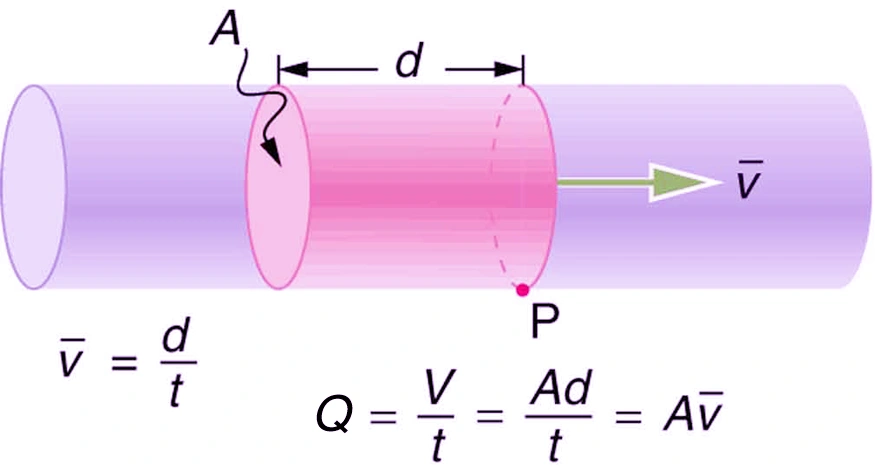
To ensure you’re within these optimal ranges, you need to be able to calculate hydraulic hose velocity. The formula is straightforward once you have the necessary values.
The basic formula for fluid velocity is:
V=AQ
- V = Velocity
- Q = Flow Rate
- A = Cross-sectional Area of the hose’s inner tube
However, since hoses are typically round, we can derive a more practical formula using the hose’s internal diameter (ID).
Formula for Imperial Units (GPM, Inches, ft/s):
V (ft/s)=ID2 (inches2)0.3208×Q (GPM)
- 0.3208 is a constant that converts GPM to cubic feet per second and accounts for the area of a circle.
- Q = Flow rate in Gallons Per Minute (GPM)
- ID = Inside Diameter of the hose in inches
Formula for Metric Units (LPM, mm, m/s):
V (m/s)=ID2 (mm2)21.22×Q (LPM)
- 21.22 is a constant that converts LPM to cubic meters per second and accounts for the area of a circle.
- Q = Flow rate in Liters Per Minute (LPM)
- ID = Inside Diameter of the hose in millimeters
Practical Example: Calculating Pressure Line Velocity
Suppose we have a hydraulic system:
- Flow Rate (Q) = 20 GPM
- Hose Internal Diameter (ID) = 0.75 inches (3/4 inch hose)
Using the imperial formula: V=0.7520.3208×20 V=0.56256.416 V≈11.41 ft/s
Referring back to our table, 11.41 ft/s falls within the recommended 10 to 20 ft/s range for pressure lines. This tells us the hose size is appropriate for this flow rate.
The Consequences of Incorrect Hydraulic Hose Flow and Velocity
Ignoring the proper guidelines for hydraulic hose flow and velocity can lead to a cascade of problems within your system. I’ve seen these issues manifest in various ways, all of which impact performance and cost.
Issues with Excessively High Velocity:
- Increased Pressure Drop: More friction means more energy loss, leading to less available pressure at your actuators. This forces your pump to work harder, consuming more power.
- Excessive Heat Generation: Friction converts fluid energy into heat. High velocity leads to significant heat buildup, which degrades hydraulic fluid, seals, and other components, shortening their lifespan.
- Cavitation: If velocity is too high, especially in suction lines, local pressure can drop below the fluid’s vapor pressure, causing gas bubbles to form. When these bubbles move to higher-pressure areas, they violently collapse, eroding metal surfaces and hose linings. This creates a distinctive “rattling” noise.
- Noise and Vibration: Turbulent fluid flow at high velocities generates more noise and vibration throughout the system, leading to discomfort and potential loosening of components.
- Hose Erosion: The constant, high-speed flow of fluid, especially if contaminated with even small particles, can erode the inner lining of the hose, shortening its service life.
Issues with Excessively Low Velocity:
- Sluggish System Response: Low velocity means your actuators will operate slowly, impacting productivity and system efficiency.
- Poor Heat Dissipation: While high velocity generates heat, very low velocity can hinder the fluid’s ability to dissipate heat effectively throughout the system or to a cooler, leading to localized hot spots.
- Sedimentation: In systems with less-than-perfect filtration, very slow flow can allow particles and contaminants to settle out within the hose or reservoir, potentially clogging passages or abrasive wear when flow eventually resumes.
- Inefficient Use of Components: Oversized hoses for the given flow rate mean you’ve invested in more material than necessary, adding unnecessary weight and cost.
Practical Tips for Managing Hydraulic Hose Flow and Velocity
As a system designer or maintenance professional, you have several levers to pull to ensure optimal hydraulic hose flow and velocity. Here are my top recommendations:
- Size Hoses Correctly from the Start: This is the most crucial step. Use the velocity formulas and recommended ranges during the design phase. Don’t simply use the same size hose as the port on the pump or valve; verify it for your specific flow rate.
- Consider Different Hose Sizes for Different Lines: As shown in the velocity table, suction lines typically require larger IDs than pressure lines to prevent cavitation, while return lines might be sized slightly larger than pressure lines to minimize back pressure.
- Minimize Hose Length and Bends: Every foot of hose and every bend introduces friction and pressure drop. Route hoses as directly as possible with the fewest and largest radius bends permissible.
- Select the Right Fittings: Ensure that fittings have an adequate internal bore size. Restrictive fittings can act as bottlenecks, causing localized high velocity and pressure drops, negating the benefits of correctly sized hoses.
- Regularly Monitor System Performance: Pay attention to system temperature, noise levels, and actuator speed. Sudden changes can indicate issues with fluid flow or velocity, potentially stemming from a hose problem.
- Maintain Fluid Cleanliness: Contaminants accelerate hose erosion at any velocity. Good filtration practices are paramount.
- Consult OEM Specifications: Always refer to the original equipment manufacturer’s (OEM) guidelines for specific velocity recommendations for their machinery, as these may be optimized for their particular components.
Conclusion
Understanding the concepts of hydraulic hose flow and velocity is fundamental to the effective design and maintenance of hydraulic systems. By carefully calculating and optimizing these factors, you can significantly reduce energy consumption, minimize heat generation, prevent damaging cavitation, and extend the life of valuable hydraulic components.
If you have any questions about a specific application or need help calculating the ideal hose size for your hydraulic system, please feel free to ask us.