Hydraulic hoses are essential components in many industries, from construction and agriculture to manufacturing and automotive. They are used to transmit high-pressure hydraulic fluid, powering various machinery and equipment. However, connecting hydraulic hoses can be a complex task that requires specific skills and tools.
In this blog post, we will guide you through the process of connecting hydraulic hoses safely and efficiently. We will cover the necessary tools, safety precautions, and step-by-step instructions to ensure a successful connection. Whether you’re a seasoned mechanic or a DIY enthusiast, this guide will provide you with the knowledge you need to tackle this task with confidence.
Let’s get started!
How to Connect Hydraulic Hoses
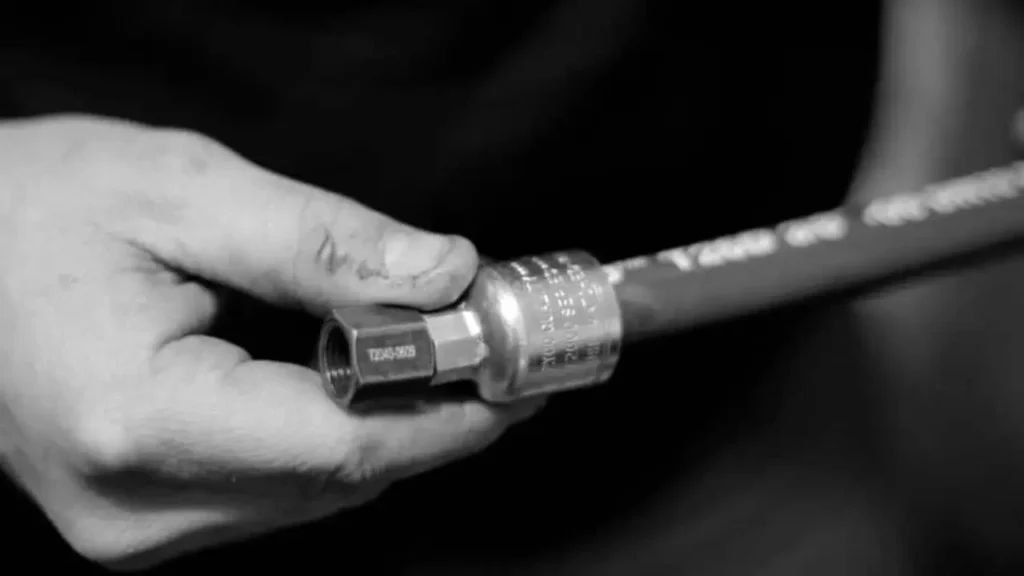
Connecting hydraulic hoses can be a complex task, and it’s important to follow proper procedures to ensure a safe and secure connection. Here’s a general guide on how to connect hydraulic hoses:
Materials and Tools:
- Hydraulic hose
- Hose fitting
- Hydraulic crimping tool
- Grease
- Wrench
Steps about connecting hydraulic hoses:
Step 1. Prepare the Hydraulic Hose:
- Accurate Cutting: Use a high-quality hose cutter designed for hydraulic hoses to ensure a clean, precise cut. Avoid using tools that could damage the hose’s internal structure.
- Thorough Cleaning: Remove any dirt, debris, or burrs from the cut end of the hose. Use a wire brush or a specialized cleaning tool to ensure a clean surface.
- Proper Lubrication: Apply a compatible hydraulic lubricant or grease to the inside of the fitting. This reduces friction and makes assembly easier. Avoid using excessive amounts, as this can lead to contamination.
Step 2. Insert the Fitting:
- Correct Orientation: Ensure that the fitting is inserted into the hose in the correct orientation. Misalignment can lead to improper crimping and potential leaks.
- Full Insertion: Push the fitting fully into the hose until it reaches the stop. This ensures a secure connection and proper crimping.
Step 3. Crimp the Fitting:
- Choosing the Right Die: Select the appropriate crimping die for the specific fitting and hose size. Incorrect die selection can result in inadequate crimping and potential failures.
- Proper Alignment: Align the hose assembly with the crimping die, ensuring that the fitting is positioned correctly.
- Complete Crimping Cycle: Activate the crimping tool and follow the manufacturer‘s instructions to complete the full crimping cycle. This ensures a strong, leak-proof connection.
Step 4. Check for Hydraulic Hose Leaks:
- Visual Inspection: Carefully inspect the crimped connection for any visible signs of damage, cracks, or misalignment.
- Pressure Testing: Apply hydraulic pressure to the hose assembly and check for leaks around the fitting. Use leak detection fluid or a pressure gauge to identify any potential issues.
- Functional Testing: If applicable, test the hydraulic system to ensure proper operation and the absence of leaks.
Additional Considerations:
- Hose and Fitting Compatibility: Ensure that the hose and fitting are compatible with the hydraulic fluid and pressure requirements of the system.
- Crimping Tool Calibration: Regularly calibrate the crimping tool to maintain accurate crimping force and ensure reliable connections.
- Hose Routing and Support: Properly route the hose to avoid excessive stress, kinking, or rubbing against sharp edges. Use hose clamps or straps to secure the hose in place.
- Regular Inspection: Periodically inspect hydraulic hoses for signs of wear, damage, or leaks. Replace any damaged hoses promptly.
- Safety Precautions: Always wear appropriate personal protective equipment (PPE), such as safety glasses and gloves, when working with hydraulic hoses and high-pressure systems.
By following these guidelines and taking necessary precautions, you can safely and effectively connect hydraulic hoses, ensuring the reliability and safety of your hydraulic system.
Hydraulic Hose Connection Types
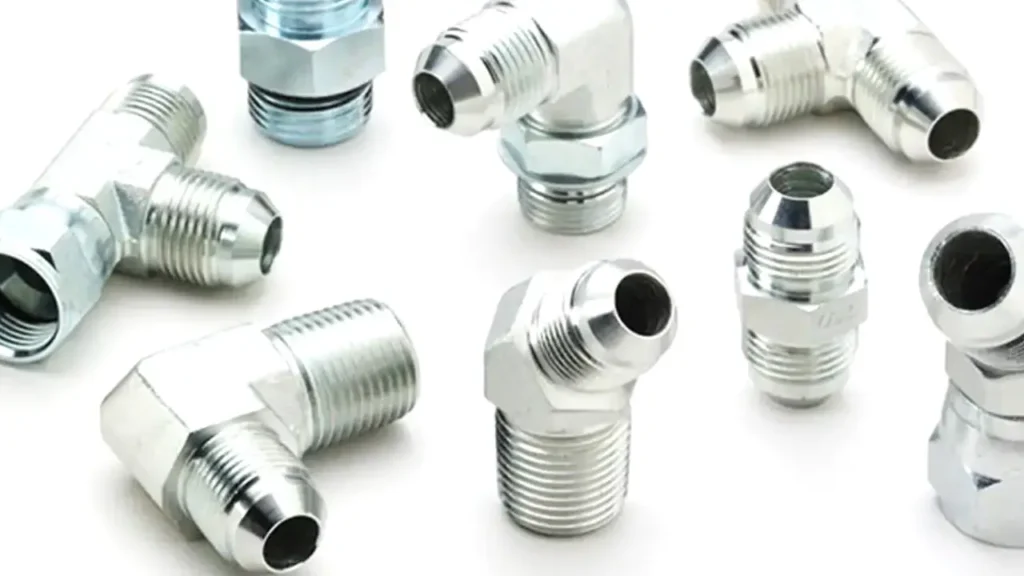
There are several types of hydraulic hose connections, each with its advantages and applications. Here are some of the most common types:
1. O-Ring Face Seal (ORFS):
- Reliable and leak-proof connection.
- Suitable for high-pressure applications.
- Requires proper alignment and torque to ensure a good seal.
2. SAE 45° Flare:
- Common connection type for hydraulic systems.
- Relatively easy to assemble and disassemble.
- May require frequent maintenance to prevent leaks.
3. JIC 37° Flare:
- Similar to SAE 45° flare but with a slightly different angle.
- Common in North American applications.
- Requires proper flaring tool and torque to ensure a good seal.
4. Metric Cone and Seat:
- Common in European and Asian applications.
- Offers a reliable and leak-proof connection.
- Requires proper assembly and torque to ensure a good seal.
5. Tapered Thread:
- Simple and easy to assemble.
- May require thread sealant to prevent leaks.
- Less reliable than other connection types for high-pressure applications.
6. Crimped Fittings:
- Permanent connection that offers excellent reliability and leak-proof performance.
- Requires specialized crimping tools to assemble.
- Cannot be disassembled without damaging the hose and fitting.
7. Reusable Fittings:
- Can be disassembled and reassembled multiple times.
- Less reliable than crimped fittings, especially for high-pressure applications.
- May require frequent maintenance to prevent leaks.
The choice of connection type depends on various factors, including pressure rating, fluid compatibility, ease of assembly, and maintenance requirements. It is important to select the appropriate connection type for the specific application to ensure a reliable and leak-free hydraulic system.
Why Hydraulic Hoses Won’t Connect
Hydraulic hoses failing to connect properly can stem from a variety of issues, often related to compatibility, damage, or improper installation. One primary reason is mismatched fittings. Hydraulic systems utilize numerous fitting types (JIC, NPT, ORFS, etc.), each with distinct thread patterns and sealing mechanisms. If the hose end fitting doesn’t precisely match the port or adapter on the equipment, a secure connection is impossible. This can manifest as:
- Incorrect Thread Type: NPT (tapered) vs. JIC (flared) threads, for instance, are incompatible.
- Mismatched Thread Size: Even within the same thread type, thread sizes must be identical.
- Different Sealing Methods: O-ring face seal (ORFS) fittings rely on an O-ring for sealing, which won’t work with a flared fitting.
Physical damage to the hose or fittings is another common culprit. Over time, hoses can become worn, corroded, or deformed, preventing a proper seal. Dents, crushed threads, or damaged sealing surfaces on fittings can also lead to connection failures. Additionally, debris or contamination within the hose or fittings can obstruct the connection or prevent a proper seal. This includes:
- Damaged Threads: Cross-threading or impact damage can render threads unusable.
- Corrosion: Rust or other corrosion can degrade fittings and sealing surfaces.
- Debris: Dirt, metal shavings, or other contaminants can block the connection.
Finally, incorrect hydraulic hose installation techniques can also contribute to connection problems. Over-tightening fittings can damage threads or sealing surfaces, while under-tightening can lead to leaks. Improper alignment during installation can also cause cross-threading or damage to the fittings. Furthermore, using incorrect tools or improper procedures can lead to connection failures. Some important points include:
- Cross Threading: Forcing a fitting that is missaligned will damage the threads.
- Improper Sealing: Not using the correct sealing method, or damaged seals.
- Incorrect Torque: Over or under tightening fittings.
Conclusion
Successfully connecting hydraulic hoses is a crucial skill for many industries. By following the steps outlined in this guide, you can ensure safe and efficient connections. Remember to always prioritize safety, use the right tools, and double-check your work.
Need Competitive Hydraulic Hoses?
If you need custom hydraulic hoses tailored to your specific needs, look no further. Our hydraulic hose manufacturer specializes in providing high-quality, custom hydraulic hoses. Our experienced team can help you select the right hose and fittings for your application.
Contact us today to learn more about our custom hydraulic hose solutions.
By choosing Gushan Rubber, you’re choosing reliability, quality, and expert service.