When there’s an unexpected leak and downtime means financial loss, the urge to try to patch a hydraulic hose with duct tape is understandable. But is this a viable solution, even if only temporarily, or a dangerous gamble that could lead to bigger problems?
In this guide, I’ll dive into the realities of trying to patch a hydraulic hose with duct tape. We’ll explore why this practice is generally discouraged, the specific risks it poses, and what actually constitutes a safe and effective temporary fix and, more importantly, a permanent fix.
Pros and Cons of Repairing Hydraulic Hoses
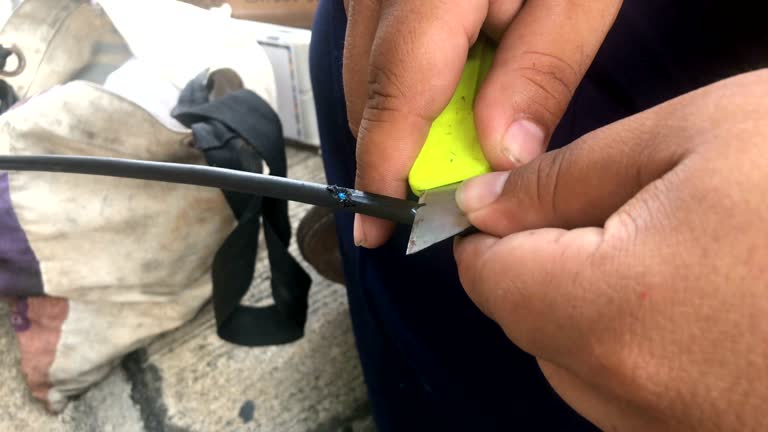
When a hydraulic hose bursts or develops a leak, especially in the field, the first thought for many is: “How can I stop this fluid loss right now?” This is where the idea to repair a hydraulic hose with tape often emerges. It seems simple, quick, and readily available. A roll of duct tape, electrical tape, or even specialized “repair tape” might be on hand, offering a seemingly immediate solution to prevent further fluid loss and perhaps limp the machine back to a proper repair facility.
This immediate appeal masks significant dangers. Hydraulic systems operate under immense pressures, often reaching thousands of pounds per square inch (PSI). Tapes, by their very nature, are designed for adhesion and light containment, not for holding back high-pressure hydraulic fluid.
The forces involved can easily blow through or push past tape, turning a minor leak into a catastrophic spray, posing severe risks of fluid injection injuries, machine damage, and environmental contamination. It’s a tempting but fundamentally unsafe approach.
Why You Should Never Repair Hydraulic Hose With Tape
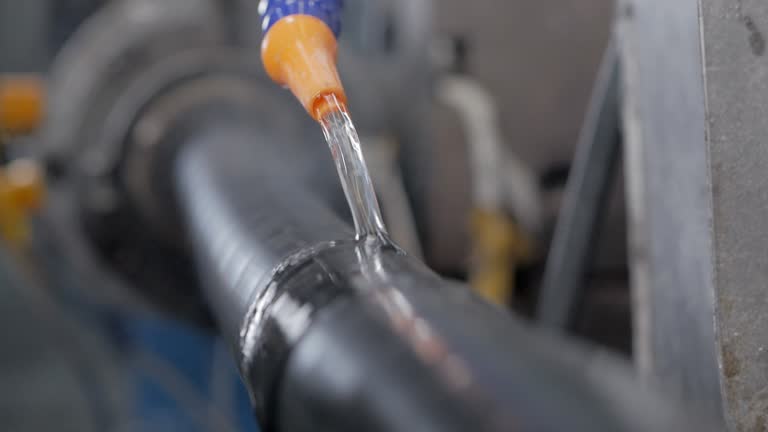
From my professional perspective, attempting to repair a hydraulic hose with tape is almost universally discouraged for critical hydraulic lines. The inherent characteristics of hydraulic systems make tape an unsuitable material for a safe or even reliably temporary repair. Let’s break down the core reasons why this practice is so risky.
The Pressure Problem: Tapes Versus PSI
Hydraulic systems are all about power transmission through pressurized fluid. Depending on the application, working pressures can range from a few hundred PSI to over 10,000 PSI. Consider typical tapes:
- Duct Tape: Designed for general-purpose sealing, not pressure containment. It might withstand a few PSI at best.
- Electrical Tape: Insulating properties are its strength, not pressure resistance.
- Fiberglass/Rescue Tape: While these self-fusing silicone tapes offer better tensile strength, they are still limited. They might temporarily slow a very low-pressure weep, but they are not rated for the dynamic, high pressures of hydraulic systems.
No commercially available tape is engineered to reliably withstand the typical operating pressures of a hydraulic hose. The fluid will find the path of least resistance, forcing its way under, around, or directly through the tape, often with explosive force.
The Fluid Compatibility Issue: Oil, Heat, and Adhesion
Hydraulic fluid is specifically formulated from petroleum-based or synthetic oil. These fluids, especially when hot, can rapidly degrade the adhesives and materials in many common tapes.
- Adhesive Breakdown: The solvents and temperature of hydraulic oil will quickly attack and dissolve the adhesive on tapes, causing them to lose their grip and peel away.
- Material Degradation: Some tape materials themselves are not resistant to hydraulic fluid, leading to softening, swelling, or complete disintegration.
- High Temperatures: Hydraulic systems often run hot. This heat further weakens tape adhesives and materials, accelerating their failure under pressure.
Even if a tape could momentarily hold back pressure, its integrity would be compromised almost immediately by the fluid and heat, leading to rapid failure.
Safety Risks: The Most Critical Concern
This is where attempting to repair hydraulic hose with tape transitions from ineffective to downright dangerous. A failing high-pressure hydraulic hose is not just a messy leak; it’s a severe safety hazard.
- Fluid Injection Injuries: A pinhole leak or burst from a taped repair can spray hydraulic fluid with enough force to penetrate skin, causing a fluid injection injury. This is a medical emergency that can lead to amputation, severe infection, or even death if not treated immediately by medical professionals who understand hydraulic injection injuries. The entry wound might look minor, but the internal damage can be catastrophic.
- Machine Malfunction/Loss of Control: A sudden hose failure can lead to a loss of hydraulic power to critical machine functions (e.g., steering, braking, lifting). This can result in loss of control, causing collisions, drops of heavy loads, or other serious accidents.
- Fire Hazard: Hydraulic fluid is flammable. A high-pressure spray onto a hot engine manifold or exhaust system can ignite, leading to a catastrophic fire.
- Environmental Contamination: Uncontrolled fluid leaks cause environmental damage and can incur heavy fines.
Given these severe risks, any attempt to repair hydraulic hose with tape must be viewed as an extreme last resort in an emergency, used only to safely move equipment away from immediate danger, and with the utmost caution. It is never a long-term solution.
When a Taped Repair Might Be Considered (and Its Limitations)
While I strongly advise against it for high-pressure lines, there might be extremely rare, specific scenarios where a temporary taped “repair” is considered, and only with a full understanding of its severe limitations and risks.
Extremely Low-Pressure (Non-Hydraulic) Applications:
- Drain Lines / Non-Pressurized Return Lines: For very low-pressure or gravity-fed drain lines that are merely weeping or seeping, and where the fluid is non-hazardous and relatively cool, a temporary tape wrap might slow the leak enough to allow for a planned shutdown and proper repair. This is not a hydraulic power line.
- Covering a Scuff/Abrasion: If the hose cover (outer layer) is scuffed or abraded but the underlying reinforcement layers are clearly intact, a strong, fluid-resistant tape might be used to prevent further external damage until the hose can be replaced. This is preventative, not a pressure repair.
Absolute Emergency (and Immediately Followed by Proper Repair):
- Moving Equipment Off a Roadway/Out of Immediate Danger: In an absolute emergency where a machine is completely immobilized by a leak in a critical location (e.g., blocking traffic, in a dangerous excavation), and no other immediate solution is possible, a tape might be applied with the hydraulic system immediately shut down and depressurized. The goal is purely to get the machine to a safer spot for proper repair, with minimal pressure applied during the move. The machine should then be fully shut down and properly repaired at the earliest opportunity.
Even in these rare scenarios, the tape is not repairing the hose. It’s, at best, a containment measure that buys minutes, not hours or days. The system should be operated at the absolute minimum pressure necessary, and a permanent, proper repair (hose replacement) must be the immediate next step.
The Proper Way to Address a Leaking Hydraulic Hose
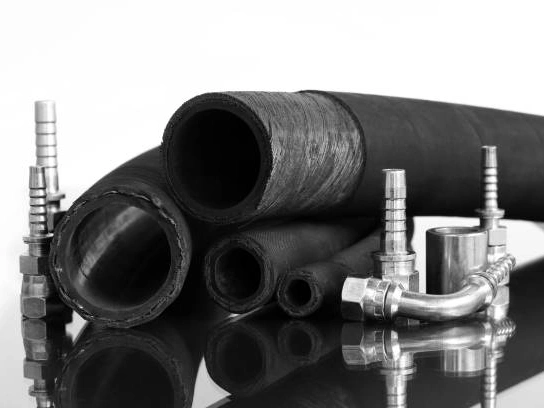
Instead of trying to repair a hydraulic hose with tape, your focus should always be on proper, safe, and effective solutions. These involve either a temporary field-expedient repair kit for immediate needs or, ideally, a complete hose replacement.
Step 1: Safety First – Immediately Depressurize the System
No matter the leak, the very first step is to shut down the hydraulic system and fully depressurize it. This means turning off the engine/motor, cycling the controls to release any trapped pressure in actuators, and potentially opening bleed valves. Safety precautions, including wearing appropriate PPE (gloves, eye protection), are paramount. Never approach a leaking high-pressure hose without depressurizing the system.
Step 2: Temporary Field Repairs (Not Tape!)
For temporary, field-expedient repairs, certain products are available that are vastly superior to tape. These are still temporary but offer a much safer alternative:
- Hydraulic Hose Repair Clamps/Kits: These kits typically involve a metal sleeve or clamps that are applied over the damaged section of the hose, sometimes with a sealant. They are designed to encapsulate the leak and offer some pressure containment. While still limited compared to a new hose assembly, they are specifically engineered for temporary hydraulic repairs and are a far safer option than tape.
- Emergency Repair Sleeves: Some specialized sleeves can be slid over a damaged section and crimped or clamped into place. These are also designed for limited pressure and duration.
Important Note: Even with these temporary repair kits, the hose should be replaced at the earliest opportunity. These are designed to get you back to a service bay, not to continue operation indefinitely.
Step 3: The Permanent Solution – Hose Replacement
The only truly safe, reliable, and permanent solution for a damaged hydraulic hose is complete hose assembly replacement. This involves:
- Identifying the Correct Hose: Matching the original hose’s type, size (ID and OD), pressure rating, temperature rating, fluid compatibility, and fitting types is crucial. Always use the manufacturer’s specifications.
- Proper Fabrication: A new hose assembly should be professionally fabricated, with fittings correctly crimped or attached according to industry standards.
- Correct Installation: The new hose must be routed properly, avoiding kinks, sharp bends, excessive tension, or abrasion points. Ensure it has enough slack to accommodate machine movement.
- System Bleeding: After installation, the hydraulic system must be properly bled to remove any trapped air, which can cause erratic operation and damage.
- Pressure Testing: If possible, conduct a static and dynamic pressure test to confirm the integrity of the new assembly before putting the machine back into full service.
Preventative Measures: Avoiding the Need for Emergency Repairs
My strongest advice regarding repairing a hydraulic hose with tape is to make it irrelevant by focusing on prevention. Proactive maintenance and proper system design dramatically reduce the likelihood of hose failures.
- Regular Inspections: Implement a routine inspection schedule for all hydraulic hoses. Look for:
- External wear or abrasion: Scuffing, cuts, or worn spots on the outer cover.
- Cracks or hardening: Especially near fittings or in areas exposed to heat.
- Bulges or blisters: Indicates internal reinforcement failure.
- Leaks: Even minor weeping can indicate an impending larger issue.
- Kinks or twists: Improper routing or installation.
- Corrosion on fittings: Can lead to leaks or weakened connections.
- Proper Routing and Installation:
- Avoid Tight Bends: Respect the hose’s minimum bend radius.
- Prevent Abrasion: Use hose clamps, protective sleeves, or routing techniques to keep hoses from rubbing against each other or machine components.
- Allow for Movement: Ensure hoses have enough slack for machine articulation without being stretched.
- Avoid twisting: Install hoses without torsion. Mark the hose to ensure it’s not twisted upon installation.
- Use the Right Hose for the Job: As discussed in our previous blog on “Types of Specialty Hydraulic Hoses,” always ensure the hose matches the pressure, temperature, fluid, and environmental conditions of the application.
- Maintain Fluid Cleanliness: Contaminants are a major cause of internal hose wear and premature failure. Regular fluid analysis and filter changes are vital.
- Scheduled Replacement: For critical applications, consider proactive hose replacement based on manufacturer recommendations or observed service life trends, even if no visible damage is present.
Conclusion
While the idea of trying to repair hydraulic hose with tape might seem like a quick fix in a pinch, the reality is that it’s an incredibly risky and largely ineffective strategy for high-pressure hydraulic lines. The immense pressures, fluid compatibility issues, and severe safety hazards—particularly fluid injection injuries—far outweigh any perceived immediate benefit.
As a professional in this field, I strongly advocate for prioritizing safety and proper procedures. For temporary relief, explore purpose-built hydraulic repair clamps, but always view these as a stopgap measure. The only truly safe, reliable, and permanent solution for a damaged hydraulic hose is complete replacement with a correctly specified and professionally assembled new hose. Invest in prevention through regular inspections and proper installation, and you’ll drastically reduce the likelihood of ever facing the temptation to reach for that roll of tape in an emergency. Your safety, your equipment’s longevity, and your operational efficiency depend on it.
Conclusion
While repairing a hydraulic hose with duct tape may seem like a quick fix in an emergency, the reality is that it is an extremely dangerous and nearly ineffective strategy for high-pressure hydraulic lines. The enormous pressures, fluid compatibility issues, and serious safety hazards far outweigh any perceived immediate benefits.
As professionals in this field, we strongly recommend prioritizing safety and proper operating procedures.