Hydraulic hose clamps are essential components in any hydraulic system. They play a crucial role in ensuring the secure and leak-proof connection of hydraulic hoses, preventing fluid loss and system failure. In this comprehensive guide, we will delve into the world of hydraulic hose clamps, exploring their types, applications, and the factors to consider when selecting the right clamp for your specific needs.
Whether you’re a seasoned hydraulics professional or a DIY enthusiast, understanding the intricacies of hydraulic hose clamps is essential for maintaining the optimal performance and longevity of your hydraulic system.
What Are Hydraulic Hose Clamps
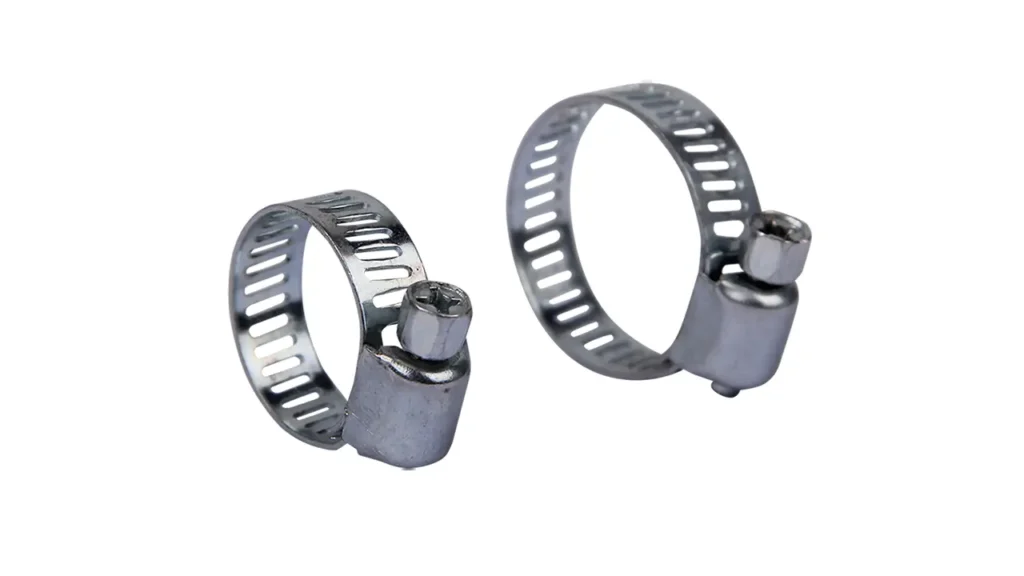
Hydraulic hose clamps are mechanical devices used to secure hydraulic hoses to fittings, preventing leaks and ensuring a secure connection. They are essential components in hydraulic systems, as they provide the necessary clamping force to hold hoses in place, even under high-pressure conditions.
Hydraulic Hose Clamp Types

Here are some common types of hydraulic hose clamps:
Worm Gear Clamps
Worm gear clamps are the most common type of hydraulic hose clamp. They consist of a band with teeth that mesh with a worm gear. By turning the worm gear, the band tightens around the hose, providing a secure grip.
Worm gear clamps are versatile and can be used in a wide range of applications. They are relatively easy to install and remove, making them a popular choice for many hydraulic systems. However, they may not be suitable for high-pressure or high-vibration applications, as the clamping force can diminish over time.
T-Bolt Clamps
T-bolt clamps offer a high clamping force and are ideal for high-pressure applications. They consist of a band with a T-shaped bolt that passes through the band and is tightened with a nut.
T-bolt clamps provide a secure and reliable connection, but they can be more difficult to install and remove than worm gear clamps. They are often used in critical applications where a high level of safety and reliability is required.
Ear Clamps
Ear clamps, also known as Oetiker or pinch clamps, are a type of clamp that uses a crimping tool to create a secure and tamper-resistant connection. They are often used in automotive and aerospace applications, where reliability and safety are paramount.
Ear clamps offer excellent vibration resistance and can withstand high pressures. However, they require a specialized crimping tool for installation, which can limit their use in some applications.
Spring Clamps
Spring clamps use a spring mechanism to provide clamping force. They are often used in automotive applications, where they are easy to install and remove.
Spring clamps are suitable for low-pressure applications and are often used to secure hoses to fittings in engine compartments and under the hood. However, they may not be suitable for high-pressure or high-vibration applications, as the spring tension can diminish over time.
Quick-Release Clamps
Quick-release clamps allow for rapid connection and disconnection of hoses. They are often used in applications where frequent assembly and disassembly are required.
Quick-release clamps are convenient and can save time, but they may not be as durable as other types of clamps. They are typically used in low-pressure applications and may not be suitable for high-pressure or high-vibration environments.
Hydraulic Hose Routing Clamps
Hydraulic hose routing clamps are specifically designed to secure and route hydraulic hoses in a specific way. They are often used to prevent hose chafing, kinking, and interference with other components.
Key Functions of Hydraulic Hose Routing Clamps:
- Protect Hoses: They shield hoses from damage caused by vibration, abrasion, and heat.
- Maintain Hose Integrity: By keeping hoses organized and secure, they help maintain their structural integrity.
- Improve System Aesthetics: They can help to tidy up the appearance of a hydraulic system.
Types of Hydraulic Hose Routing Clamps:
- Strap Clamps: These clamps use a strap or band that is tightened around the hose to secure it to a surface.
- Cable Ties: While not specifically designed for hydraulic hoses, cable ties can be used to bundle and route hoses, especially in low-pressure applications.
- Hose Clips: These clips are designed to attach hoses to specific surfaces, such as engine blocks or chassis frames.
- Hose Clamps with Integrated Routing: Some hose clamps have built-in features to guide and route hoses, such as channels or clips.
Factors to Consider When Choosing Hydraulic Hose Routing Clamps:
- Hose Size and Type: The clamp must be compatible with the size and type of hose.
- Environmental Conditions: The clamp should be resistant to the specific environmental conditions, such as temperature, humidity, and chemical exposure.
- Vibration and Shock: The clamp should be able to withstand vibration and shock, especially in mobile applications.
- Ease of Installation: The clamp should be easy to install and remove.
- Aesthetics: The clamp should be visually appealing and not detract from the overall appearance of the machine or equipment.
By using hydraulic hose routing clamps, you can improve the reliability and lifespan of your hydraulic system, reduce maintenance costs, and enhance the overall performance of your equipment.
What Are Hydraulic Hose Clamps Used for
Hydraulic hose clamps are primarily used to secure hydraulic hoses to fittings in various applications. Their primary function is to prevent leaks and ensure a secure connection, even under high-pressure conditions. This is crucial for maintaining the integrity of hydraulic systems and preventing accidents.
Here are some specific applications of hydraulic hose clamps:
Industrial Machinery:
- Construction Equipment: Clamps secure hoses on excavators, bulldozers, and other heavy machinery.
- Manufacturing Equipment: Clamps are used to secure hoses on hydraulic presses, bending machines, and other industrial equipment.
- Mining Equipment: Clamps are used to secure hoses on mining machinery, which often operates in harsh environments.
Automotive and Transportation:
- Vehicles: Clamps are used to secure hoses in the braking, steering, and cooling systems of vehicles.
- Heavy-Duty Trucks: Clamps are used to secure hoses on heavy-duty trucks and trailers.
Agriculture:
- Farm Equipment: Clamps are used to secure hoses on tractors, combines, and other agricultural machinery.
Marine Applications:
- Boats and Ships: Clamps are used to secure hoses in hydraulic systems for steering, winches, and other marine equipment.
Other Applications:
- Aerospace: Clamps are used to secure hoses in aircraft hydraulic systems.
- Oil and Gas: Clamps are used to secure hoses in oil and gas production and transportation.
By using hydraulic hose clamps, you can ensure the safe and efficient operation of hydraulic systems in a wide range of applications.
How to Clamp Hydraulic Hoses
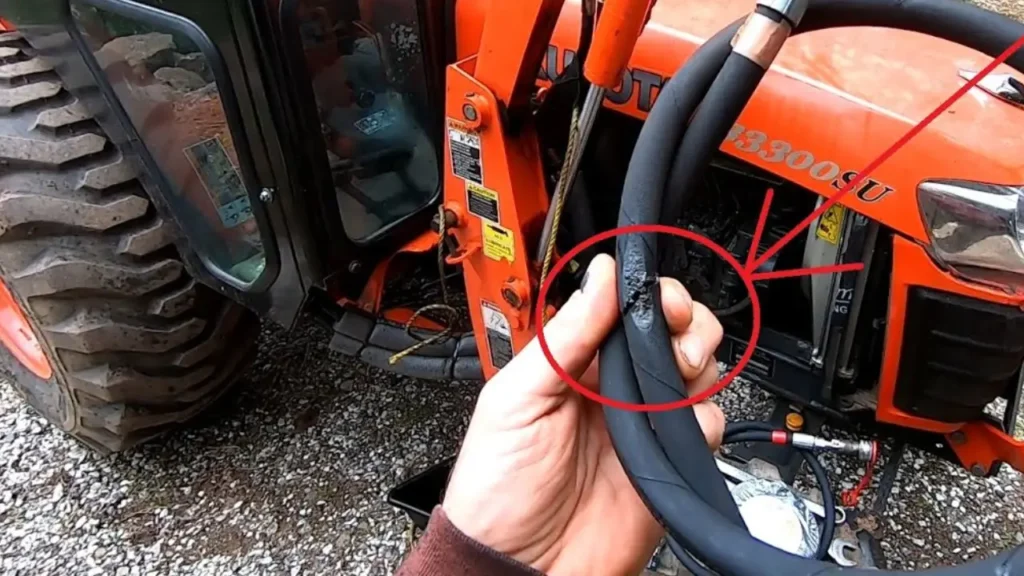
Here’s a step-by-step guide on how to properly use hydraulic hose clamps in the right way:
1. Prepare the Hose and Fitting
Before installing the clamp, ensure the hose and fitting are clean and free of dirt, grease, or debris. Any contaminants can interfere with the seal and reduce the clamp’s effectiveness. Clean the surfaces thoroughly with a suitable cleaning agent and a soft cloth.
2. Select the Right Clamp
Choose a clamp that is appropriate for the size and type of hose. Consider factors like the hose diameter, pressure rating, and the specific application. A clamp that is too small may not provide adequate clamping force, while a clamp that is too large may damage the hose.
3. Position the Clamp
Position the clamp around the hose and fitting, ensuring that it is centered and aligned correctly. The clamp should be positioned close to the fitting to prevent the hose from pulling away.
4. Tighten the Clamp
If you’re using a worm gear clamp, turn the screw clockwise to tighten the band around the hose. For T-bolt clamps, tighten the T-bolt with a wrench. For ear clamps, use a crimping tool to secure the clamp.
When tightening the clamp, apply a consistent and even pressure. Avoid over-tightening, as this can damage the hose and reduce its lifespan.
5. Check for Leaks
Once the clamp is tightened, inspect the connection for any signs of leaks. If you notice any leaks, re-tighten the clamp or replace it with a new one.
6. Regular Inspection
Regularly inspect the clamps for signs of wear, damage, or corrosion. Replace any damaged clamps promptly to prevent potential leaks and failures.
By following these steps and selecting the right hydraulic hose clamp, you can ensure the safety and reliability of your hydraulic system.
How to Choose the Right Hydraulic Hose Clamp
Selecting the right hydraulic hose clamp is crucial to ensure the safety and reliability of your hydraulic system. Here are some key factors to consider when making your choice:
1. Hose Diameter
- Accurate Measurement: Ensure you have the correct measurement of the hose’s outer diameter.
- Clamp Compatibility: Choose a clamp that is designed for the specific hose diameter to ensure a secure fit.
- Avoid Over-Tightening: Over-tightening can damage the hose and reduce its lifespan.
2. Pressure Rating
- System Pressure: Determine the maximum operating pressure of your hydraulic system.
- Clamp Capacity: Select a clamp that can withstand the maximum pressure without compromising its integrity.
- Safety Margin: Consider a clamp with a higher pressure rating than the system’s maximum pressure for added safety.
3. Material Compatibility
- Hose Material: Ensure the clamp’s material is compatible with the hose material to prevent corrosion and degradation.
- Fluid Compatibility: Consider the type of hydraulic fluid used and select a clamp material that is resistant to its effects.
- Environmental Factors: Account for factors like temperature, humidity, and exposure to chemicals when choosing the clamp material.
4. Vibration and Shock Resistance
- Application Environment: Assess the level of vibration and shock that the clamp will be subjected to.
- Clamp Design: Choose a clamp with a robust design and strong materials to withstand these forces.
- Proper Installation: Ensure the clamp is installed correctly to maximize its vibration and shock resistance.
5. Ease of Installation and Removal
- User-Friendly Design: Consider clamps that are easy to install and remove, especially for frequent maintenance or repairs.
- Tool Requirements: Evaluate the tools needed for installation and removal to ensure they are readily available.
- Time Efficiency: Opt for clamps that can be installed quickly and efficiently.
6. Durability and Longevity
- Material Quality: Choose a clamp made from high-quality materials that are resistant to wear and tear.
- Corrosion Resistance: Select a clamp with corrosion-resistant properties, especially for outdoor or harsh environments.
- Regular Inspection: Regularly inspect the clamp for signs of damage or wear and replace it as needed.
By carefully considering these factors, you can select the right hydraulic hose clamp to ensure the safe and efficient operation of your hydraulic system.
Conclusion
Hydraulic hose clamps play a crucial role in ensuring the safety and reliability of hydraulic systems. By understanding the different types of clamps, their applications, and proper installation techniques, you can significantly reduce the risk of leaks, failures, and accidents.
Ready to optimize your hydraulic systems?
Explore our extensive range of high-quality wholesale hydraulic hoses, designed to meet the demands of diverse industries. From construction and agriculture to manufacturing and mining, our hoses offer exceptional durability, flexibility, and resistance to extreme pressures and temperatures.
Contact us today to discuss your specific needs and discover how our hydraulic hoses can empower your operations.