Hydraulic hose failure can lead to significant downtime, costly repairs, and potential safety hazards. Understanding the common causes of hose failure is crucial to prevent such incidents.
In this blog post, we will delve into the primary factors that contribute to hydraulic hose failure and explore effective mitigation strategies to ensure the reliability and safety of your hydraulic systems.
Hydraulic Hose Failure Analysis
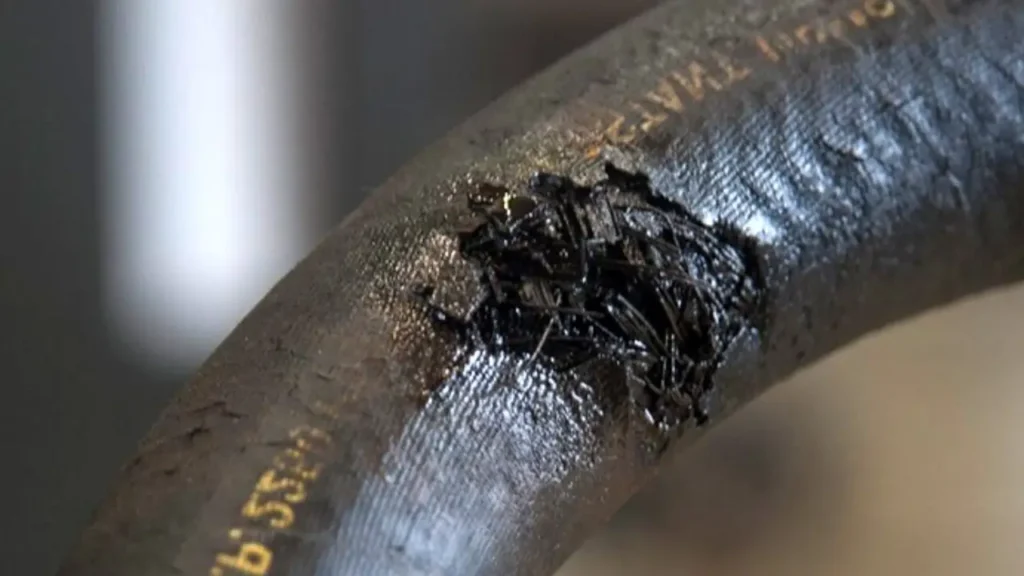
Hydraulic hose failure can lead to significant downtime, safety risks, and costly repairs. To prevent such incidents, it’s crucial to understand the common causes of hose failure and implement preventive measures.
Common Causes of Hydraulic Hose Failure
Hydraulic hose failure can lead to significant downtime, safety hazards, and costly repairs. Understanding the common causes of hose failure is crucial to prevent such incidents. Here’s a deeper look into the most common causes:
1. Abrasion
- Wear and tear caused by friction against nearby components.
- Prevention: Use protective sleeves or guards to shield hoses from abrasion and implement proper routing to minimize contact with other components.
2. Cut or Puncture
- Physical damage caused by sharp objects, impacts, or improper handling.
- Prevention: Avoid routing hoses near sharp edges or potential impact zones. Use caution during installation and maintenance.
3. Excessive Radius Bending
- Exceeding the minimum bend radius can weaken the hose material, leading to cracks and leaks.
- Prevention: Ensure proper hose routing, avoiding sharp bends and kinks.
4. Heat Damage
- Exposure to high temperatures can degrade the hose material, causing it to become brittle and crack.
- Prevention: Use heat-resistant hoses and avoid routing them near heat sources.
5. Fluid Incompatibility
- Using incompatible fluids can cause the hose material to deteriorate and lead to premature failure.
- Prevention: Always use the correct fluid specified by the manufacturer.
6. Improper Hydraulic Hose Installation
- Incorrect installation, such as overtightening fittings or improper routing, can lead to leaks and damage.
- Prevention: Follow the manufacturer‘s instructions and use proper tools and techniques.
7. Age and Fatigue
- Over time, hoses can deteriorate due to age and exposure to various factors.
- Prevention: Implement a regular inspection and replacement schedule.
By understanding these common causes and taking preventive measures, you can significantly reduce the risk of hydraulic hose failure and ensure the safety and reliability of your hydraulic systems.
Analyzing Hydraulic Hose Failures
To prevent future failures, it’s essential to conduct a thorough analysis of failed hoses. This involves:
- Visual Inspection: Examine the failed hose for signs of wear, cuts, cracks, or other damage.
- Fluid Analysis: Check the hydraulic fluid for contamination or degradation.
- Pressure Testing: Test the hose and fittings for leaks and pressure capacity.
- Root Cause Analysis: Identify the underlying cause of the failure, such as improper installation, excessive pressure, or heat damage.
By understanding the root causes of hydraulic hose failures, you can take steps to prevent future incidents and improve the reliability of your hydraulic systems.
How to Solve Hydraulic Hose Damage
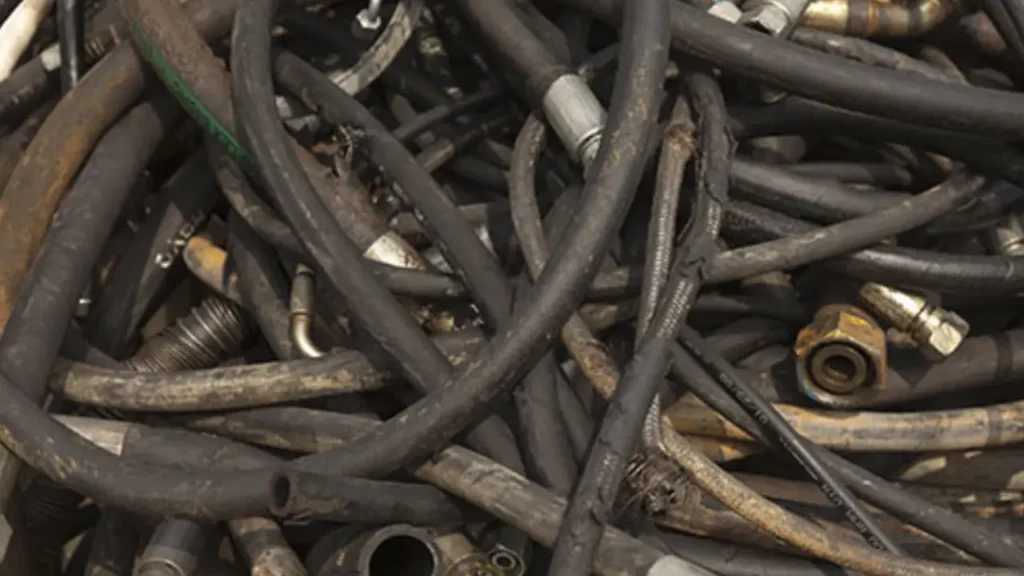
Note: While temporary fixes can be made, it’s crucial to replace a damaged hydraulic hose as soon as possible. Temporary repairs should only be used in emergencies.
1. Assess the Damaged Hydraulic Hose:
- Identify the extent of the damage: Determine if it’s a small leak, a puncture, or a larger tear.
- Check for underlying issues: Look for other potential problems, such as excessive pressure or temperature, that may have contributed to the damage.
2. Temporary Repair (for minor damage):
- Use a Hydraulic Hose Repair Kit: These kits typically include clamps, sleeves, and adhesives to seal small leaks or punctures.
- Follow the instructions: Carefully follow the manufacturer‘s instructions for the specific repair kit.
- Test for Leaks: After applying the repair, test the hose for leaks using soapy water.
3. Professional Repair or Replacement:
- Consult a Specialist: For significant damage or recurring issues, consult a hydraulic hose specialist.
- Professional Repair: A professional can assess the damage, determine the best course of action, and perform a proper repair or replacement.
- Replacement: In most cases, replacing the damaged hose is the most reliable and long-lasting solution.
Preventive Measures:
- Regular Inspection: Regularly inspect hoses for signs of wear, cuts, or leaks.
- Proper Installation: Ensure correct installation and routing to avoid excessive stress.
- Avoid Extreme Conditions: Protect hoses from extreme temperatures, excessive pressure, and harsh chemicals.
- Use Protective Covers: Use protective covers or sleeves to shield hoses from abrasion and other damage.
Remember, a temporary repair is just that – temporary. It’s essential to address the root cause of the damage and replace the hose with a new one to ensure the safety and reliability of your hydraulic system.
Hydraulic Hose Breakdown Prevention Tips
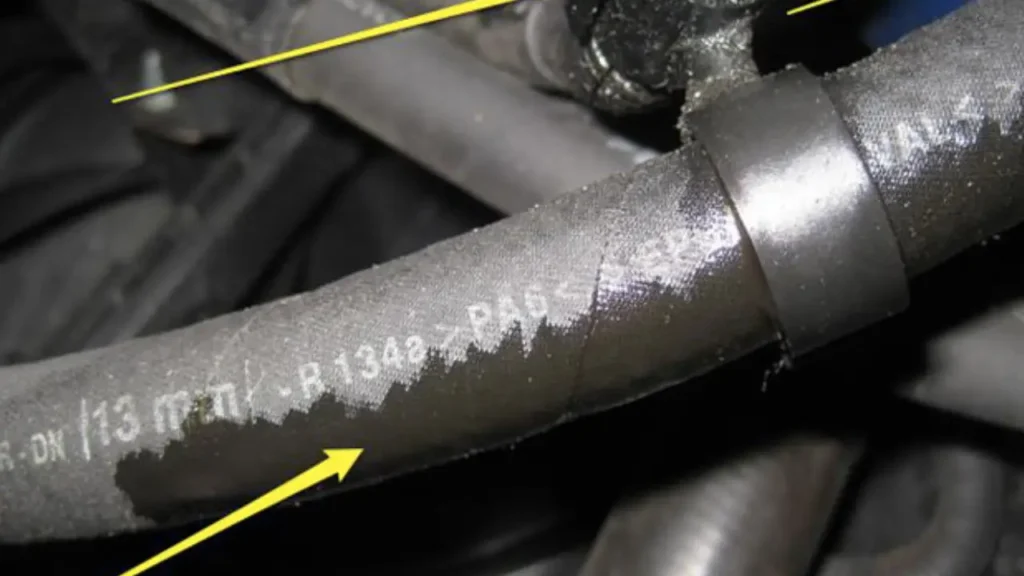
To prevent hydraulic hose failure and ensure the longevity of your hydraulic system, consider these key tips:
Regular Inspection and Maintenance
- Visual Inspection: Regularly check hoses for signs of wear, cuts, cracks, or leaks.
- Pressure Testing: Periodically pressure test hoses to identify potential weaknesses.
- Fluid Contamination: Monitor hydraulic fluid for contamination, as it can accelerate hose degradation.
Proper Installation and Routing
- Avoid Excessive Bending: Excessive bending can weaken the hose and lead to premature failure.
- Protect from Abrasion: Use protective sleeves or guards to shield hoses from abrasion and other damage.
- Secure Hoses: Properly secure hoses to prevent movement and chafing.
- Avoid Heat Sources: Keep hoses away from heat sources to prevent heat damage.
Choose the Right Hose
- Pressure Rating: Select a hose with a pressure rating that exceeds the maximum operating pressure of your system.
- Temperature Rating: Ensure the hose can withstand the temperature extremes of your application.
- Fluid Compatibility: Choose a hose that is compatible with the hydraulic fluid being used.
Additional Tips:
- Regularly Replace Hoses: Even with proper maintenance, hoses will eventually wear out. Replace hoses according to the manufacturer‘s recommended intervals.
- Train Operators: Train operators to recognize signs of hose wear and to report any issues promptly.
- Emergency Procedures: Have a plan in place for handling hydraulic hose failures, including emergency shut-down procedures.
By following these preventative measures, you can significantly reduce the risk of hydraulic hose failures and improve the overall reliability of your hydraulic system.
Conclusion
By understanding the common causes of hydraulic hose failure and implementing preventive measures, you can significantly reduce the risk of equipment downtime and costly repairs. Regular inspection, proper maintenance, and the use of high-quality hoses are crucial for ensuring the reliability and safety of your hydraulic systems.
Ready to upgrade your hydraulic systems with high-quality hoses?
Contact us today to explore our wide range of hydraulic hoses and fittings. Our expert team can help you select the right products for your specific application and provide expert advice on installation and maintenance.