When we think of high-pressure hoses, we usually think of two common types: hydraulic hoses and pressure washer hoses. While both are designed to move fluids at high pressures, their construction, applications, and capabilities are very different. Confusing or using them interchangeably can lead to dangerous malfunctions, inefficiencies, and costly damage. In this guide, we’ll explore the unique differences between hydraulic hoses and pressure washer hoses.
Hydraulic Hose vs Pressure Washer Hose: The Core Function
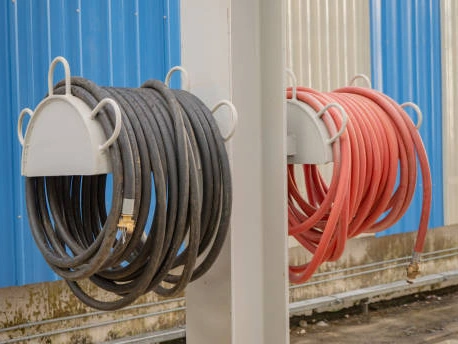
Before we dive into the construction, let’s understand the primary roles each hose plays. While both a hydraulic hose vs pressure washer hose move fluid, the type of fluid, the pressure dynamics, and the ultimate purpose of that fluid transfer are vastly different. Understanding these core functions helps us appreciate why their designs diverge so significantly.
A hydraulic hose is designed to transmit power within a hydraulic system. It carries hydraulic fluid—typically an oil-based fluid—under high, often fluctuating, pressures to actuate hydraulic cylinders, motors, and other components. The fluid itself is the medium for power transmission, and the hose must withstand not just constant pressure but also intense pressure spikes, significant temperature variations, and the chemical properties of the hydraulic fluid.
A pressure washer hose is designed to deliver water, usually cold but sometimes hot, at high pressure to a nozzle for cleaning purposes. While it handles high pressure, the primary goal is flow and impingement force for cleaning, not power transmission to move heavy loads. This fundamental difference in application drives the unique engineering of each hose type.
Anatomy and Construction: Why They Look Alike But Are So Different
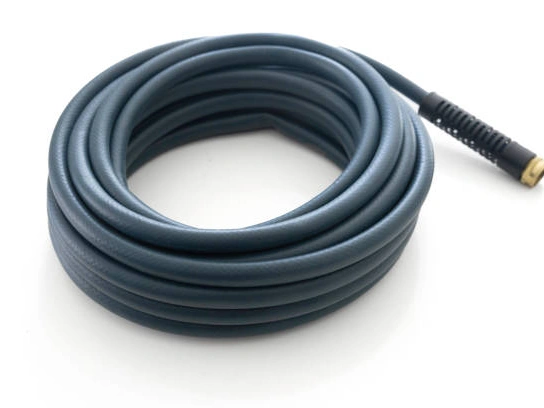
At first glance, a hydraulic hose vs pressure washer hose might appear similar – often black, reinforced, and flexible. However, a closer inspection and understanding of their internal construction reveal the critical differences that dictate their performance and safety. Each component is meticulously chosen and assembled to meet the rigorous demands of its specific environment.
Let’s break down their typical construction:
Hydraulic Hose Construction
A hydraulic hose is engineered for extreme durability and specific performance under demanding conditions. Its multi-layered design provides robust resistance to high pressure, temperature, and chemical exposure.
- Inner Tube: This is the innermost layer that comes into direct contact with the hydraulic fluid. It’s typically made from synthetic rubber (like Nitrile or Neoprene) or sometimes thermoplastic materials. The key characteristic here is fluid compatibility. The material must resist degradation from the specific hydraulic oil used, which can vary widely in chemical composition and temperature.
- Reinforcement Layers: This is the heart of the hydraulic hose’s strength. These layers are usually composed of high-tensile steel wire, braided or spiraled, or sometimes textile braids.
- Braided Hoses: Often feature one or two layers of braided wire. They offer good flexibility and are common in medium-to-high pressure applications.
- Spiral Hoses: Utilize multiple layers (typically four or six) of spiraled steel wire, laid in opposing directions. This construction provides superior strength and flexibility, making them suitable for very high and ultra-high pressure applications where pressure surges are common. The number of layers directly correlates with the hose’s pressure rating.
- Outer Cover: The outermost layer is designed to protect the reinforcement from external damage, including abrasion, ozone, UV radiation, chemicals, and environmental factors. Materials like synthetic rubber or thermoplastic are common, engineered for durability and resistance to nicks and cuts.
Pressure Washer Hose Construction
A pressure washer hose, while also handling high pressure, has a simpler construction tailored for conveying water and resisting abrasion from being dragged across surfaces.
- Inner Tube: Typically made from synthetic rubber (like EPDM or SBR) or sometimes thermoplastic. The primary concern here is water resistance and temperature tolerance if hot water is used. Chemical compatibility is less of an issue compared to hydraulic fluids, although some cleaning agents might need consideration.
- Reinforcement Layer(s): Often consists of one or two layers of textile braiding (e.g., polyester) or, in higher-end or industrial models, a single layer of steel wire braid. The reinforcement provides the burst strength for water pressure, but generally not the dynamic pressure cycling or extreme peak pressures seen in hydraulic systems.
- Outer Cover: Usually made from abrasion-resistant PVC, rubber, or polyurethane. This layer is designed to withstand dragging, scuffing, and exposure to cleaning chemicals and outdoor elements. Flexibility is also a key consideration for ease of use.
Pressure Ratings: A Matter of Scale and Dynamics
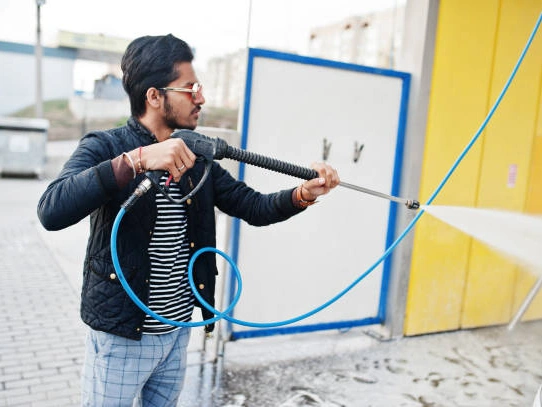
Perhaps the most critical distinction between a hydraulic hose vs pressure washer hose lies in their pressure ratings and how they handle dynamic pressure conditions. Misunderstanding these ratings can lead to catastrophic failure.
Hydraulic Hose Pressure Ratings
Hydraulic hoses are engineered to operate at significantly higher pressures, often ranging from a few hundred PSI (pounds per square inch) to several thousand PSI, with specialized hoses exceeding 10,000 PSI. More importantly, they are designed to withstand dynamic pressure cycling – the repeated, rapid fluctuations in pressure that occur as hydraulic cylinders extend and retract or motors start and stop. These cycles create immense fatigue on the hose’s reinforcement layers. The burst pressure for hydraulic hoses is typically 4 times their maximum working pressure, providing a substantial safety factor. We always adhere strictly to these ratings, knowing that exceeding them, even momentarily, can lead to premature failure or a sudden hydraulic hose burst.
Pressure Washer Hose Pressure Ratings
Pressure washer hoses typically operate in a lower pressure range compared to hydraulic hoses, commonly from 1,500 PSI for residential units to 4,000-5,000 PSI for commercial and industrial models. While these pressures are high for water delivery, they are generally static or slowly changing pressures, without the constant, rapid cycling characteristic of hydraulic systems. The safety factor for burst pressure on pressure washer hoses is often around 3:1, meaning the burst pressure is three times the working pressure. While robust for their intended use, they are simply not built to handle the extreme and dynamic pressure demands of hydraulic power transmission.
Feature | Hydraulic Hose | Pressure Washer Hose |
Primary Function | Transmits power (actuates components) | Delivers water for cleaning |
Fluid Type | Hydraulic oil (various chemical compositions) | Water (cold or hot) |
Typical Pressure Range | 500 PSI – 10,000+ PSI (highly dynamic, with pressure spikes) | 1,500 PSI – 5,000 PSI (generally static or slowly changing) |
Reinforcement | Multi-layered high-tensile steel wire (braided or spiral) | Textile braid or single layer of steel wire braid |
Inner Tube Material | Synthetic rubber (Nitrile, Neoprene) or thermoplastic, optimized for fluid compatibility | Synthetic rubber (EPDM, SBR) or thermoplastic, optimized for water resistance |
Outer Cover Material | Synthetic rubber, thermoplastic (abrasion, ozone, UV, chemical resistant) | PVC, rubber, polyurethane (abrasion resistant for dragging) |
Temperature Range | Wider range, accommodates hot hydraulic oil (e.g., -40°F to 250°F / -40°C to 121°C) | Generally lower, but some handle hot water (e.g., 32°F to 200°F / 0°C to 93°C) |
Flexibility | Can be stiff due to steel reinforcement, especially high-pressure types | Generally more flexible for ease of handling and movement |
Fittings | Specialized, high-pressure fittings (JIC, ORFS, NPT, Metric, BSP) | Specific fittings (M22, 3/8″ Quick Connect, etc.) |
Safety Factor | Typically 4:1 (Burst Pressure: Working Pressure) | Typically 3:1 (Burst Pressure: Working Pressure) |
Fluid Compatibility: More Than Just a Little Bit of Oil
The type of fluid each hose is designed to carry is another critical differentiating factor. We’ve learned that using the wrong hose for the fluid can lead to rapid degradation and premature failure, even if the pressure rating seems sufficient.
Hydraulic hoses are specifically formulated to be compatible with a wide range of hydraulic oils. These oils often contain additives, are designed to operate at elevated temperatures, and can be quite aggressive towards incompatible materials. An inner tube material that isn’t chemically resistant to these oils will quickly soften, swell, or dissolve, leading to internal erosion and ultimately a hydraulic hose burst.
Pressure washer hoses, on the other hand, are primarily designed for water. While some may handle mild cleaning detergents, they are not built to resist the chemical composition and higher temperatures often associated with hydraulic fluids. Introducing hydraulic oil into a pressure washer hose would quickly degrade its inner tube and reinforcement, leading to failure.
Fittings and Connections: Not Interchangeable
The fittings on a hydraulic hose vs pressure washer hose are distinct and not interchangeable. This is a crucial safety aspect that prevents accidental misuse.
Hydraulic hose fittings are robust, often made of steel or stainless steel, and designed to withstand immense pressure and provide a leak-proof seal under dynamic conditions. Common types include JIC (Joint Industry Council), ORFS (O-Ring Face Seal), NPT (National Pipe Taper), BSP (British Standard Pipe), and various metric fittings. These fittings are crimped onto the hose using specialized equipment, creating an extremely strong and permanent connection.
Pressure washer hose fittings are typically simpler, such as M22 threaded connections, 3/8-inch quick connects, or garden hose-type fittings for residential units. While they provide a secure connection for water pressure, they are not engineered to handle the far greater pressures, temperatures, or dynamic stresses of a hydraulic system. Attempting to adapt a pressure washer hose to a hydraulic system, or vice versa, would be extremely dangerous and likely result in immediate failure.
Practical Implications and Safety: Why Knowing the Difference Matters
The differences between a hydraulic hose vs pressure washer hose have profound practical and safety implications. As operators and maintenance professionals, we must always use the correct hose for the job.
- Safety Hazard: Using a pressure washer hose in a hydraulic system is extremely dangerous. It will likely burst under the much higher and more dynamic hydraulic pressures, potentially causing severe injury from fluid injection, burns, or the whipping of a ruptured hose.
- Performance Issues: A pressure washer hose would offer inadequate flow rates and pressure stability for hydraulic applications, leading to poor machine performance and potential damage to hydraulic components.
- Premature Failure: Even if a pressure washer hose somehow withstands initial hydraulic pressure, its material will quickly degrade due to fluid incompatibility and fatigue from dynamic cycling, leading to early failure.
- Costly Downtime: Any hose failure, especially a hydraulic hose burst, results in lost productivity, repair costs, and potential environmental cleanup expenses.
Always verify the hose type, pressure rating, fluid compatibility, and fitting type before installation. If in doubt, consult the equipment’s manual or a hydraulics expert. We prioritize safety and efficiency above all else, which means using the right tool—and the right hose—for the job every single time.
Conclusion
In the hydraulic hose vs. pressure washer hose debate, it becomes apparent that despite their superficial similarities, they are very different products designed for very different uses. Hydraulic hoses are workhorses used to transmit power under extreme pressures, temperatures, and fluid chemistries, and are reinforced with rugged steel. Pressure washer hoses are optimized for efficient delivery of clean water, with reinforcements for lower, less dynamic pressures, and different use environments.
Understanding these fundamental differences is not only a matter of technical knowledge, but also of operational safety, efficiency, and longevity of your equipment. We always emphasize that using the correct hose for the intended use is non-negotiable. It protects people, avoids costly breakdowns, and keeps our machines up and running. Contact us for a tailor-made solution.