Hydraulic hoses are the lifeblood of countless industrial and mobile applications, transmitting vital fluids under immense pressure. The performance and longevity of these systems hinge heavily on the materials used in hose construction.
This blog post will delve into the diverse world of hydraulic hose materials, exploring their unique properties, applications, and considerations for optimal selection.
What Are Hydraulic Hoses Made Of
Hydraulic hoses are typically constructed from several layers of different materials, giving them the strength and durability needed to withstand high pressures and harsh environments.1 Here’s a breakdown of the common materials used:
Inner Tube:
- Synthetic Rubber: Most common, offering good resistance to hydraulic fluids and abrasion.
- Thermoplastic: Used in some applications, known for its flexibility and resistance to low temperatures.
- Teflon (PTFE): Excellent chemical resistance but can be more expensive.
Reinforcement Layer:
- Steel Wire: Provides high strength for handling extreme pressures. Can be braided or spirally wound.
- Synthetic Fibers: Offer flexibility and resistance to abrasion, often used in conjunction with steel wire.
Outer Cover:
- Synthetic Rubber: Protects the inner layers from abrasion, ozone, and other environmental factors.
- Polyurethane: Highly resistant to abrasion and impact, often used in demanding applications.
The specific materials used will vary depending on the intended application of the hose, factors like pressure, temperature, the type of fluid being conveyed, and the operating environment all play a crucial role in material selection.
Hydraulic Hose Material Properties
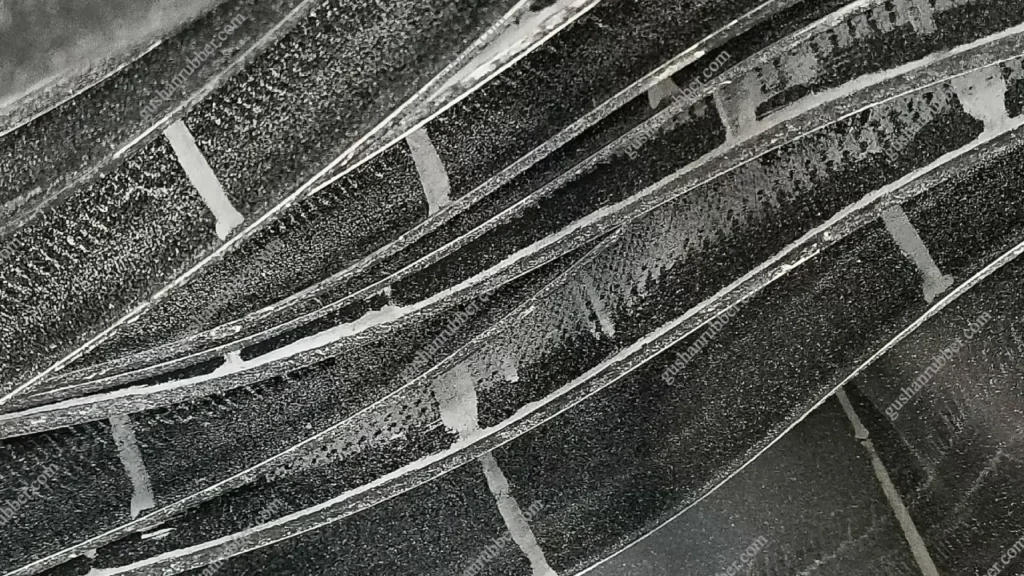
The choice of materials for hydraulic hoses is critical as they directly impact the hose’s performance, lifespan, and safety within a hydraulic system. Here’s a deeper look into the key properties and considerations:
1. Inner Tube:
- Resistance to Hydraulic Fluids: The primary concern. The inner tube must be compatible with the specific hydraulic fluid used (e.g., mineral oil, synthetic fluids, water-glycol mixtures). Incompatibility can lead to:
- Fluid Degradation: The hose material can degrade the fluid, affecting its viscosity and performance.
- Hose Degradation: The fluid can attack the hose material, causing swelling, cracking, or even dissolving it.
- Temperature Resistance:
- High Temperatures: Can cause the hose to harden, crack, or even melt.
- Low Temperatures: Can lead to stiffening and reduced flexibility, potentially hindering fluid flow.
- Abrasion Resistance: Protects against wear and tear from internal flow turbulence or particulate matter in the fluid.
2. Reinforcement Layer:
- Pressure Resistance: The primary function. Steel wire provides exceptional strength to withstand high pressures.
- Braided: Offers flexibility and resistance to pulsation.
- Spirally Wound: Provides higher burst pressure but may have limitations in bending radii.
- Flexibility: Allows for ease of installation and movement within the system.
- Fatigue Resistance: Withstands repeated pressure cycles without weakening or failing.
3. Outer Cover:
- Abrasion Resistance: Protects the inner layers from external damage (e.g., rubbing against machinery, contact with sharp objects).
- Weather Resistance: Resists ozone, UV radiation, and other environmental factors that can degrade the hose.
- Chemical Resistance: Protects against exposure to chemicals, solvents, and other substances that might be present in the operating environment.
- Fire Resistance: In certain applications, fire-resistant materials are crucial for safety.
Key Considerations:
- Compatibility with the Fluid: As mentioned earlier, this is paramount.
- Operating Pressure and Temperature Range: The hose must be able to withstand the maximum and minimum pressures and temperatures expected during operation.
- Bending Radius: The minimum bend radius should be considered to avoid kinking or damage to the hose.
- Application: The specific application (e.g., mobile equipment, industrial machinery, marine) will dictate the necessary material properties and performance requirements.
By carefully considering these factors, engineers and technicians can select the appropriate hydraulic hose materials to ensure optimal system performance, reliability, and safety.
How to Choose the Best Hydraulic Hose Material
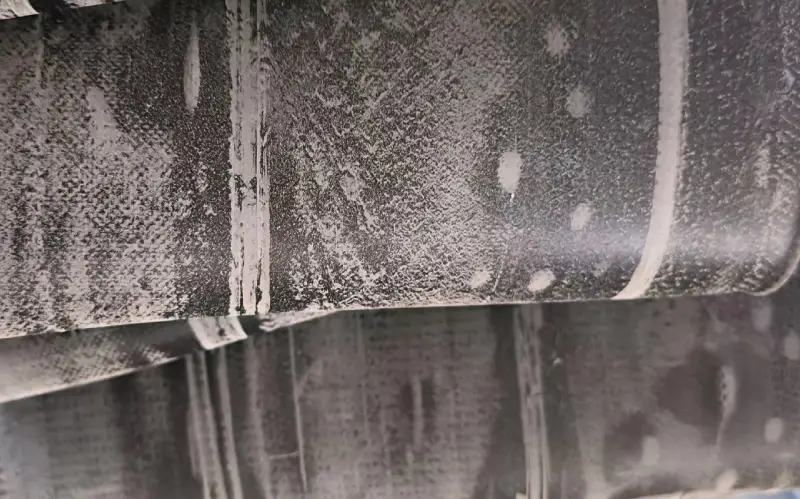
Selecting the right hydraulic hose material is crucial for the safety, efficiency, and longevity of your hydraulic system.
Here’s a breakdown of the key factors to consider:
1. Define Your Application:
- Pressure: Determine the maximum working pressure and potential pressure surges within the system.
- Temperature: Identify both the operating temperature range and the ambient temperature extremes.
- Fluid Compatibility:
- Type of Fluid: Mineral oil, synthetic fluids, water-glycol mixtures, etc.
- Fluid Contamination: Consider the presence of abrasives or other contaminants.
- Environmental Factors:
- Exposure to Weather: UV radiation, ozone, moisture, extreme temperatures.
- Chemical Exposure: Potential contact with solvents, acids, or other chemicals.
- Abrasion: Risk of rubbing against machinery, sharp objects, or rough surfaces.
- Flexibility and Bend Radius: Consider the required flexibility for installation and operation.
- Fire Hazard: Determine if fire resistance is necessary.
2. Evaluate Material Properties:
- Inner Tube:
- Resistance to Hydraulic Fluids: Compatibility with the specific fluid is paramount.
- Temperature Resistance: Ability to withstand both high and low temperatures.
- Abrasion Resistance: Protects against wear and tear from internal flow.
- Reinforcement Layer:
- Pressure Resistance: Strength to withstand operating pressures and surges.
- Flexibility: Allows for ease of installation and movement.
- Fatigue Resistance: Withstands repeated pressure cycles without failure.
- Outer Cover:
- Abrasion Resistance: Protects against external damage.
- Weather Resistance: Resists environmental factors.
- Chemical Resistance: Protects against exposure to chemicals.
- Fire Resistance: In applicable situations.
3. Consult with Experts:
- Hose Manufacturers: Utilize their expertise and product catalogs.
- Hydraulic System Engineers: Seek guidance on material selection for your specific application.
- Industry Standards: Refer to relevant industry standards (e.g., SAE, ISO) for guidance.
4. Consider Safety Factors:
- Pressure Rating: Select a hose with a working pressure rating significantly higher than the maximum expected pressure.
- Temperature Rating: Choose a hose that can comfortably handle both the operating and ambient temperature extremes.
5. Obtain Samples and Conduct Testing:
- Compatibility Testing: If possible, conduct compatibility tests between the hose material and the hydraulic fluid.
- Performance Testing: Evaluate the hose’s performance under simulated operating conditions.
By carefully considering these factors and consulting with experts, you can select the most suitable hydraulic hose material for your application, ensuring optimal system performance, reliability, and safety.
Hydraulic Hose Manufacturing Process
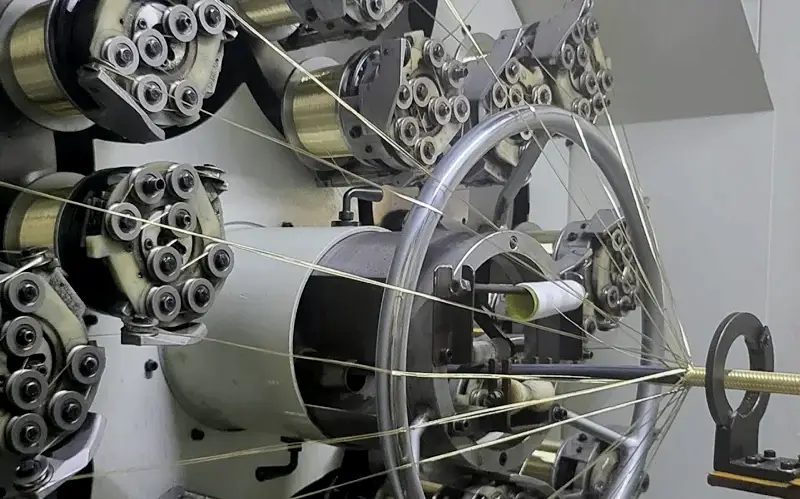
The manufacturing process for hydraulic hoses involves several key steps:
1. Raw Material Preparation:
- Rubber Compounds: Different rubber compounds are formulated based on the specific application and performance requirements. These compounds may include natural rubber, synthetic rubbers (like nitrile, neoprene, or EPDM), and various additives (fillers, reinforcements, antioxidants).
- Reinforcement Materials: Steel wire, synthetic fibers (like nylon or polyester), or a combination of both are prepared for the reinforcement layer.
2. Inner Tube Extrusion:
- The rubber compound for the inner tube is fed into an extruder, a machine that heats and forces the rubber through a die, forming a continuous tube.
- The extruded tube is carefully inspected for defects and dimensional accuracy.
3. Reinforcement Layer Application:
- Braiding: For braided hoses, steel wires or synthetic fibers are interwoven around the inner tube using specialized braiding machines.
- Spiraling: For spirally wound hoses, steel wires are wound helically around the inner tube.
4. Outer Cover Extrusion:
- The rubber compound for the outer cover is extruded over the reinforced inner tube, forming a protective layer.
5. Vulcanization:
- The assembled hose is subjected to a curing process called vulcanization. This involves heating the hose in a controlled environment (e.g., autoclave, steam chamber) to cross-link the rubber molecules, improving its strength, durability, and resistance to heat, oil, and abrasion.
6. Testing and Inspection:
- Rigorous testing is conducted at various stages of the manufacturing process to ensure quality and performance. This may include:
- Burst pressure tests: To determine the maximum pressure the hose can withstand before rupturing.
- Working pressure tests: To verify the hose’s ability to withstand operating pressures.
- Dimensional inspections: To ensure the hose meets the specified dimensions.
- Visual inspections: To check for any defects or imperfections.
7. Finishing and Packaging:
- The finished hoses are cut to the desired lengths, marked with identification markings (e.g., size, pressure rating), and packaged for shipping.
Key Considerations:
- Quality Control: Throughout the entire manufacturing process, stringent quality control measures are implemented to ensure consistent product quality and minimize defects.
- Automation: Many stages of the manufacturing process are automated, improving efficiency and reducing labor costs.
- Continuous Improvement: Manufacturers are constantly seeking ways to improve their manufacturing processes, such as developing new materials, optimizing production techniques, and implementing advanced quality control systems.
This comprehensive process ensures that hydraulic hoses are manufactured to the highest standards, providing reliable and durable performance in demanding applications.
Conclusion
In conclusion, the choice of hydraulic hose material is crucial for the safe and efficient operation of hydraulic systems. Factors such as pressure, temperature, and the nature of the fluid being conveyed must be carefully considered when selecting the appropriate hose. By understanding the properties and limitations of different materials, engineers and technicians can make informed decisions that optimize system performance and minimize the risk of failure.
Ready to upgrade your hydraulic system with high-quality hoses? Contact us today for a free quote on our wide selection of wholesale hydraulic hoses. Our team of experts can help you choose the perfect hose for your specific application needs. Visit our website or call us to get started.