If you’ve ever observed heavy machinery in action – whether it’s an excavator digging, a forklift lifting, or a press-shaping metal – you’re witnessing the power of hydraulics. At the heart of these robust systems are hydraulic hoses, critical conduits that transmit pressurized fluid to power motion.
While they might seem like simple tubes, understanding the individual hydraulic hose components is key to appreciating their strength, durability, and the vital role they play in countless industrial and mobile applications.
Why Understanding Hydraulic Hose Components is Crucial
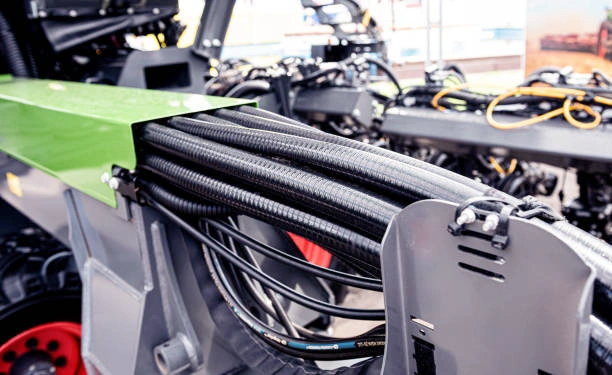
For anyone working with hydraulic systems – from maintenance technicians and engineers to equipment operators and purchasers – this knowledge isn’t just academic; it’s practical, economical, and safety-critical. Knowing how each component functions helps us troubleshoot issues, select the right replacement parts, optimize system performance, and, most importantly, prevent costly downtime and dangerous failures. We’ve seen firsthand how a little knowledge here can save a lot of headaches, and often, a lot of money.
What Are the Basic Hydraulic Hose Components?
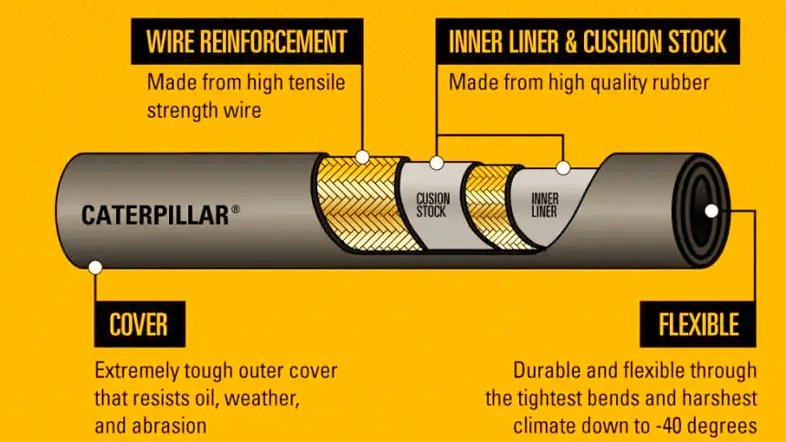
At its most fundamental, a hydraulic hose is a composite structure, typically made up of three primary layers, each serving a distinct and critical purpose. These layers work in harmony to contain high-pressure fluids, resist degradation, and protect against external elements. Understanding this layered construction is the first step in comprehending the resilience of hydraulic hose components.
1. The Inner Tube (Liner): The Fluid’s Pathway
The inner tube is arguably the most critical of the hydraulic hose components, as it’s the part that’s in direct contact with the hydraulic fluid. Its primary function is to contain the fluid without leaking or contaminating it. But it’s not just about containment; the inner tube must be chemically compatible with the specific hydraulic fluid being used.
- Material Composition: Inner tubes are usually made from various synthetic rubbers like nitrile (NBR), chloroprene (CR/Neoprene), EPDM, or even thermoplastic materials. The choice depends heavily on the fluid type (e.g., petroleum-based oils, synthetic fluids, water-based emulsions) and the operating temperature range.
- Key Properties: We look for excellent fluid compatibility, low permeability (to prevent fluid from seeping through), and resistance to degradation from high temperatures. A degraded inner tube can lead to leaks, fluid contamination, and ultimately, system failure.
2. Reinforcement Layers: The Strength Behind the Pressure
If the inner tube is the fluid’s pathway, the reinforcement layers are the muscle of the hydraulic hose. These layers are what give the hose its incredible pressure-withstanding capabilities, allowing it to handle thousands of pounds per square inch (psi) without bursting. Without robust reinforcement, a hydraulic hose would simply swell and rupture under pressure.
- Material Composition: Reinforcement typically consists of high-tensile steel wire or synthetic fibers (like rayon or aramid fiber).
- Construction Styles: We primarily see two common construction styles for reinforcement:
- Braided: One or more layers of braided wire or fiber. This provides flexibility and is common in medium-pressure hoses (e.g., SAE 100R1, 100R2).
- Spiral: Multiple layers of spiraled steel wire, often in opposing directions. This construction offers superior pressure resistance and is used in high-pressure and very high-pressure hoses (e.g., SAE 100R12, 100R13, 100R15).
- Number of Layers: The number of reinforcement layers directly correlates with the hose’s pressure rating. More layers generally mean a higher working pressure.
- Key Role: The reinforcement layers resist expansion under pressure and provide the structural integrity necessary for the hose to perform reliably.
3. The Outer Cover: The Protector
The outer cover is the outermost layer of the hydraulic hose and serves as its first line of defense against the external environment. Its role is crucial for the longevity and durability of the entire assembly.
- Material Composition: Typically made from synthetic rubbers (like synthetic rubber compounds, sometimes with PVC blends) that are resistant to abrasion, ozone, weathering, and chemicals.
- Key Properties: We expect the outer cover to protect the inner reinforcement layers from:
- Abrasion: Rubbing against machinery, other hoses, or rough surfaces.
- Environmental Degradation: UV radiation, ozone, moisture, and extreme temperatures.
- Chemical Exposure: Spills of various chemicals, fuels, or oils.
- Importance: A damaged outer cover can expose the reinforcement layers to corrosion or physical damage, severely compromising the hose’s pressure integrity and leading to premature failure.
Beyond the Hose Itself: Fittings and Adapters
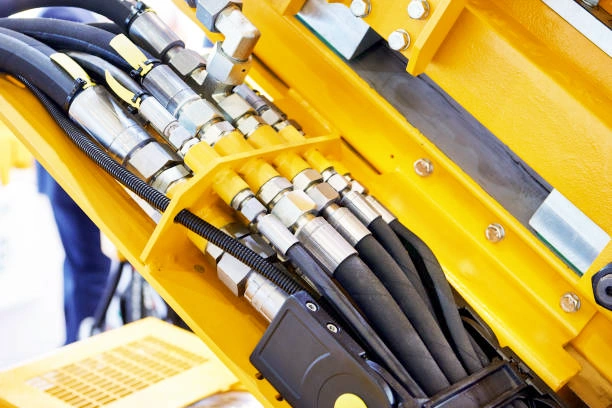
While the hose body is central, it’s incomplete without the vital hydraulic hose components that connect it to the rest of the system: fittings and adapters. These parts ensure a secure, leak-free connection, enabling fluid to flow from one component to another.
4. Hose Fittings (End Connections): The Critical Link
Hose fittings, also known as end connections or couplings, are the metallic components crimped or otherwise attached to the ends of the hose. They provide the mechanical connection to pumps, valves, cylinders, and other hydraulic system parts.
- Material: Usually made from steel, stainless steel, brass, or other alloys, depending on the application’s pressure, corrosion, and fluid compatibility requirements.
- Attachment Methods:
- Crimped: The most common method. A crimping machine compresses a ferrule or collar onto the hose, securing the fitting.
- Reusable: Designed to be disassembled and reassembled, allowing for field repairs, though less common in modern high-pressure applications.
- Push-Lok: For low-pressure applications, specific hoses and fittings allow for a simple push-on assembly without clamps.
- Types of Fittings: There’s a vast array of fitting types, each designed for specific connection standards. Common types we encounter include:
- NPT (National Pipe Taper): Common in North America, creates a seal by threading taper.
- SAE (Society of Automotive Engineers): Many variants like JIC (Joint Industry Council) 37° flare, O-ring Boss (ORB), and Four-Bolt Flange.
- Metric: DIN (Deutsches Institut für Normung) and BSP (British Standard Pipe) are common internationally.
- JIC (37° Flare): A very common type with a 37-degree flared seating surface.
- ORFS (O-Ring Face Seal): Provides an excellent leak-free seal using an O-ring on the face.
- Key Function: They create a robust, leak-proof connection that can withstand the high pressures and vibrations inherent in hydraulic systems. Selecting the correct fitting type and ensuring proper crimping are paramount for safety and system integrity.
5. Adapters: Bridging the Gaps
Adapters are often used in conjunction with fittings to connect different thread types, sizes, or to change flow direction. They provide flexibility in system design and can help simplify plumbing.
- Function: Allow connections between components that wouldn’t directly mate due to different thread types (e.g., NPT to JIC), sizes, or angles.
- Types: Come in various shapes (straight, elbow, tee) and thread combinations.
- Material: Similar to fittings, typically steel or stainless steel.
- Importance: They offer versatility in routing and connecting, but it’s crucial to select adapters with appropriate pressure ratings for the system.
Auxiliary Hydraulic Hose Components: Enhancing Performance and Longevity
Beyond the core hose and connection parts, several other hydraulic hose components or accessories play a significant role in protecting the hose, extending its lifespan, and ensuring safe operation.
6. Hose Guards/Protectors
These are external coverings designed to shield the hose from abrasion, impacts, and crushing.
- Materials: Often plastic spirals, fabric sleeves, or metal spring guards.
- Benefits: Significantly extends hose life in demanding environments, preventing wear and tear that can lead to premature failure.
7. Clamps and Mounts
Used to secure hoses in place, preventing excessive movement, kinking, and abrasion against other components.
Function: Proper clamping reduces stress on hose assemblies and prevents tangling, which can lead to chafing and damage.
8. Strain Relievers
These are specialized fittings or devices that reduce the stress on the hose at the point where it connects to a fitting, particularly important in applications with dynamic motion.
Benefit: Prevents kinking and fatigue at the most vulnerable part of the hose assembly.
9. Quick Disconnect Couplings
Allow for fast, tool-free connection and disconnection of hydraulic lines, useful in applications where attachments are frequently changed.
Function: Designed to minimize fluid loss and air inclusion during connection/disconnection.
What is the Difference Between R1 and R2 Hydraulic Hoses?
The main difference between SAE 100R1 and SAE 100R2 hydraulic hoses lies in their reinforcement layers, which directly impact their pressure ratings and suitability for different applications.
SAE 100R1 hoses feature a single layer of high-tensile steel wire braid for reinforcement. This makes them suitable for medium-pressure hydraulic lines and general industrial systems. They offer good flexibility and are a common choice where robust pressure capabilities are needed, but extreme pressures aren’t the norm.
In contrast, SAE 100R2 hoses are constructed with two layers of high-tensile steel wire braid reinforcement. This additional layer significantly increases their pressure capacity, allowing them to handle higher working pressures and more demanding applications. We typically use 100R2 hoses in heavy-duty machinery, construction equipment, and other systems where sustained high pressure and impulse resistance are critical. While both types have oil-resistant inner tubes and weather-resistant outer covers, the double braiding of the 100R2 provides superior strength and durability.
The Synergy of Hydraulic Hose Components
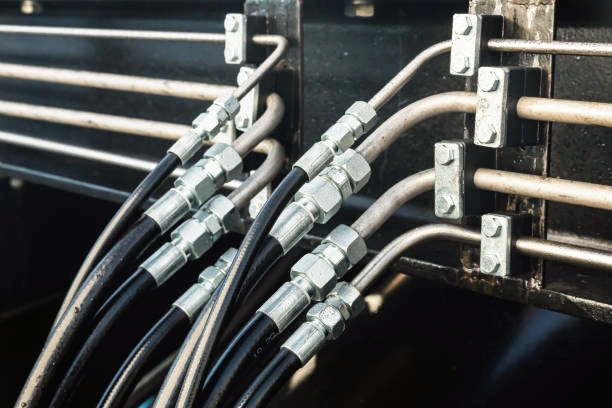
Ultimately, the performance and safety of any hydraulic system depend on the quality and compatibility of all its hydraulic hose components. Each layer of the hose, along with the fittings, adapters, and protective accessories, must work in perfect synergy. A chain is only as strong as its weakest link, and in hydraulics, a single faulty or mismatched component can compromise the entire system, leading to leaks, inefficient operation, or even catastrophic failure.
Key Considerations When Selecting Components:
- Fluid Compatibility: Ensure all components are compatible with the hydraulic fluid.
- Pressure Rating: Match components to the system’s maximum working pressure and burst pressure requirements.
- Temperature Range: Verify components can withstand the operating and ambient temperatures.
- Application Environment: Consider abrasion, chemical exposure, UV, and other environmental factors.
- Industry Standards: Always adhere to relevant standards (e.g., SAE, ISO, DIN) for hose and fitting selection.
Conclusion
Understanding the individual hydraulic hose components empowers us to make informed decisions that translate directly into safer, more efficient, and more reliable hydraulic systems. It’s not just about replacing a worn part; it’s about comprehending why that part is there, what its limitations are, and how it contributes to the whole. By investing in this knowledge, we can ensure our hydraulic machinery operates at its peak, minimize downtime.