In the world of industrial hoses, material selection is paramount for performance and longevity. Many commonly encounter challenges with hoses degrading when exposed to oils, fuels, or chemicals, leading to frequent replacements and costly downtime.
This blog delves into NBR rubber, a material specifically engineered to overcome these common issues. We’ll explore its unique properties and the significant advantages it brings to hose manufacturing, ensuring reliable and durable solutions for demanding fluid transfer applications.
What is NBR?
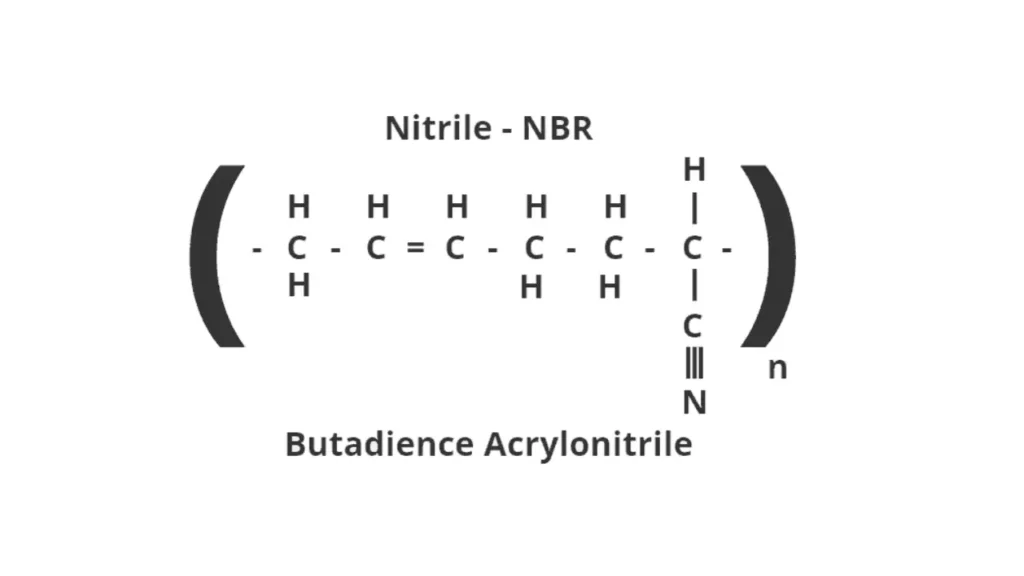
NBR is the common abbreviation for Nitrile Butadiene Rubber, also known as Buna-N or acrylonitrile butadiene rubber. It is a type of synthetic rubber highly valued for its excellent resistance to petroleum-based oils, fuels, and many other chemicals.
NBR Rubber Hose Benefits
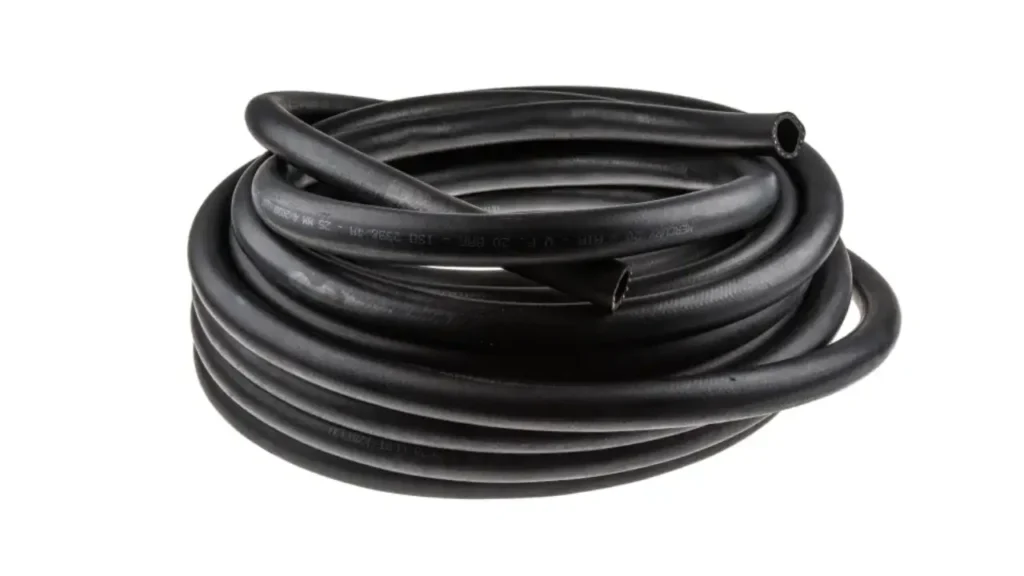
NBR rubber hoses are a popular choice across many industries due to a combination of beneficial properties, offering a balance of performance and cost-effectiveness. Their unique chemical composition, particularly the presence of acrylonitrile, grants them specific advantages that make them suitable for diverse applications.
Here are some key benefits of NBR rubber hoses:
- Excellent Oil and Fuel Resistance: NBR hoses are highly resistant to degradation from petroleum-based oils, fuels (including gasoline and diesel), hydraulic fluids, and greases. This is their most significant advantage, preventing swelling, softening, and deterioration that can lead to leaks and system failures.
- Good Abrasion and Tear Resistance: NBR rubber provides good resistance to abrasion, cuts, and tears, which contributes to the hose’s durability and extended service life in demanding industrial environments where hoses might be subjected to rubbing or physical stress.
- Wide Temperature Operating Range: NBR hoses can operate effectively across a broad temperature spectrum, typically from around -40°C to +100°C (with some specialized grades reaching higher). This versatility allows them to function reliably in various climatic conditions and industrial processes.
- Good Flexibility and Elasticity: NBR hoses offer a good balance of flexibility and elasticity, making them relatively easy to route and install in complex systems. This property also helps them withstand bending and continuous movement without cracking or kinking, ensuring consistent flow.
- Cost-Effectiveness: Compared to higher-performance elastomers like FKM or silicone, NBR rubber hoses are generally more economical. This makes them a cost-effective solution for a wide range of applications where their specific resistance properties are sufficient, offering a good balance between performance and budget.
NBR Rubber for Different Types of Hose
NBR rubber’s versatility and excellent resistance profile make it an ideal material for manufacturing a diverse array of hoses, each designed for specific applications where contact with oils, fuels, or certain chemicals is prevalent. The ability to vary the acrylonitrile content during its production allows manufacturers to fine-tune the hose’s properties to meet demanding performance requirements, balancing factors like flexibility, temperature range, and resistance.
Different types of hoses made from NBR include:
- Fuel Hoses: NBR is extensively used for automotive fuel lines, diesel transfer hoses, and aviation fuel hoses due to its superior resistance to gasoline, diesel, and biofuels, preventing degradation and leaks in critical fuel systems.
- Hydraulic Hoses: The inner tubes of many hydraulic hoses are made from NBR because of its compatibility with various hydraulic fluids, allowing for efficient power transfer without material breakdown, even under high pressure.
- Oil Transfer Hoses: From industrial machinery lubrication lines to heavy-duty oil suction and discharge hoses, NBR’s resistance to mineral and synthetic oils ensures reliable performance and longevity in applications involving oil transport.
- Chemical Transfer Hoses: While not universally resistant to all chemicals, NBR is suitable for transferring diluted acids, bases, and many industrial chemicals, especially those with petroleum bases, making it a common choice in chemical processing and manufacturing.
- Food-Grade Hoses (with specific NBR formulations): Certain NBR compounds are formulated to meet FDA standards, making them suitable for transferring fatty and oily foodstuffs, such as dairy products, edible oils, and sauces, without imparting taste or odor.
Density of NBR Rubber
The density of NBR rubber is not a fixed value but rather a range that varies depending on its specific formulation and compounding. Generally, the density of NBR rubber typically falls between 1.00 and 1.30 g/cm³.
This range is influenced by several factors:
- Acrylonitrile (ACN) Content: The percentage of acrylonitrile in the NBR polymer affects its density. Higher ACN content generally increases the density, along with enhancing oil and fuel resistance.
- Fillers: The addition of reinforcing fillers like carbon black or silica, which are common in rubber compounding, will increase the overall density of the NBR material. Different types and loadings of fillers can significantly alter the density.
- Plasticizers and Oils: Plasticizers are often added to NBR compounds to improve flexibility and processability. These additives typically have a lower density than the base polymer, thus reducing the overall density of the compounded rubber.
- Curing System and Cross-linking: The curing process and the degree of cross-linking can also have a subtle impact on the final density.
- Manufacturing Methods: Different production processes, such as high-pressure molding, can yield products with slightly higher densities compared to low-pressure methods.
Therefore, the specific density of an NBR compound is tailored by manufacturers to meet the precise performance requirements of its intended application, balancing properties like flexibility, strength, and chemical resistance.
NBR Nitrile Rubber Properties
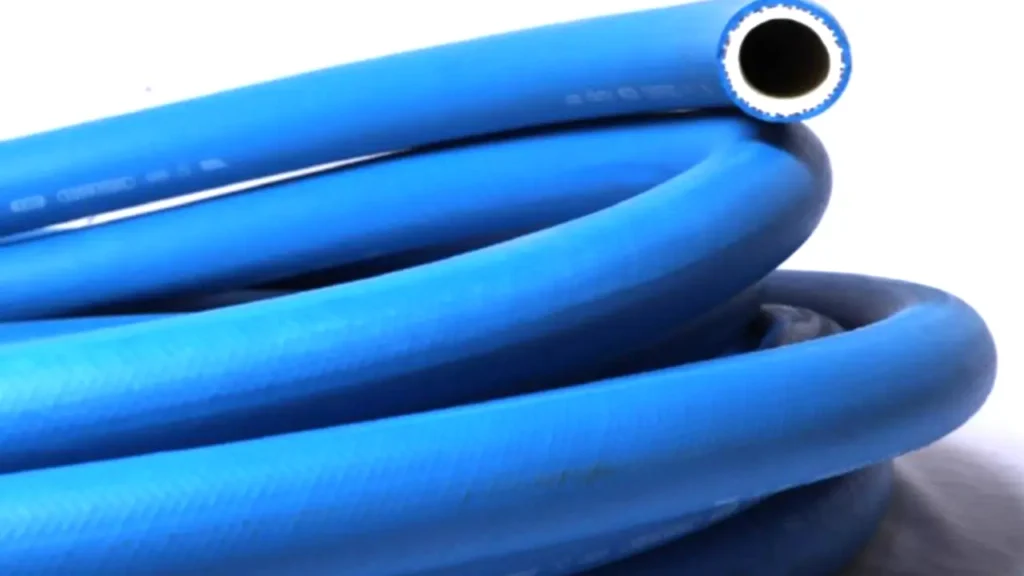
NBR rubber, or Nitrile Butadiene Rubber, possesses a range of beneficial properties that make it a highly versatile and widely used synthetic elastomer. Its key characteristic is its excellent resistance to petroleum-based oils, fuels, and many chemicals, which is primarily influenced by its acrylonitrile (ACN) content. Higher ACN levels generally lead to superior oil and fuel resistance, albeit with a slight reduction in low-temperature flexibility.
Beyond chemical resistance, NBR offers:
- Good Abrasion and Tear Resistance: This property contributes to the material’s durability, allowing NBR components to withstand wear and tear in demanding applications.
- Good Mechanical Properties: NBR exhibits good tensile strength, elongation at break, and decent compression set resistance, meaning it can return to its original shape after being compressed, crucial for reliable sealing.
- Wide Operating Temperature Range: NBR typically performs well in temperatures ranging from approximately -40°C to +100°C (some specialized grades can extend this range).
- Good Flexibility and Elasticity: While not as flexible as natural rubber, NBR maintains good flexibility, making it suitable for hoses, seals, and other parts that require bending or dynamic movement.
- Fair to Good Water and Alcohol Resistance: NBR generally holds up well against water and various types of alcohols.
- Low Gas Permeability: This property makes it effective in applications where gas leakage needs to be minimized.
However, NBR also has some limitations, including poor resistance to ozone, UV radiation, and aromatic hydrocarbons (like benzene and toluene). For applications exposed to these elements, protective compounding or alternative materials are often necessary.
NBR Rubber Chemical Compatibility
NBR rubber is highly valued for its chemical compatibility with a range of substances, making it suitable for numerous industrial applications. Its resistance primarily stems from its acrylonitrile (ACN) content; higher ACN levels generally lead to better resistance.
- Oils and Fuels: NBR offers outstanding resistance to petroleum-based oils, diesel fuel, gasoline, hydraulic fluids, and greases. This makes it a preferred material for fuel lines, oil seals, and hydraulic hoses.
- Water and Alcohols: NBR typically exhibits good resistance to water, including hot water (though not steam), and various alcohols. This broad compatibility extends its use in many fluid transfer and sealing applications.
- Diluted Acids and Bases: NBR can withstand exposure to many dilute acids and bases. However, its resistance diminishes significantly with strong oxidizing acids or concentrated alkaline solutions, which can cause swelling or degradation.
- Limited Aromatic and Chlorinated Solvents: NBR has poor resistance to aromatic hydrocarbons like benzene and toluene, and chlorinated solvents such as trichloroethylene. Exposure to these can lead to considerable swelling and material breakdown.
- Poor Ozone and UV Resistance: A significant limitation of NBR is its poor resistance to ozone, UV radiation, and general weathering. For outdoor applications or environments with high ozone levels, NBR typically requires protective additives or coatings, or an alternative material should be considered.
NBR Rubber Chemical Resistance
NBR rubber, or Nitrile Butadiene Rubber, is highly valued for its chemical resistance, which makes it a preferred choice in applications involving various fluids. Its resistance profile is primarily determined by its acrylonitrile (ACN) content; generally, a higher ACN percentage provides better resistance to oils and fuels, though it can slightly reduce flexibility in very cold temperatures.
NBR’s chemical resistance:
- Petroleum-Based Oils and Fuels: NBR exhibits excellent resistance to a wide array of petroleum-based products including crude oil, gasoline, diesel fuel, hydraulic fluids, and greases. This makes it ideal for components in automotive fuel systems, oil seals, and industrial hydraulic hoses.
- Water and Alcohols: NBR generally holds up well against water and various types of alcohols (e.g., methanol, ethanol). This broad compatibility allows its use in many sealing and fluid transfer applications where exposure to these common liquids occurs.
- Diluted Acids and Bases: NBR offers good resistance to many dilute acids and bases. However, its performance degrades significantly when exposed to strong oxidizing acids or highly concentrated alkaline solutions, which can lead to swelling, softening, or breakdown of the material.
- Aromatic Hydrocarbons and Polar Solvents: NBR has poor resistance to aromatic hydrocarbons like benzene, toluene, and xylene, as well as polar solvents such as acetone, MEK (methyl ethyl ketone), and chlorinated solvents like trichloroethylene. Contact with these substances can cause considerable swelling, softening, and rapid degradation.
- Ozone and UV Radiation: A notable limitation of NBR rubber is its poor resistance to ozone, ultraviolet (UV) radiation, and general weathering. Prolonged exposure to outdoor elements or environments with high ozone concentrations can lead to surface cracking and material degradation, making it less suitable for unprotected outdoor applications unless specially compounded with protective additives.
NBR Rubber Manufacturing Process
The manufacturing of NBR rubber involves several key steps, transforming raw monomers into a versatile synthetic elastomer. This process is crucial for dictating the final properties and performance characteristics of the rubber, making it suitable for diverse industrial applications.
Step 1: Emulsion Polymerization
Nitrile rubber production begins with emulsion polymerization. Acrylonitrile and butadiene monomers are dispersed in water with emulsifiers and initiators. This mixture forms an emulsion where polymerization occurs, creating tiny polymer particles suspended in water, forming a latex.
Step 2: Shortstopping and Monomer Recovery
Once the desired conversion of monomers to polymer is reached, a “shortstop” agent is added to halt the polymerization process. Following this, unreacted monomers are recovered from the latex using steam stripping. This step ensures product purity and allows for recycling of unreacted raw materials.
Step 3: Coagulation
The NBR latex then undergoes coagulation, where chemicals like calcium chloride or aluminum sulfate are added. These coagulating agents cause the NBR polymer particles to clump together and separate from the water phase, forming a crumb-like rubber material.
Step 4: Washing and Drying
The crumb rubber obtained from coagulation is thoroughly washed to remove residual emulsifiers, salts, and other impurities. After washing, the rubber crumbs are dried in ovens to remove moisture, preparing the NBR for the next stage of processing and compounding.
Step 5: Compounding and Mixing
The dried NBR rubber is then subjected to compounding, where various additives are mixed in. These can include reinforcing fillers (like carbon black), plasticizers, antioxidants, and curing agents. This precise mixing process in internal mixers or roll mills is critical for achieving the desired final properties of the NBR, such as hardness, strength, and improved resistance.
NBR Rubber Temperature Range
NBR rubber offers a versatile operating temperature range, making it suitable for a wide array of applications. However, its specific performance at temperature extremes can vary depending on the acrylonitrile (ACN) content and specific compounding. Generally, NBR compounds are designed to perform reliably within a continuous service temperature range.
Here’s a breakdown of NBR’s temperature range:
- Standard Operating Range: Most standard NBR compounds are suitable for continuous use in temperatures from approximately -40°C (-40°F) to +100°C (212°F). This range covers many common industrial and automotive applications.
- High Temperature Performance: For short intermittent periods, NBR can withstand slightly higher temperatures, sometimes up to +120°C (248°F), or even briefly up to 140-150°C for specialized high-temperature formulations, particularly when in contact with oils. Prolonged exposure above its recommended maximum can lead to hardening, cracking, and loss of flexibility.
- Low Temperature Flexibility: NBR’s low-temperature flexibility is influenced by its ACN content. Lower ACN content generally improves low-temperature performance, with some specialized compounds able to operate as low as -50°C (-58°F) or even -65°C (-85°F). However, at temperatures below its rated minimum, NBR can become brittle and lose its elasticity, compromising its sealing ability.
Conclusion
In conclusion, NBR rubber’s exceptional resistance to oils and fuels, coupled with its durability and flexibility, positions it as an indispensable material in hose manufacturing. Understanding its benefits highlights why it’s the go-to choice for reliable fluid transfer in diverse industrial settings.
For businesses seeking consistent quality and competitive pricing for their hose needs, partnering with a trusted manufacturer is key.
Secure your supply of high-performance NBR rubber hoses wholesale by connecting with Gushan Rubber, ensuring your operations benefit from superior, long-lasting products.