Hydraulic hose bursts can have catastrophic consequences, leading to equipment damage, injuries, and even fatalities. Understanding the factors that contribute to hose failure is crucial for preventing such incidents.
In this blog post, we will delve into the common causes of hydraulic hose bursts and discuss preventive measures to ensure the safety and reliability of your hydraulic systems.
Why Do Hydraulic Hose Burst
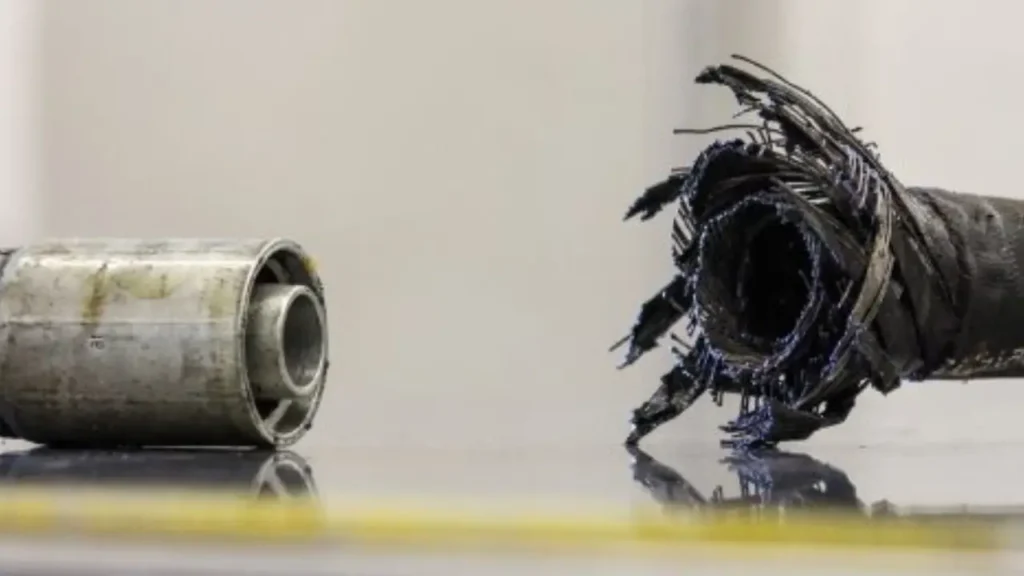
The hydraulic hose burst is one of the hydraulic hose failure reasons, which can lead to significant safety risks, equipment damage, and costly downtime. Understanding the root causes of these failures is crucial for implementing effective preventive measures.
1. Excessive Pressure
- Overpressurization: Operating the hydraulic system beyond the hose’s rated pressure is a common cause of burst failures. This can occur due to system malfunctions, operator error, or design flaws.
- Pressure Surges: Sudden pressure spikes, often caused by pump cavitation, valve slamming, or rapid load changes, can exceed the hose’s pressure rating and lead to catastrophic failure.
- System Malfunction: Faulty pumps, valves, or other components can cause excessive pressure buildup in the hydraulic system, increasing the risk of hose failure.
2. Improper Installation and Maintenance
- Incorrect Fitting: Improperly installed fittings can weaken the hose and create stress points, leading to leaks and potential bursts.
- Excessive Bending: Exceeding the hose’s minimum bend radius can cause internal damage and weaken the hose material.
- Insufficient Support: Inadequate support for the hose can lead to excessive stress and vibration, accelerating wear and tear.
- Lack of Regular Inspection: Failing to inspect hoses regularly for signs of wear, damage, or leaks can lead to unexpected failures.
3. External Damage
- Abrasion: Friction against nearby components can wear down the hose’s outer cover and reinforcement layers.
- Puncture: Impact from sharp objects or debris can cause punctures in the hose, leading to fluid leakage.
- Chemical Exposure: Exposure to incompatible chemicals can degrade the hose material, reducing its strength and flexibility.
4. Heat Damage
- High-Temperature Exposure: Prolonged exposure to high temperatures can accelerate the aging process of the hose material, making it more susceptible to failure.
- Thermal Fatigue: Repeated exposure to temperature fluctuations can cause thermal stress and fatigue, leading to cracking and eventual failure.
5. Fluid Incompatibility
- Chemical Degradation: Using incompatible hydraulic fluids can degrade the hose material, reducing its strength and flexibility.
- Corrosion: Certain fluids can cause corrosion of the hose’s metal components, leading to weakened connections and potential leaks.
Here’s a table showing some potential reasons why hydraulic hoses burst:
Reason | Description |
---|---|
High Pressure | Exceeding the hose’s pressure rating, sudden pressure surges. |
Excessive Heat | High temperatures weaken the hose material, degrade hydraulic fluid. |
Abrasion | Wear and tear from rubbing against other components. |
Fatigue | Repeated flexing and bending weakens the hose structure. |
Improper Installation | Incorrect fittings, improper crimping, sharp bends. |
Chemical Exposure | Exposure to incompatible chemicals degrades the hose material. |
Age and Wear | Natural deterioration over time due to use and environmental factors. |
By understanding these common causes of hydraulic hose failure, you can implement preventive measures to minimize the risk of accidents and equipment damage. Regular inspection, proper maintenance, and the use of high-quality hoses are essential for ensuring the safety and reliability of your hydraulic systems.
Hydraulic Hose Burst Pressure
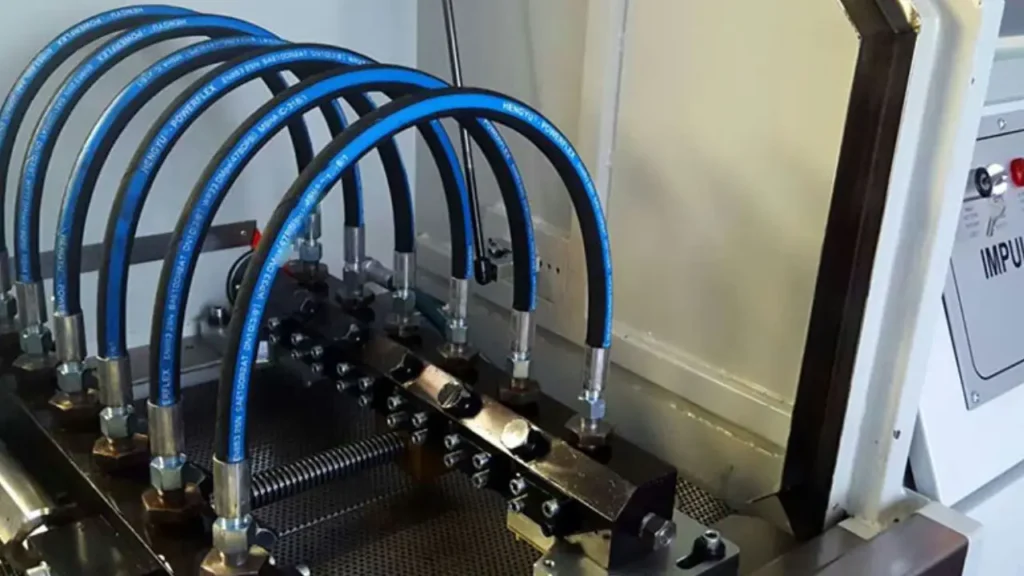
Hydraulic hose burst pressure refers to the maximum pressure a hose can withstand before rupturing. This pressure is typically significantly higher than the hose’s working pressure rating.
Why is burst pressure important?
- Safety: A higher burst pressure provides a safety margin, reducing the risk of catastrophic failure.
- Reliability: A hose with a higher burst pressure is less likely to fail under normal operating conditions.
- Peace of Mind: Knowing that your hoses can withstand unexpected pressure spikes can give you peace of mind.
Factors Affecting Burst Pressure:
- Hose Material: The type of material used in the hose construction significantly affects its burst pressure.
- Hose Design: The design of the hose, including the number of layers and reinforcement, influences its burst pressure.
- Temperature: Extreme temperatures can affect the hose’s material properties and reduce its burst pressure.
- Fluid Compatibility: Using incompatible fluids can degrade the hose material, lowering its burst pressure.
It’s crucial to select hydraulic hoses with a suitable burst pressure rating for your specific application. Always consult the manufacturer‘s specifications and consider factors such as working pressure, temperature range, and fluid compatibility.
Remember: While a high burst pressure is important, it’s equally important to avoid exceeding the hose’s working pressure rating during normal operation. Proper maintenance, regular inspection, and timely replacement of worn-out hoses are essential for ensuring the safety and reliability of your hydraulic system.
Hydraulic Hose Burst Protection Sleeve
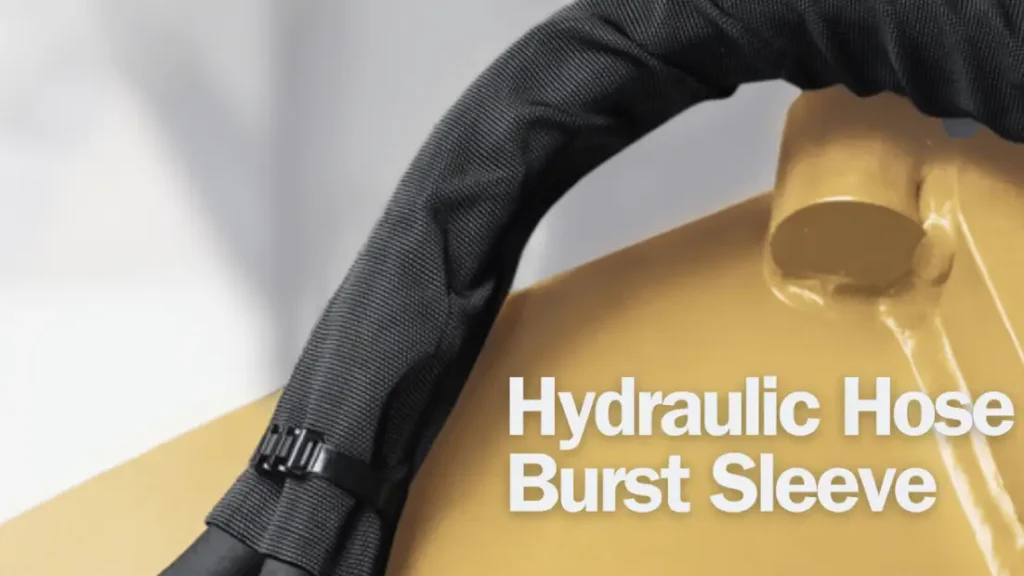
A hydraulic hose burst protection sleeve is a safety device designed to minimize the impact of a hydraulic hose rupture.
Here’s how burst protection sleeve for hydraulic hoses work and their benefits:
How they work:
Containment: The primary function is to contain the forceful ejection of hydraulic fluid when a hose bursts.This prevents the fluid from spraying uncontrollably, which can cause:
- Injury to personnel: High-pressure fluid can cause serious injuries, including eye damage and skin lacerations.
- Equipment damage: The spray can damage nearby equipment, electronics, and even cause fires.
- Energy Absorption: Some sleeves are designed to absorb some of the energy released during a burst, reducing the force of the fluid ejection.
Benefits:
- Improved Safety: Significantly reduces the risk of injury to personnel and damage to equipment.
- Reduced Downtime: Containing the fluid and minimizing damage can help reduce equipment downtime for repairs and cleaning.
- Environmental Protection: Prevents the release of hydraulic fluid into the environment, which can be harmful to soil and water.
- Compliance: In many industries, burst protection sleeves are required by safety regulations and industry standards.7
Types of Sleeves:
- Nylon Braided Sleeves: Common and cost-effective, offering good abrasion resistance and some burst containment.
- Metal Braided Sleeves: Provide higher levels of burst protection and abrasion resistance, but can be more expensive.
- High-Tech Composite Sleeves: Offer advanced features like flame resistance, chemical resistance, and superior burst containment.
Key Considerations:
- Hose Size and Pressure: Choose a sleeve that is compatible with the size and pressure rating of the hydraulic hose.
- Application: Consider the specific application and environment (e.g., temperature, chemicals, abrasion) to select the appropriate sleeve material.
- Installation: Proper installation is crucial for effective burst protection. Follow manufacturer‘s instructions carefully.
Conclusion
Hydraulic hose bursts can lead to significant safety risks, equipment damage, and costly downtime. By understanding the common causes of hose failure and implementing preventive measures, you can minimize the risk of such incidents. Regular inspection, proper maintenance, and the use of high-quality hoses are essential for ensuring the reliability and safety of your hydraulic systems.
Ready to upgrade your hydraulic systems with high-quality hoses?
Contact us today to explore our wide range of hydraulic hoses and fittings. Our expert team can help you select the right products for your specific application and provide expert advice on installation and maintenance.