Hydraulic hoses are essential components in countless industries, from construction and agriculture to manufacturing and automotive. They are responsible for transmitting high-pressure hydraulic fluid to power various equipment and machinery.
To ensure optimal performance and safety, it’s crucial to properly crimp hydraulic hoses. Crimping involves securing the fittings to the hose ends, creating a leak-proof and durable connection.
In this blog post, we’ll delve into the intricacies of hydraulic hose crimping. We’ll cover the essential tools and equipment, step-by-step procedures, safety precautions, and troubleshooting tips. Whether you’re a seasoned mechanic or a DIY enthusiast, this guide will provide you with the knowledge and skills needed to crimp hydraulic hoses effectively.
Let’s get started!
What Is Hydraulic Hose Crimping
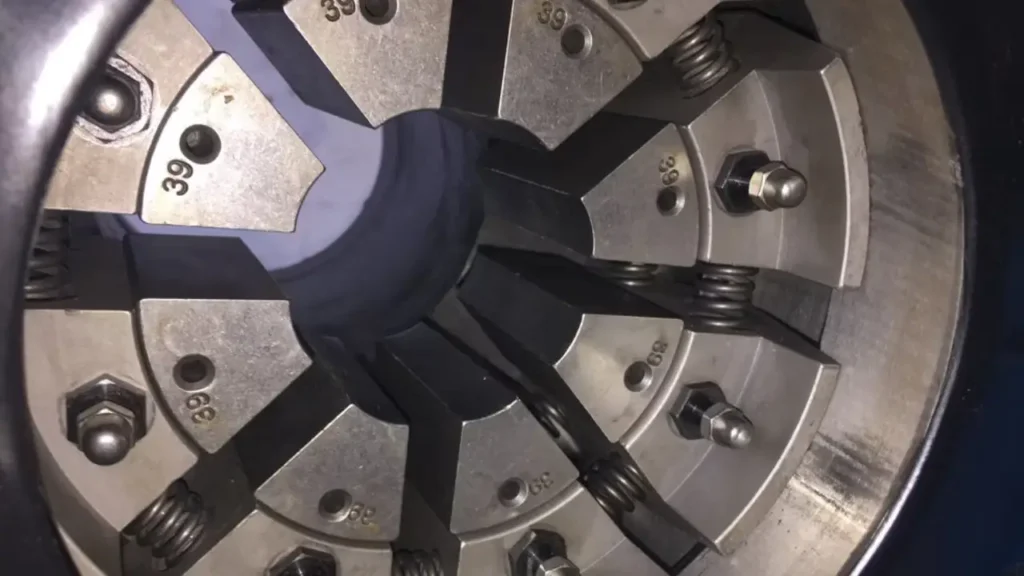
Hydraulic hose crimping is a process used to securely attach a fitting to a hydraulic hose. This process is crucial for ensuring the safety and reliability of hydraulic systems, as it prevents leaks and maintains proper pressure.
Hydraulic Hose Crimping Tool
Hydraulic hose crimping tools are essential equipment for repairing and maintaining hydraulic systems. They are used to securely connect hydraulic hoses to fittings by crimping ferrules onto the hose ends.
Types of Hydraulic Hose Crimping Tools:
There are several types of hydraulic hose crimping tools available, each with its own advantages and disadvantages:
- Manual Hydraulic Hose Crimpers: These are portable and easy to use, making them ideal for on-site repairs. However, they require significant physical effort to operate.
- Electric Hydraulic Hose Crimpers: These tools are powered by electricity and offer greater ease of use and faster crimping speeds compared to manual crimpers. They are suitable for both shop and field use.
- Pneumatic Hydraulic Hose Crimpers: These tools are powered by compressed air and offer even faster crimping speeds than electric crimpers. They are best suited for high-volume crimping applications in workshops.
Choosing the Right Crimping Tool:
When choosing a hydraulic hose crimping tool, consider the following factors:
- Hose Size: The tool should be capable of crimping the specific size of hose you need to work with.
- Crimping Force: The tool should generate enough force to properly crimp the ferrule onto the hose.
- Portability: If you need to use the tool on-site, a portable model is essential.
- Ease of Use: The tool should be easy to operate and maintain.
- Cost: The cost of the tool will vary depending on the features and capabilities.
By carefully considering these factors, you can select the best hydraulic hose crimping tool for your specific needs.
How to Crimp Hydraulic Hoses
Step 1. Prepare Your Workspace and Tools
The first step in the process of crimping a hydraulic hose is to establish a clean and well-organized workspace. This ensures that all necessary tools are readily accessible and that there is ample room to maneuver the hose and fitting assembly.
The essential tools required for this task include a hose cutter, a hose deburring tool, a fitting insertion tool, a hydraulic hose crimping machine, and the appropriate dies that are compatible with the specific hose and fitting combination being used.
Step 2. Select the Right Hose and Fitting
Once the workspace is prepared, the next step is to carefully select the appropriate hose and fitting. The hose must be chosen based on its compatibility with the fluid, pressure, and temperature requirements of the intended application.
Factors such as reinforcement, flexibility, and chemical resistance should also be considered when selecting a hydraulic hose. The fitting, on the other hand, must be compatible with both the hose size and thread type, as well as the crimping machine and dies that will be used to secure the connection.
Step 3. Measure and Cut the Hose
After selecting the appropriate hose and fitting, the hose must be accurately measured and cut to the desired length using a hose cutter.
It is crucial to ensure that the cut is clean and precise to avoid any potential damage to the fitting or the crimping process.
Step 4. Deburr the Hose End
Following the cutting process, the cut end of the hose must be deburred using a deburring tool. This step is essential to remove any sharp edges that may have formed during the cutting process.
Removing these sharp edges prevents potential damage to the fitting and ensures a clean and smooth connection.
Step 5. Insert the Fitting
The next step involves inserting the fitting into the hose. To facilitate this process, a light lubricant can be applied to both the fitting and the inside of the hose.
A fitting insertion tool is then used to gently push the fitting onto the hose to the specified depth. It is important to ensure that the fitting is fully seated to prevent any potential leaks or issues during the crimping process.
Step 6. Prepare the Crimping Machine
Once the fitting is inserted, the crimping machine must be prepared. This involves selecting the correct dies for the specific hose and fitting combination being used.
The crimping machine must also be calibrated to the appropriate pressure and stroke settings to ensure a proper and secure crimp.
Step 7. Crimp Hydraulic Hose
With the crimping machine prepared, the hose and fitting assembly is carefully positioned into the machine, aligning it with the selected dies.
The crimping machine is then activated, applying pressure to the fitting and forming a secure bond with the hose. Once the crimping cycle is complete, the hose assembly is released from the machine.
Step 8. Inspect the Crimped Joint
The final step in the hydraulic hose crimping process is to thoroughly inspect the crimped joint. This involves a visual inspection to identify any potential defects, such as misalignment, cracks, or excessive deformation.
Additionally, a dimension check is performed using a caliper or other measuring tool to verify that the crimp diameter meets the specified requirements.
By following these detailed steps and prioritizing safety, individuals can successfully crimp hydraulic hoses and ensure the integrity of their hydraulic systems.
Importance of Proper Crimping:
- Prevents Leaks: A properly crimped joint ensures a leak-free connection, preventing fluid loss and potential safety hazards.
- Maintains Pressure: A secure crimp maintains the system’s pressure, ensuring optimal performance of hydraulic equipment.
- Ensures Longevity: Proper crimping extends the life of the hydraulic hose and fittings, reducing the need for frequent replacements.
Safety Considerations:
- Use Proper Tools: Utilize specialized crimping tools designed for the specific hose and fitting types.
- Wear Protective Gear: Always wear safety glasses, gloves, and other protective equipment when handling hydraulic hoses and fittings.
- Follow Manufacturer‘s Instructions: Adhere to the manufacturer‘s guidelines for hose and fitting selection, cutting, and crimping procedures.
How to Use a Hydraulic Hose Crimper
Here’s a comprehensive guide on how to use a hydraulic hose crimper:
1. Prepare Your Workspace and Tools:
- Ensure a clean and organized workspace with sufficient room to maneuver the hose and crimping machine.
- Gather the necessary tools:
- Hydraulic hose crimping machine
- Correct dies for your hose and fitting combination
- Hose cutter
- Hose deburring tool
- Fitting insertion tool
- Safety gear (safety glasses, gloves, etc.)
2. Select the Right Hose and Fitting:
- Choose a hose that is compatible with the fluid, pressure, and temperature requirements of your application.
- Select fittings that match the hose size and thread type. Ensure they are compatible with the crimping machine and dies you have.
3. Measure and Cut the Hose:
- Measure the desired length of the hose using a measuring tape.
- Mark the hose at the measured length and cut it cleanly using a hose cutter.
4. Deburr the Hose End:
- Use a deburring tool to remove any sharp edges from the cut end of the hose. This prevents damage to the fitting and ensures a secure connection.
5. Insert the Fitting:
- Apply a light lubricant to the fitting and the inside of the hose to facilitate insertion.
- Use a fitting insertion tool to gently push the fitting onto the hose to the specified depth.
6. Prepare the Crimping Machine:
- Select the correct dies for your hose and fitting combination.
- Calibrate the crimping machine to the appropriate pressure and stroke settings according to the manufacturer‘s instructions.
7. Crimp the Hose:
- Place the hose and fitting assembly into the crimping machine, aligning it with the dies.
- Engage the crimping machine’s lever or button, which will apply pressure to the fitting and crimp it onto the hose.
- Hold the lever or button until the crimping cycle is complete, which is typically indicated by an audible signal or a pressure gauge reaching a predetermined level.
- Release the lever or button and carefully remove the hose assembly from the crimping machine.
8. Inspect the Crimped Joint:
- Visually inspect the crimped joint for any defects, such as misalignment, cracks, or excessive deformation.
- Use a caliper or other measuring tool to verify the crimp diameter and ensure it meets the manufacturer‘s specifications.
9. Clean Up and Dispose:
- Clean the crimping machine and remove any debris from the workspace.
- Dispose of any used materials or lubricants according to local regulations.
Additional Tips:
- Always wear safety gear when using a hydraulic hose crimper.
- Read and understand the manufacturer‘s instructions for your specific crimping machine and dies.
- Practice on scrap hoses before crimping actual hoses to familiarize yourself with the process.
- If you are unsure about any step or encounter any issues, consult a qualified technician or refer to the manufacturer‘s manual.
By following these steps and prioritizing safety, you can effectively use a hydraulic hose crimper to create secure and reliable connections for your hydraulic systems.
Conclusion
Hydraulic hose crimping is a complex process that requires specialized tools and expertise. By understanding the critical steps involved, you can ensure the safety and reliability of your hydraulic systems. However, for optimal performance and longevity, it’s often best to entrust this task to professionals.
Need reliable, expertly crimped hydraulic hoses? Look no further. [Your Company Name] offers top-quality hydraulic hose crimping services tailored to your specific needs. Our skilled technicians use state-of-the-art equipment to deliver precise and durable crimps.
Contact us today to discuss your hydraulic hose requirements and experience the difference of professional crimping.