In the intricacies of hydraulic systems, selecting the right hose is crucial for optimal performance, safety, and longevity. Each hose has its unique advantages to meet specific application needs. In this guide, we will take a deep dive into the differences between 2-Wire vs 4 Wire Hydraulic Hose to help you understand which hose is the best choice for your needs.
Understanding Hydraulic Hose Reinforcement
Before we delve into the specifics of 2 wire vs 4 wire hydraulic hose, it’s essential to grasp the concept of reinforcement. This internal structure is what gives a hydraulic hose its ability to withstand immense pressure. Without proper reinforcement, a hose would simply burst under the forces exerted by hydraulic fluid. The type, amount, and configuration of this reinforcement are critical determinants of a hose’s performance characteristics, including its pressure rating, flexibility, and overall durability.
What is 2-Wire Hydraulic Hose
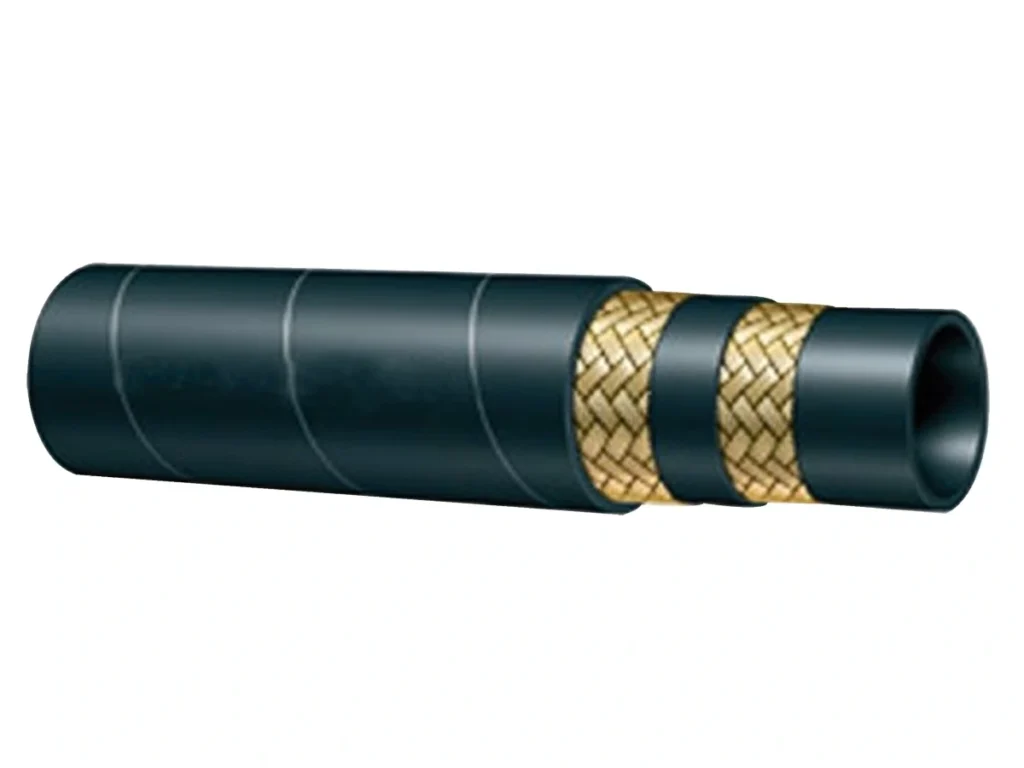
2 wire hydraulic hose is an essential material for countless hydraulic applications and is known for its versatile performance. Its design prioritizes the balance between pressure-bearing capacity, flexibility, and cost-effectiveness, making it a popular choice across a wide range of industries. Understanding its construction and characteristics is the first step to understanding its role in a hydraulic system.
The core of a 2 wire hydraulic hose consists of an inner tube, typically made from synthetic rubber, designed to resist hydraulic fluids. Surrounding this tube are two layers of braided high-tensile steel wire. These wire layers are crucial for handling the internal pressure. Finally, an outer cover protects the hose from environmental elements, abrasion, and ozone. This multi-layered construction provides significant strength while maintaining a degree of flexibility, which is essential for routing in diverse machinery layouts.
What is 4 Wire Hydraulic Hose
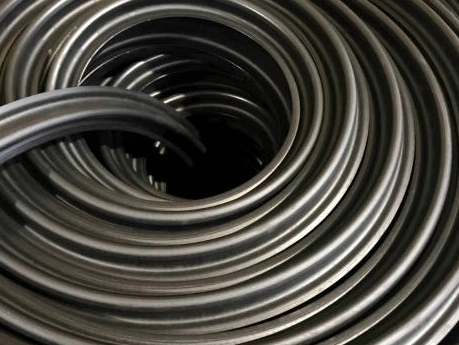
4-wire hydraulic hose is engineered for the most demanding applications where extreme pressure and rugged durability are non-negotiable. Its construction deviates significantly from the 2-wire variant, focusing on maximum strength to endure the most severe operational conditions imaginable.
What sets a 4-wire hydraulic hose apart is its formidable reinforcement. Instead of braids, it features four (or more, sometimes six) layers of spiral-wound high-tensile steel wire. These layers are wound tightly in alternating directions, providing unparalleled structural integrity and burst resistance.
Like the 2-wire hose, it has an inner tube and a tough outer cover, but the spiraled wire layers are the key to its superior pressure handling. This design makes the 4-wire hose less flexible but exponentially stronger, ideal for intense, high-impulse applications.
Key Performance Differences: 2 Wire vs 4 Wire Hydraulic Hose
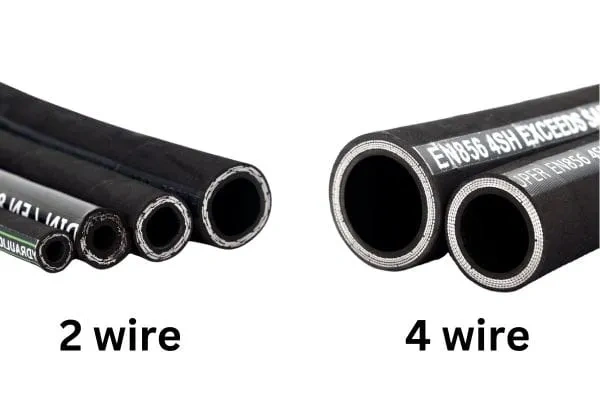
The fundamental difference in construction between 2 wire vs 4 wire hydraulic hose directly translates into distinct performance characteristics. Understanding these differences is crucial for selecting the correct hose that will not only perform optimally but also ensure the safety and longevity of your hydraulic system. We’ll compare them across several critical parameters that influence their suitability for various applications.
Feature | 2 Wire Hydraulic Hose | 4 Wire Hydraulic Hose |
Reinforcement | 2 braided layers of steel wire | 4 or more spiral-wound layers of steel wire |
Pressure Rating | High (e.g., 2,500 – 5,000 PSI) | Very High / Extremely High (e.g., 4,000 – 6,000+ PSI) |
Flexibility | Good / Moderate Flexibility | Lower Flexibility / More Rigid |
Bend Radius | Tighter bend radius possible | Larger bend radius required |
Weight | Lighter | Heavier |
Abrasion Resistance | Good | Excellent (often with thicker covers) |
Cost | Generally lower | Generally higher |
Impulse Cycles | Good for moderate impulse applications | Excellent for high-impulse applications |
Pressure Handling: A Critical Factor in 2 Wire vs 4 Wire Hydraulic Hose
When comparing 2 wire vs 4 wire hydraulic hose, pressure handling is arguably the most significant differentiator. The ability of a hose to withstand internal pressure dictates the type of work it can perform and the forces it can safely manage. Our choice here directly impacts the efficiency and safety of the entire hydraulic circuit.
A 2 wire hydraulic hose is engineered for significant pressure. Typically, depending on the hose diameter, it can comfortably handle working pressures ranging from 2,500 PSI to 5,000 PSI. This makes it suitable for a vast array of industrial and mobile hydraulic systems that operate under substantial, but not extreme, stress. It’s the go-to for general-purpose high-pressure lines where a balance of performance and flexibility is needed.
In stark contrast, the 4 wire hydraulic hose is built for extreme pressure. Its spiral-wound reinforcement allows it to withstand working pressures that can easily exceed 4,000 PSI and reach up to 6,000 PSI or even higher for specialized applications. This exceptional capability makes it indispensable for heavy-duty machinery subject to enormous forces and frequent pressure surges, such as in mining equipment, large excavators, and heavy-duty presses.
Flexibility and Bend Radius
Another crucial aspect when weighing 2 wire vs 4 wire hydraulic hose is their respective flexibility and required bend radius. These characteristics greatly influence ease of installation, routing within complex machinery, and ultimately, the longevity of the hose assembly itself. Understanding this trade-off is key to preventing premature hose failure due to kinking or excessive stress.
A 2 wire hydraulic hose offers superior flexibility compared to its 4-wire counterpart. The braided wire reinforcement allows for a tighter bend radius, meaning it can be routed more easily in confined spaces or around sharp corners without compromising its integrity. This flexibility is a significant advantage in applications where space is limited or where the hose needs to accommodate movement without excessive strain on fittings.
The multi-layered spiral-wound reinforcement of a 4 wire hydraulic hose makes it considerably more rigid. This increased stiffness means it requires a larger minimum bend radius. Forcing a 4-wire hose into a tighter bend than recommended can lead to kinking, internal damage, and premature failure. Therefore, careful consideration of routing paths and available space is vital when designing systems utilizing 4-wire hoses to ensure proper installation and operation.
Abrasion Resistance and Durability
When working in harsh conditions, the external durability of a hydraulic hose is just as important as its internal strength. Choosing the right hydraulic hose for its abrasion resistance and overall durability helps us select a product that can withstand the physical stress of its working environment, thereby extending its service life and reducing the frequency of replacement.
Both 2 wire and 4 wire hydraulic hoses come with robust outer covers designed to resist abrasion, ozone, and weathering. However, given the extreme applications for which 4-wire hoses are designed, they often feature thicker and more heavy-duty outer covers. This enhanced external protection makes 4 wire hydraulic hose exceptionally resilient against cuts, impacts, and constant rubbing, which are common occurrences in demanding industrial and construction settings.
While 2 wire hydraulic hoses offer good abrasion resistance suitable for many applications, the sheer scale of the forces and environmental exposure faced by equipment using 4-wire hoses often necessitates that extra layer of external ruggedness. Investing in the right level of durability prevents costly downtime and ensures that your hydraulic lines remain intact and functional, even under relentless physical stress.
Cost and Application Considerations: Making the Right Investment
The decision between 2 wire vs 4 wire hydraulic hose ultimately comes down to a balance of performance requirements, application specifics, and, of course, cost. Understanding where each hose excels in real-world scenarios will guide you in making the most economical and effective choice for your hydraulic system. It’s not just about what a hose can do, but what it should do for your specific needs.
Application Type | Best Fit for 2 Wire Hydraulic Hose | Best Fit for 4 Wire Hydraulic Hose |
General Industrial Machinery | Manufacturing lines, lift trucks, standard automation, general fluid power transfer. | Heavy presses, large metal fabrication equipment, extreme shock load applications. |
Mobile Construction Equipment | Smaller excavators, skid steers, backhoes, auxiliary lines, less extreme duty cycles. | Large excavators, bulldozers, cranes, mining equipment, primary boom/arm lines. |
Agricultural Equipment | Heavy-duty tillage equipment, large forestry machinery, and applications with constant extreme pressure surges. | Container handlers, port equipment, and very large lifting applications. |
Material Handling | Tractors, harvesters (many implements), and general hydraulic lines on farm machinery. | Drilling rigs, blow-out preventers (BOPs), and high-pressure well service lines. |
Oil & Gas | Lower pressure auxiliary lines, some non-critical transfer lines. | Drilling rigs, blow-out preventers (BOPs), high-pressure well service lines. |
Maintenance & Repair | Versatile for general repairs and replacements where extreme pressure isn’t the primary concern. | Critical repairs on heavy equipment where original specifications demand extreme durability and pressure rating. |
Conclusion
In the world of hydraulic systems, the debate between two-line hydraulic hose and four-line hydraulic hose is not about which one is inherently “better”, but rather which one is “better” for a specific application. We have seen that while two-line hydraulic hoses offer excellent versatility, flexibility, and cost-effectiveness for a variety of high-pressure needs, four-line hydraulic hoses are the clear winners in extreme pressure, high-pulse environments that require high strength.
What specific hydraulic applications are you considering using these hoses for? We would be happy to assist you professionally.